Скачать .zip |
Реферат: Проект алмазной обогатительной фабрики
Экономическая часть
6.1. Общие сведения
Но современном этапе развития общества значительно возрастают масштабы производства, связанные с техническим прогрессом в добывающем, обогатительном, металлургическом и обрабатывающих производствах.
С увеличением объемов капитальных вложений и размеров производственных фондов ставиться – повышения эффективности общественного производства на основе внедрения в производство научно-технического прогресса.
Одни и те же общественные потребности могут быть удовлетворены с помощью новой техники, нового строительства или расширения, реконструкции действующих предприятий, внедрения новых технологий.
6.1. Расчет проектной технологической схемы
6.1.2. Капитальные затраты на оборудования
№ | Наименование оборудования | Балансовая стоимость, тыс. руб. | Кол-во, шт. | Общая стоимость, тыс. руб. | Мощность, кВт/час |
1 | Классификатор 1КСН-12 | 333 334 | 1 | 333 334 | 15 |
2 | Классификатор 1КСН-5 | 99 167 | 3 | 297 501 | 3 |
3 | Дробилка 45-4680-GR | 53 380 000 | 2 | 106 760 000 | 320 |
4 | Грохот ГВII-50 | 322 600 | 1 | 332 600 | 8 |
5 | Грохот ГИСТ-51 | 402 000 | 1 | 402 000 | 18,5 |
6 | Грохот ГИЛ-42 | 287 875 | 1 | 287 875 | 7,5 |
7 | Грохот ГИЛ-11 | 49 018 | 1 | 49 018 | 1,1 |
8 | Сепаратор ЛС-20-05-2М | 2 375 000 | 6 | 14 250 000 | 36 |
9 | Сепаратор МО-105 | 1 506 750 | 1 | 1 506 750 | 1,5 |
10 | Сепаратор СВ3-1500 | 72 000 | 1 | 72 000 | - |
11 | Сепаратор ПФМ-5М | 686 280 | 1 | 686 280 | 5,5 |
12 | Модуль ТСС | 14 450 000 | 1 | 27 463 473 | 136,3 |
Итого | 152 532 498 | 607,7 |
6.1.3. Затраты на здания и сооружения составляет 50 % от общей
стоимости оборудования, т. руб.
Сз= Соб ·0,5=76 266 249,
гдеСоб – стоимость оборудования, т. руб;
6.1.4. Сумма капитальных затрат, тыс. руб.
К=Соб+Сз,
гдеСоб – стоимость оборудования, т. руб;
Сз – затраты на здания и сооружения, т. руб.
К=152 532 498+76 266 249=228 798 747 т. руб.
6.1.5. Монтаж оборудования составляет 20 % от общей стоимости
оборудования, т. руб.
Моб= Соб·0,2=30 506 499,6 т. руб.
6.1.6. Амортизация зданий и сооружений, т. руб.
Аз=(Сз·Наз)/100,
гдеНаз – норма амортизации зданий и сооружений (Наз =1,7)
Аз=(76 266 249·1,7)/100=1 296 526,2 т. руб. в год
Сумма амортизационных отчислений, т. руб:
∑А=Аз+Аоб,
гдеАоб – годовая сумма амортизации оборудования (амортизационные отчисления составляют 15 % от общей стоимости)
∑А=1 296 526,2+22 879 874,7=24 176 400,9
6.1.7. Затраты на содержание и эксплуатацию основных фондов
определяется в размере 7% от их стоимости
Зс.э.=(Соб+Сз)·0,07,
гдеЗс.э. – затраты на содержание и эксплуатацию основных фондов
Зс.э.=(152 532 498+76 266 249)·0,07=16 015 912,2 т. руб. в год
6.1.8. Затраты на ремонт (50 % от суммы амортизационных отчислений)
Зр=0,5·∑А,
гдеЗр – затраты на ремонт.
Зр=0,5·24 176 400,9=12 088 200,4 т. руб. в год
6.1.9. Затраты на электроэнергию
Зэ.э.=Р·Цэ,
гдеР=∑(Руст. ·Ким) ·24·341=(607,7·0,8)·24·341=3 978 733,4 кВт/год:
Р – установочная мощность, кВт/час;
Ким – коэффициент использования мощности;
24 – количество работы цеха в сутки, дней
341 – количество рабочих дней в год, дней
Цэ=5,04 руб/кВт·час.
Зэ.э=3 978 733,4·5,04=20 052 816,5 т. руб. в год
6.1.10. Затраты на воду
Зв=Цв·Нсв.в.·Q,
гдеНсв.в. – расход свежей воды, м3/т (Нсв.в.=33,534 м3/т);
Цв – цена за 1 м3 воды, руб (Цсв.в.=0,19 руб);
Q – объем перерабатываемой руды в год, т/год.
Q=Траб. час·74,61=499961,61т/в год
Зв=0,19·33,534·499961,61=3 185 485,39 т. руб.
6.1.11. Затраты на вспомогательные материалы 10 % от стоимости
оборудования
Зв.м.=15 253 249,8 т. руб.
6.1.12. Затраты на заработную плату
Ззп=Зср·Nсп·12,
гдеЗср – среднемесячная заработная плата, т. руб;
Nсп – списочная численность, чел.;
12 – число месяцев в году.
Ззп=17 290,1·76·12=15 768 571,2 т. руб. в год
Таблица. Заработная плата рабочего персонала
№ | Затраты | Кол-во | Разряд | Ставка | К-во часов в мес. | Начисл. | Налоги 14 % | Зар. плата | ИТОГО |
1 2 | Начальник Инженер | 1 1 | 11 10 | 168 168 | |||||
3 | Мастер | 4 | 8 | 21 | 180 | 26 990 | 23 211,4 | 92 845,6 | |
4 | Энергетик | 1 | 7 | 20 | 168 | 24 800 | 21 328 | 21 328 | |
5 | Механик | 1 | 7 | 20 | 168 | 24 800 | 21 328 | 21 328 | |
6 | Дробильщик | 4 | 6 | 19 | 180 | 21 610 | 18 584,6 | 74 338,4 | |
7 | Сепараторщик РЛС | 4 | 6 | 17 | 180 | 21 230 | 18 257,8 | 73 031,2 | |
8 | Грохотовщик | 4 | 5 | 16 | 180 | 17 040 | 14 654,4 | 58 617,6 | |
9 | Оператор | 4 | 7 | 20 | 180 | 20 800 | 17 888 | 71 552 | |
10 | Оператор Отсадки | 4 | 5 | 16 | 180 | 18 040 | 15 514,4 | 62 057,6 | |
11 | Сепараторщик винтовой сепарации | 4 | 4 | 16 | 180 | 17 040 | 14 654,4 | 58 617,6 | |
12 | Флотатор | 4 | 6 | 18 | 180 | 19 420 | 16 701,2 | 66 804,8 | |
13 | Сепараторщик жир. сепарации | 4 | 6 | 18 | 180 | 19 420 | 16 701,2 | 66 804,8 | |
14 | Сепараторщик магн. сепарации | 4 | 6 | 18 | 180 | 19 420 | 16 701,2 | 66 804,8 | |
15 | Электрослесарь | 4 | 6 | 17 | 180 | 19 230 | 16 537,8 | 66 151,2 | |
16 | Слесарь | 4 | 6 | 17 | 180 | 19 230 | 16 537,8 | 66 151,2 | |
17 | Мастер КИПиА | 4 | 7 | 20 | 180 | 24 800 | 21 328 | 85 312 | |
18 | Дежурный КИПиА | 4 | 6 | 17 | 180 | 17 230 | 14 817,8 | 59 271,2 | |
19 | Мастер службы режима | 2 | 7 | 20 | 180 | 24 800 | 21 328 | 42 656 | |
20 | Доводчик | 8 | 5 | 16 | 180 | 18 040 | 15 514,4 | 124 115,2 | |
21 | Конролер | 4 | 5 | 16 | 180 | 18 040 | 15 514,4 | 62 057,6 | |
22 | Мастер ОТК | 2 | 7 | 19 | 180 | 23 040 | 19 814,4 | 39 628,8 | |
ИТОГО | 76 | 1 279 473,6 |
6.1.13. Сумма текущих годовых затрат
С=∑А+Зр+Зсэ+Зээ+Ззп+Звм, т. руб
С=24 176 400,9+12 088 200,4+16 015 912,2+
+20 052 816,5+15 768 571,2+15 253 249,8=13 355 151 т. руб. в год
6.1.14. Себестоимость продукции проектной фабрики, руб/т
Сп.ф..=(Зс.э.+0,15·К)/Qп.ф.,
гдеЗс.э. - затраты на содержание и эксплуатацию основных фондов;
К - капитальные затраты;
Qп.ф. - объем перерабатываемой руды, т/год.
Сп.ф..= (16 015 912,2 +0,15·228 798 747)/499961,61=100,6 руб/т
6.1.15 Себестоимость продукции действующей фабрики, руб/т
Сд.ф.=(Зс.э.+0,15·К)/Qд.ф.,
ГдеЗс.э. - затраты на содержание и эксплуатацию основных фондов 25 144 982,1 т.руб;
К - капитальные затраты составляют 359 214 032,7 т.руб;
Qл.ф. - объем перерабатываемой руды 785 000, т/год.
Сд.ф.= (25 144 982,1+0,15·654 000 119,3)/ 785 000=157 руб/т
6.1.16 Эффективность проектной фабрики, т. руб./год
ε=( Сд.ф - Сп.ф.)· Qп.ф.,
гдеСд.ф - себестоимость продукции действующей фабрики;
Сп.ф - себестоимость продукции проектной фабрики;
Qп.ф - объем перерабатываемой руды, т/год.
ε=(157 – 100,6.)· 500000=28 200 000
6.1.17 Коэффициент окупаемости проектной фабрики
Ко=( Зс.э+0,15·К)/ ε,
гдеЗс.э. - затраты на содержание и эксплуатацию основных фондов;
К - капитальные затраты;
ε - эффективность проектной фабрики
Ко=(16 015 912,2 +0,15·228 798 747)/ 28 200 000=1,78
Охрана труда
7.1. Основные сведения
На обогатительный фабриках организацию производства строят по принципу создания наиболее благоприятных условий для рационального использования оборудования и рабочего времени в интересах роста производства, повышения производительности труда и создания его нормальных условий. Это особенно важно в связи с внедрением на обогатительных фабриках высокопроизводительного оборудования, которое должно быть максимально использовано во времени.
Научная организация труда – это организация труда, основанная на достижениях науки и передовом опыте, систематически внедряемых в производство. Научная организация труда позволяет наиболее эффективно соединить технику и людей в едином производственном процессе и обеспечивает повышение производительности труда, сохранение здоровья человека и постепенное превращение труда в первую жизненную необходимость.
Сформулированы следующие основные направления НОТ:
Разработка и внедрение рациональных форм разделения и кооперации труда;
Улучшение организации подбора, подготовки и повышения квалификации кадров;
Совершенствование организации и обслуживания рабочих мест;
Рационализация трудового процесса, внедрение передовых приемов и методов труда;
Совершенствование нормирования труда;
Внедрение рациональных форм и методов материального и морального стимулирования;
Укрепление дисциплины труда;
Улучшение условий труда.
7.2. Техника безопасности, промышленная санитария
и элетробезопасность
Система технических мероприятий и средств, предупреждающих воздействие на рабочих опасных производственных факторов, называется техникой безопасности, а система гигиенических и санитарно-технических мероприятий и средств, предотвращающих воздействие на работающих вредных производственных факторов, - производственной санитарией.
Главной задачей техники безопасности является профилактика производственного травматизма на основе исследований производственных процессов и безопасных приемов труда.
Учитывая специфику на обогатительных фабриках, их насыщенность современными высокопроизводительными агрегатами, всем рабочим и инженерно-техническим работникам обогатительных фабрик необходимо не только изучать и хорошо знать требования техники безопасности, инструкции и правила, но и обеспечивать их строгое выполнение.
Для предупреждения несчастных случаев большое значение имеет инструктаж по безопасным методам работ при эксплуатации и ремонте оборудования.
В соответствии ГОСТом проводятся следующие виды инструктажа:
- вводный инструктаж всех принимаемых на работу проводят инженер по охране труда, и работник пожарной охраны и газоспасательной службы, если такая имеется на предприятии.
- первичный инструктаж на рабочем месте проходят все работники, вновь поступившие на работу и прошедшие вводный инструктаж, переведенные из одного цеха в другой, а также переведенные с одной работы на другую в одном и том же цехе.
- периодический инструктаж проходят все работающие не реже чем через 6 мес. Его цель – повысить уровень знаний инструкций по охране труда.
- внеочередной инструктаж проводится при изменении технологического процесса или правил по охране труда, замене или модернизации оборудования, нарушении работникам требований безопасности труда, перерывах в работе свыше 60 дней.
- повседневный инструктаж проводится с работниками перед производством труда.
Производственные процессы, ведущееся в цехе, относятся к процессам, выполняемым при неблагоприятных метеорологических условиях при напряженной физической работе. Так как цех мокрый, предусмотрены помещения для сушки рабочей одежды и обогрева работающих.
К числу санитарно-бытовых помещения для удовлетворения санитарных и бытовых нужд трудящихся относятся: помещения для приема пищи, гардеробные, душевые, уборные, умывальные, курительные, прачечные, питьевого водоснабжения.
Здания санитарно-бытовых комбинатов примыкают непосредственно к производственным зданиям цеха. Бытовые помещения имеют изолированный выход, т.е. располагаются таким образом, чтобы не проходить через производственное помещение, но возможно ближе к рабочим местам.
Места отдыха устанавливают в виде кабин, в которых устанавливают скамьи со спинками. В эти кабинки подается питьевая вода.
Основные промышленные санитарные требования:
- проектирование, строительство, реконструкцию и эксплуатацию фабрик необходимо осуществлять в соответствии с требованиями «Санитарных правил для предприятий по добыче и обогащению рудных, нерудных и россыпных месторождений полезных ископаемых», «Санитарных норм проектирования промышленных предприятий», утвержденных Минздравом России;
- на всех вновь вводимых и реконструируемых объектах фабрик должны быть эффективные системы вентиляции, газоочистки, пылеулавливания и кондиционирования воздуха, обеспечивающие санитарные условия на рабочих местах и соответствующие действующим нормативам и проектам;
На каждой фабрике должны быть организованы службы по эксплуатации и контролю санитарно-технических систем и назначены ответственные лица.
на обогатительных фабриках должны быть разработаны мероприятия по систематическому улучшению условий труда на рабочих местах. Сроки приведения всех рабочих мест в соответствие с действующими нормами устанавливаются по согласованию с органами санитарного надзора; рабочих, занятых обогащением полезных ископаемых, обеспечивают спецодеждой, спецобувью и средствами индивидуальной защиты в соответствии с «Типовыми отраслевыми нормами бесплатной выдачи спецодежды, спецобуви и предохранительных приспособлений рабочим и служащим»;
- вентиляцию и отопление производственных зданий проектируют в соответствии с требованиями «Санитарных норм проектирования промышленных предприятий». Параметры воздушной среды во всех производственных помещениях обогатительной фабрики с постоянным или длительным (более 2 ч) пребыванием людей должны соответствовать требованиям ГОСТ 12.1.005-87.
- в помещениях, где располагаются оборудование с большой открытой водной поверхностью (флотационные машины, классификаторы, отсадочные машины и др.), необходимо предусмотреть устройства, обеспечивающие организованный сток конденсата;
- в цехах, где предусматривается мокрая уборка полов, а также во всех цехах с мокрым технологическим процессом полы должны быть с водонепроницаемым покрытием. Уклон полов для стока воды должен быть не менее 0,02 (1,8о). На основных проходах уклоны полов не должны превышать 0,04 (2,6о) и служебных проходах – не более 0,1 (6о).
- дробилки, транспортные ленты для подачи руды и промежуточных продуктов, места пересыпки и загрузки их в оборудование (питатели, агрегаты для сушки, электростатические и электромагнитные сепараторы, пеноприемные желоба флотомашин, емкости с растворами реагентов и др.) следует оборудовать укрытиями с аспирационными системами или системами гидрообеспыливания, работы которых должна быть сблокирована с производственным оборудованием. Блокировка устройств системы должна обеспечивать включение их за 3-5 мин до начала работы и включение их не ранее чем через 5 мин после остановки оборудования или работы без нагрузки.
- для оборудования, генерирующего вибрацию (дробилки, мельницы, грохота и др.), должен быть использован комплекс строительных, технологических и санитарно-технических мероприятий, обеспечивающих снижение вибрации до требований ГОСТа «ССБТ. Вибрация. Общие требования безопасности». Основное технологическое оборудование, создающее шум повышенных уровней (грохоты и др.), необходимо снабжать отдельными звукоизолирующими ограждениями, соответствующими требованиям стандарта «ССБТ. Шум. Общие требованиями безопасность».
По условиям электробезопасности различают электроустановки с напряжением до 1000 В включительно и с напряжением свыше 1000 В. Электродвигатели мельниц, дробилок, насосов (например, насосов 12ГРК) работают при напряжении 6000 В, а электродвигатели классификаторов, магнитных сепараторов, дешламаторов и другого оборудования – при напряжении 380 В. Все электроустановки опасны для жизни и здоровья обслуживающего персонала, поэтому каждый рабочий должен хорошо знать и выполнять все требования ПТЭ (Правил технической эксплуатации) и ПТБ (Правил технический безопасности) электроустановки. Необходимость строгого соблюдения правил безопасности обусловлена и тем, что помещения обогатительной фабрики относятся к категории особо опасных. Особая опасность помещений характеризуется наличием в них токопроводящей пыли, токопроводящих полов и повышенной влажностью.
К обслуживанию электроустановок должны допускаться обученные лица, имеющие удостоверение по профессии и соответствующую квалификационную группу по технике безопасности. Эксплуатация электродвигателей разрешается только при наличии специальных сетчатых ограждений, исключающих возможность прикосновения к токоведущим частям.
На каждом пусковом аппарате должна быть четкая подпись, указывающая технологический номер включающейся установки.
При необходимости проведения ремонтных работ электродвигатель должен быть остановлен, а на приводе выключателя вывешен плакат: «Не включать – работают люди».
Ремонтные работы разрешаются только при наличии специальной бирки. Положение о бирочной системе должен знать и выполнять каждый машинист мельниц.
Металлические корпуса установок, которые при нормальной работе не находятся под напряжением, но могут оказаться под ним в результате нарушения изоляции, должны быть заземлены.
Отступления от Правил техники безопасности при эксплуатации электроустановок запрещены.
7.3. Меры безопасности при обслуживании технологического и
транспортного оборудования
Для предупреждения производственного травматизма технологическое оборудование устанавливают в производственных помещениях в соответствии с действующими правилами, обеспечивая свободный проход к оборудованию для его обслуживания и ремонта.
При установке оборудования в производственных помещениях соблюдают минимальные расстояния между смежным оборудованием и от стен.
Расстояние между выступающими частями машин, фундаментов, ограждений и стенами зданий, с учетом укрепленных на них трубопроводов, должно быть не менее: 1,5м для основных проходов; 1 м для рабочих проходов; 0,7 м для рабочих проходов между стеной и машиной и для местных сужений; 0,6 м для проходов к бакам, чанам и резервуарам для их обслуживания и ремонта. Минимальная ширина проходов, предназначенных для транспортирования крупных сменных узлов и деталей во время ремонта оборудования, должна на 1,2 м превышать их максимальный размер.
Передвижение работающих по фабрике допускается только по предусмотренным для этого проходам, лестницам и площадкам. Перелезать через трубы, желоба, барьеры и прочие устройства не разрешается.
Все площадки для обслуживания оборудования, переходные мостики и лестницы должны быть прочными, устойчивыми и снабжены перилами высотой не менее 1 м с перекладиной и сплошной обшивкой понизу перила на высоту 0,14 м.
Рабочие площадки, расположенные на высоте более 0,3 м, должны быть ограждены перилами и снабжены лестницами.
Площадки для обслуживания оборудования и ступени лестниц должны быть выполнены таким образом, чтобы на них не задерживались влага и грязь.
Угол наклона лестниц к рабочим площадкам и механизмам зависит от условий эксплуатации (при постоянной эксплуатации – не более 45о, при посещении 1 - 2 раза в смену – не более 60о, а в зумпфах и колодцах – до 75о).
Во всех случаях ширина лестниц должна быть не менее 0,6 м, высота ступеней – не более 0,3 м, ширина ступеней – не менее 0,25 м. Металлические ступеньки лестниц и площадки должны выполняться из рифленого металла.
Как правило, предусматривают кнопочное управление оборудованием. Кнопки располагают на высоте 1 – 1,5 м над уровнем пола рабочего места при обслуживании стоя и 0,6 – 1,2 м – при обслуживании сидя. Пульты и панели управления располагают в местах с хорошим обзором обслуживаемого агрегата и прилегающих е нему участков. Для оповещения о пуске, остановке и нарушениях режима работы обслуживаемых агрегатов используют световую и звуковую сигнализацию.
Все движущиеся части машин и механизмов, ременные и другие передачи должны быть ограждены, чтобы исключить доступ к ним во время работы. Ограждение должно быть надежно закреплено. Вращающие части (валы, муфты, шкивы, барабаны и т. п.) должны иметь сплошные или сетчатые ограждения с ячейками размером не более 25 на 25 мм. Для барабанов конвейеров допускается сетчатое ограждение с размером ячейки не более 40 на 40 мм.
Перед пуском в работу оборудования, находящегося вне зоны видимости, должен быть подан звуковой предупредительный сигнал продолжительностью не менее 10 с, а затем после паузы (не менее 30 с) – второй сигнал продолжительностью 30 с.
Кроме того, о пуске такого оборудования оповещают по громкоговорящей связи с указанием его наименования и технологической нумерации.
7.4. Мероприятия по снижению запыленности и загазованности на
обогатительной фабрике
Способы борьбы с пылеобразованием на обогатительных фабриках и связанные с ними мероприятия можно подразделить на следующие группы: создание условий переработки и обогащения, исключающих большое пылеобразование (минимальный по длине транспорт, минимум перегрузок, устранение переизмельчения при грохочении, дроблении, обогащении, небольшая скорость воздуха и т.д.); подавление пыли в местах ее образования, исключающее поднятие её в воздух (орошение, воздействие связывающими пыль веществами); устранение выбросов в рабочее пространство из укрытий пылевоздушный смеси; тщательный отсос образовавшейся в укрытиях пылевоздушной смеси.
В технологических процессах устранение большого пылеобразования достигается применением малопылящего оборудования. Так, следует применять дробилки, материал в которых дробится раздавливанием и раскалыванием, а не ударом и истиранием.
При выборе грохотов следует учитывать, что вибрационные и резонансные грохоты энергично встряхивают материал и сильно пылят, а валковые пылят меньше, чем барабанные, и т.д.
Сокращение мест перегрузок, уменьшение высоты перегрузок и скорости движения материала в местах перегрузок уменьшают пылеобразование. При загрузке бункеров следует устраивать спиральные спускные желоба, при выгрузке из бункеров применять малопылящие питатели. Создание в бункерах небольшого вакуума устраняет выход из них пылевоздушной смеси. Непрерывная работа оборудования фабрики и замена трансмиссией редукторной передачей уменьшают образование промышленной пыли. Увлажнение материала сильно влияет на пылеобразование. Так, увеличение влажности порошка шамота от 0,02 до 4 % уменьшает пылеобразование в 58 раз; увеличение влажности сухих кварцитов на 1 – 2 % подавляет пылеобразование в 9 – 10 %.
При увлажнении материалов следует учитывать их смачиваемость. К хорошо смачивающимся водой материалам следует отнести кварц, полевой шпат, магнетит, слюду и другие окисленные ископаемые; к слабо смачивающимся веществам относятся тальк, графит, пирит, антрацит и целый ряд других материалов.
Главные мероприятия по борьбе с пылеобразованием и загрязнением рабочих пространств – хорошая аспирация обогатительных фабрик, хорошая изоляция пылящих мест от рабочих, постоянная чистота фабрик, правильный подвод свежего воздуха на рабочие места. А также немаловажную роль играет работа самих вентиляционных установок, т.е. во время работы технологического оборудования все основные приточно-вытяжные вентиляционные установки фабрики должны работать непрерывно.
На рабочих местах необходимо систематически контролировать состояние атмосферы и принимать меры по устранению её запыленности.
7.5. Пожарная безопасность
Ответственность за противопожарное состояние предприятия и цехов возложена на руководителей этих предприятий и цехов.
Для каждого производственного помещения разрабатываются противопожарные инструкции, которые должны быть внимательно изучены рабочими и служащими, и строго выполняться в процессе производства.
Территория предприятия и помещения цехов должны содержаться в чистоте, а проезды и подъезды к зданиям, сооружениям и источникам водоснабжения – в исправном состоянии.
Должны быть определено число и места хранения пожароопасных жидкостей и веществ, установлен строгий порядок сбора промасленных обтирочных материалов в металлические ящики с крышами и их своевременное удаление из цеха.
Проходы, выходы, коридоры, лестницы должны содержаться в исправном состоянии и ничем не загромождаться.
Спецодежда должна храниться в специально предназначенных для этих целей помещениях. Оставление после работы спецодежды у рабочих мест не допускается.
Все цехи, мастерские, склады и другие помещения должны быть снабжены первичными средствами пожаротушения, установленными на специальных щитах, и обеспечен свободный доступ к ним.
Цехи, склады, мастерские должны быть обеспечены материальными наглядной противопожарной агитации с учетом особенностей технологического процесса.
7.7. Защита от шума и вибрации
На обогатительной фабрике основным из вредных влияний является шум механического происхождения, возникающий вследствие вибрации поверхностей машин и оборудования, а также одиночных или периодических ударов в сочленениях деталей, сборочных единиц или конструкций в целом, распространяющийся в воздушной среде от источника возникновения до места наблюдения.
Целью установления допускаемых значений шумовых характеристик машин является:
- обеспечение условий труда, при которых шум, воздействующий на работающих, не должен превышать предельно допускаемых уровней;
- получение объективных данных о шумовых характеристиках машин, позволяющих проектным организациям рассчитывать ожидаемый шумовой режим в производственных помещениях;
- оценка конструктивного совершенства и качества изготовления машин точки зрения безопасности труда по их шумовым характеристикам. Шум на фабрике характеризуется как постоянный широкополосный с непрерывным спектром шириной более одной октавы.
Средства и методы защиты от шума по отношению к защищаемому объекту подразделяются на:
- средства и методы коллективной защиты;
- средства индивидуальной защиты.
Главным является подавление шума в источнике, а затем необходимы меры, предупреждающие его распространение. Уменьшение шума от соударения металлических частей машин достигается заменой металлических деталей неметаллическими, с этой целью используют искусственную техническую кожу, пластические массы и другие материалы. Для ослабления шума агрегатов в источнике применяют ряд других мероприятий:
- замену ударных действий безударными;
- замену возвратно-поступательных движений деталей агрегатов вращательными движениями;
- уменьшение ударов в сочленениях деталей и устранения неправильного сочленения деталей (перекосов);
- смазка соударяющихся деталей вязкими жидкостями и заключение в жидкостные, масляные и другие ванны вибрирующих и создающих шум деталей;
- замена подшипников качения подшипниками скольжения;
- ограничение скорости обтекания деталей агрегата воздушными и газовыми струями;
- заключение в изолирующие кожухи шумящие узлы агрегатов
Качественные и количественные критерии и показатели неблагоприятного воздействия вибрации на человека в процессе труда устанавливаются санитарными нормами, правилами и другими нормативными документами Минздрава. Воздействие вибрации на человека классифицируется:
- по способу передачи вибрации на человека;
- по направлению действия вибрации;
- по временной характеристики вибрации.
В качестве факторов, влияющих на степень и характер неблагоприятного воздействия вибрации, должны учитываться:
- риски (вероятности) проявления различных патологий вплоть до профессиональной вибрационной болезни;
- показатели физической нагрузки и нервно-эмоционального напряжения;
- влияние сопутствующих факторов, усугубляющих воздействие вибрации (шум, влажность);
- длительность и прерывистость воздействия вибрации;
- длительность рабочей смены.
Показатели вибрационной нагрузки на оператора формируются из следующих параметров:
- виброскорость (уровень виброскорости)
- диапазон частот;
- время воздействия вибрации.
Оценка вибрационной безопасности труда должна производиться на рабочих местах технологической операции. Основным способом обеспечения вибробезопасности является применение вибробезопасных машин.
Вибробезопасность труда на предприятиях должна обеспечиваться:
- соблюдением правил и условий эксплуатации машин и ведения технологических процессов, использованием машин только в соответствии с их назначениями;
- поддержанием технического состояние машин, параметров технологических процессов, своевременного проведения планового и предупредительного ремонта машин;
- совершенствованием режимов работы машин и элементов производственной среды, исключением контакта работающих с вибрирующими поверхностями за пределами рабочего места или зоны, введением ограждений, предупреждающих знаков, окраски, сигнализации, блокировки;
- улучшением условий труда;
- применением средств индивидуальной защиты от вибрации;
- введением и соблюдением режимов труда и отдыха, в наибольшей мере снижающих неблагоприятной воздействие вибрации на человека;
- санитарно-профилактическими и оздоровительными мероприятиями,предусмотренными рекомендациями Минздрава.
7.9. Охрана окружающей среды
К основу мероприятию по охране окружающей среды на фабриках алмазной промышленности России является организации системы бессточных водохранилищ для складирования хвостов. Такие системы характеризуются практически полным водооборотом, отсуствием сброса в открытые водостоки, а также отсутствием фильтрационных потерь благодаря устройству ограждающих дамб мерзлотного типа. Производственные стоки алмазоперерабатывающих фабрик в целом пригодны для полного оборотного водоснабжения при некоторых мероприятиях по кондиционированию воды и регулированию реагентного режима в процессах пенной сепарации.
Кондиционирование заключается в осветлении и умягчении оборотной воды, подаваемой на пенную сепарацию, и доочистке концентрата от солей химическим методом с помощью щелочных осадителей для процесса электрохимической сепарации. Установки по кондиционированию воды размещаются в помещениях фабрик и являются составной частью технологии соответствующих процессов обогащения.
Бессточная система оборотного водоснабжения организуется по схеме: обогатительная фабрика – хвостохранилище – обогатительная фабрика. При этом в водном балансе хвостохранилища образуется избыток в объеме воды из-за необходимости использования свежей воды на доводочных операциях обогащения. Избыток аккумулируется в хвостохранилище в течение всего периода эксплуатации. Накапливание излишков воды в хвостохранилище предпочтительнее по сравнению со сбросом и предварительной их очистки не только по условиям охраны окружающей среды, но и в экономическом отношении.
В зимний период уровень воды в хвостохранилище поддерживается постоянным за счет подледного складирования хвостов. Вода, вытесняемая хвостами, сбрасывается в пруд-накопитель и в насосную станцию оборотной воды.
Летом вода из накопителя поступает на фабрику через станцию оборотной воды или обратно в хвостохранилище, освобождая тем самым объем для зимнего периода.
За летний период дамба хвостохранилища должна наращиваться намывов до отметок, обеспечивающих прием перекачиваемой из накопителя воды, складирования хвостов и естественного стока с поверхности, включая половодье следующего года.
Для повышения эффективности осаждения шламов применяют коагуляционный метод. Этот метод заключается в том, что в осветляемую воду добавляют полиакриламид в целях ускорения осаждения взвесей. Полиакриламид выступает в роли ситетического органического флокулянта.
Очистка сточных вод методом электрокоагуляции основана на них электролизе с использованием металлических анодов, подвергающихся элетролитическому растворению. Вследствие растворения анодов вода обогащается соответствующими ионами, образующими затем в нейтральной и слабощелочной среде гидроксид железа (II), который под воздействием растворенного в воде кислорода переходит в гидроксид железа (III). В результате осуществляется процесс коагуляции, аналогичный обработке воды соответствующими солями железа. Однако в отличие от применения солевых коагулянтов при электрокоагуляции вода не загрязняется сульфатами или хлоритами, содержание которых в очищенной воде лимитируется как при сбросе ее в открытые водоемы, так и при повторном использовании в системах промышленного водоснабжения.
Электрокоагуляция применяется главным образом для удаления из сточных вод нерастворенных тонкодисперсных примесей, образующих в воде различные коллоидные системы. Значительно реже этот метод применяется для удаления из воды частично растворенных примесей.
Основными преимуществами электрокоагуляционного метода по сравнению с реагентными являются компактность установки, относительная простота ее эксплуатации и сокращение реагентного хозяйства. Применение электрокоагуляции предпочтительно при обработке сточных вод, расход которых не превышает 50-80 м3/ч, в условиях нехватки производственных площадей, а также на предприятиях, расположенных в отдельных и бездорожных районов.
Для очистки промышленных сильнозагрязненных вод, содержащих большое количество поверхностно-активных т твердых частиц, целесообразно сочетать флотационные, гравитационные, механические и другие методы. При использовании флокулянтов необходимо обеспечить условия, предотвращающие декструкцию молекул флокулянта и разрушение образующих с их помощью флоккул и аэрофлокул.
Для очистки промышленных вод на фабрике применяется электрохимический метод водоподготовки, основанный на принципах электролиза водных систем. Изменение характеристик воды происходит в электролизерах бездиафрагменного типа. Аппарат представляет собой замкнутый корпус, в объем которого подается исходная вода. Внутри корпуса установлен блок электродов, через которые пропускается постоянный ток.
К природоохранным мероприятиям следует так же отнести использование нетоксичных реагентов в соответствующих операциях обогащения. До недавнего времени при доводке алмазных концентратов применялся метод разделения в тяжелых суспензиях, где в качестве суспензии использовалась высокотоксичная жидкость Клеричи, имеющая в своем составе таллий.
В настоящее время процесс разделения алмазосодержащих концентратов в тяжелых суспензиях заменен другими процессами, в частности, рентгенолюминесцентной сепарацией.
ЗАКЛЮЧЕНИЕ
В дипломном проекте осуществлен выбор и расчет технологической схемы обогащения руды месторождения "Интернациональная". Схема выбиралась на основании анализа вещественного состава и технологических свойств минералов, входящих в состав исходного сырья. Были определены основные технологические показатели обогатимости минералов, что позволило определить необходимые данные для осуществления последующих этапов проектирования. Используя стандартную методику, было выбрано оборудование и рассчитано его количество. Состав основных фондов позволил определить затраты капитальные и эксплуатационные посредством чего была определена себестоимость переработки одной тонны рудного сырья и рассчитана товарная продукция.
В приложении представлена графическая часть дипломного проекта
на ___ листах.
Литература
А.Е. Троп, В.З. Козин, В.М. Аршинский «Автоматизация обогатительных фабрик», издательство «Недра» Москва 1970 год, 318 с;
А.К. Разумов «Проектирование обогатительных фабрик», издательство «Недра», Москва 1970 год, 591 с;
А.Л. Саградян, Н.А. Суворовская, Б.Г. Крангачев «Контроль технологического процесса флотационных фабрик», издательство «Недра», 1983 год, 407 с;
А.И. Берлинский «Разделение минералов», Москва, издательство «Недра», 227 с;
Б.Д. Кошарский, А.Я. Ситковский «Автоматизация управления обогатительными фабриками» Москва «Недра» 1977 год, 526 с;
В.А. Глембоцкий, В.И. Классен «Флотация», издательство «Недра», Москва 1973 год, 379 с;
В.А. Глембоцкий, В.И. Классен «Флотационные методы обогащения», Москва «Недра» 1981 год, 303 с;
В.И. Ревнивцев, Е.И. Азбель, Е.Г. Баранов, В.М. Изоитко, Е.И. Крапивский, М.И. Кротков, Е.П. Леман, А.С. Петров «Подготовка минерального сырья к обогащению и переработке», издательство «Недра» 1987 год, 304 с;
В.Я. Бадеников, С.Б. Леонов «Некоторые вопросы интенсификации флотации», издательство Иркутского университе, 1986 г, 190 с;
Е.К. Лазаренко «Курс минералогии», издательство «Высшая школа», Москва 1971 год, 607 с;
К.А. Разумов «Проектирование обогатительных фабрик», Государственное научно-техническое издательство литературы по чёрной и цветной металлургии, Москва 1952 год., 600 с;
К.А. Разумов «Проектирование обогатительных фабрик», издательство «Недра», Москва 1965 год, 504 с;
Л.А. Васильев, З.П. Белых «Алмазы, их свойства и применение», Москва «Недра» 1983 год, 99 с;
О.С. Богданов «Теория и технология флотации руд», Москва «Недра» 1980 год, 430 с;
С.И. Черных «Создание флотационных машин пневматического типа и опыт их применения на обогатительных фабриках», Москва «ЦНИИцветмет экономики и информации» 1995 год, 299 с;
Ф.А. Фишман, В.И. Зеленов «Практика обогащения руд цветных и редких метеллов» Т. 5, 253 с., издательство «Недра», Москва 1967 год;
Ю.Б. Рубинштейн, В.И. Мелик-Гайказян, Н.В. Матвеенко, С.Б. Леонов «Пенная сепарация и колонная флотация», издательство «Недра», 1989 год, 303 с;
«Методика проведения экспериментов на пенном сепараторе ПС-0,2», г. Мирный, Якутнипроалмаз, 1980 год;
А.Д. Кириллин, О.А. Кириллин, Г.А. Кириллин «Мировой алмазный рынок», Москва-1999 год, 397 с;
В.М. Авдохин «Основы переработки и обогащения полезных ископаемых», Москва-1996 год, 117 с;
А.Д. Харькив, Н.Н. Зинчук, А.И. Крючков «Коренные месторождения алмазов мира», Москва, Недра 1998 год, 555 с;
А.А. Абрамов «Переработка, обогащение и комплексное использование твердых полезных ископаемых», Москва, издательство МГГУ, 2001 год.
Специальная часть
5.1. Общие сведения
Флотационное обогащение — один из обогатительных процессов разделения минералов или отделения одной группы минералов от другой для дальнейшего экономически целесообразного их применения в народном хозяйстве. Такое разделение основано на использовании различия природных или искусственно созданных свойств минералов.
Способы флотации. Флотация как процесс обогащения позволяет отделить частицы одних минералов от других за счет селективного прилипания их к поверхности раздела двух фаз — жидкой и газообразной.
В промышленности широко применяется пенная флотация — процесс, основанный на прикреплении менее гидрофильных частиц к пузырькам воздуха, пропускаемого снизу через смесь минеральных частиц с водой (пульпу), и выносе этих частиц на поверхность пульпы, где образуется пена. Более гидрофильные частицы при этом остаются взвешенными в пульпе.
Разновидность пенной флотации — пенная сепарация, при которой пульпа подается на поверхность пены. Струя пульпы частично пробивает в месте подачи слой пены, однако воздух, проходящий снизу вверх, селективно удерживает и уносит в пену менее гидрофильные частицы, а более гидрофильные, не удерживаясь в пенном и подпенном слоях, падают вниз.
Находит применение и пленочная флотация, при которой менее гидрофильные частицы, попадая на поверхность потока пульпы, остаются на ней, образуя пленку, а более гидрофильные тонут.
В настоящее время редко используются процессы масляной флотации и флотации твердой стенкой. В первом случае менее гидрофильные частицы прилипают к каплям масла и всплывают вверх, а более гидрофильные остаются взвешенными в пульпе, во втором — менее гидрофильные частицы прилипают к гидрофобной твердой движущейся поверхности, которая выносит их из пульпы.
Флотационный процесс используется также для извлечения тонкодисперсных гидрофобных осадков, находящихся в растворе или образующихся при взаимодействии ионов раствора с добавляемыми реагентами (ионная флотация).
Пенная флотация осуществляется во флотационных машинах, в которых пульпа перемешивается с необходимыми реагентами, причем через пульпу пропускаются воздушные пузырьки. С помощью пузырьков и происходит разделение минеральных частиц.
Флотационные машины бывают различных типов в зависимости от способов перемешивания пульпы, засасывания и диспергирования воздуха.
Назначение флотационных реагентов. Большинство минералов в естественном виде хорошо смачивается водой и не обладает способностью к флотации. Вследствие этого главными реагентами, обеспечивающими флотацию минералов, являются реагенты, гидрофовизирующие поверхность минерала. Основное назначение этих реагентов — сорбироваться на поверхности минеральных частиц и снижать их смачиваемость. Эти реагенты называются собирателями. Однако, как правило, действие собирателей недостаточно селективно. Поэтому применяют реагенты, которые регулируют действие собирателей, усиливая его или ослабляя. Реагенты, усиливающие действие собирателей, называются активаторами, а ослабляющие это действие — подавителями (депрессорами) .
Естественная флотируемость минералов и их гидратация. При разрушении твердого тела происходит разрыв связей между молекулами, атомами или ионами и на его поверхности появляются ненасыщенные связи.
Энергия взаимодействия между твердой поверхностью и окружающими молекулами жидкости определяется характером связей, обнажающихся при раскалывании твердого тела, что, в свою очередь, зависит от его структуры. Поэтому различия в гидрофильности твердых тел обусловливаются характером этих связей или особенностями структуры твердого тела, как было показано Г.С. Стрельциным.
Естественная флотируемость свойственна многим органическим соединениям (например, углеводороды) и лишь очень немногим неорганическим соединениям (сера, йод, графит, молибденит, тальк и борная кислота).
Различный характер связей, обнажающихся при раскалывании минералов, обусловливает резкие различия в их гидрофильности и флотационных свойствах. Тальк и слюда имеют сходные кристаллические структуры. Эти минералы являются слоистыми силикатами, кристаллы которых состоят из слоев кремнекислородных тетраэдров; но тальк обладает естественной флотируемостью, так как слои тетраэдров у этого минерала соединены слабыми молекулярными связями, а слюда гидрофильна, так как у нее связь между слоями кремнекислородных тетраэдров осуществляется за счет ковалентных и ионных сил.
5.2 Пневматические флотационные машины
В пневматических флотационных машинах пульпа перемешивается подводимым воздухом; съем пены — двусторонний и часто осуществляется самотеком.
Флотационная машина с неподвижным пористым днищем "Келлоу", машина "Мак-Интош" с одним или двумя вращающимися у дна роторами, покрытыми пористой тканью или перфорированной резиной, мелкие аэролифтные машины "Форрестер" и "Саусвестерн" широко применялись в 30—40-х годах. В настоящее время эти машины редко устанавливаются на обогатительных фабриках. К их недостаткам относятся забивание пор (особенно при использовании извести) в машинах "Келлоу" и "Мак-Интош", забивание воздухоподводящих трубок песками при отключении воздуха в мелких аэролифтных машинах, трудности при переработке грубозернистого материала, чувствительность к колебаниям плотности пульпы и гранулометрического состава руды.
Глубокая аэролифтная машина АФМ 2,5 разработана в СССР и отличается от других конструкцией глубоких аэролифтных машин двусторонним щелевым подводом воздуха. Щелевые аэраторы представляют собой пустотелые металлические коробки, заканчивающиеся сбоку щелевидным обратным клапаном, образованным стенкой коробки и резиновой накладкой и предохраняющим аэратор от забивания. Аэраторы подводят воздух к центральному отсеку (аэролифтной камере) равномерно по всей длине машины. В результате плотность пульпы в центральном отсеке по сравнению с боковыми отсеками снижается, пульпа из боковых отсеков поступает в центральный отсек, смешивается с воздухом и выбрасывается вверх.
Отбойник над центральным отсеком направляет пульпу вниз, и она вместе с мелкими и минерализованными пузырьками под вертикальными перегородками поступает в боковые отсеки. При этом транспортный воздух выходит через отверстия в системе направляющих щитов. Минерализованные пузырьки поднимаются вверх и образуют на поверхности боковых отсеков пену, удаляемую самотеком.
Аэролифт машины АФМ 2,5 имеет высокую производительность и обеспечивает интенсивное перемешивание и аэрацию пульпы. Коэффициент использования воздуха по сравнению с мелкими аэролифт-ными машинами увеличен с 5—10 до 25 %.
Машина компонуется из отдельных секций длиной 3 м. Глубина ванны 2 м, ширина 2,5 м. Расход воздуха составляет 5-7 м3/мин на 1 м машины при избыточном давлении 25—30 кПА. Выход пенного продукта регулируется накладными планками. Пульпа поступает в машину через приемный карман и разгружается через хвостовой карман, снабженный шибером для регулирования уровня пульпы в ванне.
Промышленные испытания машины АФМ 2,5 и машины "Саусвес-терн" на старой Кафанской фабрике, перерабатывающей медно-пирит-ную руду, показали экономические преимущества машины АФМ 2,5, на основании чего машина АФМ 2,5 была установлена на новой Кафанской фабрике.
Колонная флотационная машина выпускается фирмой "Колэм Флотейшн" (Канада). Она состоит из трех частей: верхней, центральной и нижней. Обработанная реагентами пульпа поступает в центральную часть колонны и движется навстречу воздушным пузырькам, поднимающимся снизу из специального диспергатора воздуха.
В качестве диспергатора воздуха, расположенного в нижней части колонны, используются рукава из перфорированной резины или ткани. Срок службы трубок составляет не менее 0,5 г. Расход воздуха 1,35 м3/мин на 1 м2 сечения машины. В верхнюю часть колонны подается чистая вода. Поток воды отмывает механически увлеченные при движении пузырька частицы и способствует получению высококачественных концентратов. Это — важное технологическое достоинство колонной машины. Пульпа разгружается через трубу, снабженную клапаном, с помощью которого автоматически регулируется уровень пульпы в машине.
На фабрике 'Таспе" (Канада) в перечистках молибденового концентрата установлены три колонные машины сечением 1,8 х 1,8, 0,9 х х 0,9, 0,45 х 0,45 м и глубиной 12 м. Три перечистки в колоннах заменили 13 операций, которые проводились в машинах "Денвер Д-Р". Сокращение числа операций достигнуто благодаря лучшему разделению минералов в колонных машинах, при этом извлечение молибдена возросло на 11 %.
Колонные машины установлены также на канадских фабриках "Гибралтар", "Лорнекс", "Хаймонт", "Айленд Коппер" в молибденовых перечистках цикла медно-молибденового разделения, на фабрике "Гибралтар", кроме того, — в перечистках медно-молибденового концентрата, на фабрике "Полярис" — в перечистках свинцового и цинкового концентратов.
В СССР ИОТТ, Гинцветметом и Госгорхимпроектом разработаны оригинальные конструкции колонных машин. Колонные машины, сконструированные институтом ИОТТ, успешно применяются на фабриках в перечистках сурьмяного концентрата и для доизвлечения цинка из хвостов разделения свинцово-цинкового концентрата. Конструкции колонных машин предложены в США, Великобритании, Польше, Индии и других странах.
Флотационные машины чанового типа разработаны в СССР. Камера машины имеет верхнюю цилиндрическую и нижнюю коническую части. В камере расположены два аэратора — основной и вспомогательный. Основной аэратор представляет собой металлический каркас с закрепленными на нем перфорированными резиновыми трубками. Вспомогательный аэратор имеет коническую форму и состоит из металлического каркаса с закрепленными на нем резиновыми кольцами. Он предназначен для пуска машины с питанием за счет подачи в него сжатого воздуха.
Пульпа подается в машину в верхней части камеры через центральную трубу и по периферии и движется навстречу пузырькам, образованным при пропускании воздуха через основной аэратор. Пенный продукт разгружается самотеком в кольцевой желоб, камерный продукт — через карман с шибером.
Технические характеристики пневматических машин чанового типа приведены в таблице
Параметр | ФП 10 | ФП40 | ФП 80 | ФП 100 |
Диаметр, м | 2 | 3,4 | 3,4 | 3,4 |
Глубина, м | 5,2 | 5,2 | 11 | 13 |
Вместимость, м3 | 10 | 40 | 80 | 100 |
Производительность по потоку | 3 | 8 | 8 | 8 |
пульпы, м3/мин | ||||
Максимальный расход воздуха, | 7,5 | 15 | 30 | 40 |
м3/мин | ||||
Избыточное давление воздуха | 0,15 | 0,15 | 0,16 | 0,18 |
на входе в аэратор, мПА | ||||
Мощность, затрачиваемая на | 19 | 40,5 | 81 | 108 |
подачу максимального расхода | ||||
воздуха, кВт |
Новая пневматическая флотационная машина создана в ФРГ. Первая особенность машины состоит в том, что диспергирование воздуха и минерализация пузырьков предварительно подготовленными к флотации частицами осуществляются в специальном аэра-ционном реакторе, а отделение минерализованных пузырьков от пульпы, образование пены и удаление концентрата и хвостов происходят во флотационной камере. Другая особенность машины заключается в условиях диспергирования воздуха и минерализации пузырьков в аэра-ционном реакторе.
Воздух подается через пористую среду поперек направлению движения пульпы, при этом ширина слоя пульпы, в котором эффективно минерализуются пузырьки, не превышает нескольких сантиметров. Размер генерируемых в таком слое пузырьков составляет менее 0,5 мм. Минерализованные пузырьки уносятся пульпой во флотокамеру.
Аэратор в виде трубок изготовлен из полиэтилена низкого давления. Трубки имеют диаметр пор 15 мкм и порозность 40 %. Воздух подводится в трубки с двух сторон. Скорость движения пульпы составляет 9,5 м/с.
Поток пульпы, поступающий на флотацию, делится на части, каждая из которых обрабатывается в одном аэрационном реакторе и раздельно вводится во флотационную машину. Камера представляет собой конусообразную емкость с цилиндрической верхней частью. Пульпа поступает в камеру из аэрационных реакторов горизонтально и почти тангенциально или снизу. Минерализованные пузырьки всплывают вверх, образуя пену, которая разгружается в центральной части камеры, а несфлотированные частицы разгружаются снизу.
Пневматическая флотационная машина испытана в полупромышленных условиях на угле, железной, магнезитовой, апатитовой рудах и тонких шламах свинцово-цинковой руды. В промышленной эксплуатации находятся камера производительностью 1,7 м3/мин в которой флотируется апатитовая руда, и камеры вместимостью 27 и 40 м3 производительностью соответственно 8,3 и 16,7 м3/мин, обрабатывающие воды после промывки угля с содержанием твердого 30—70 г/л.
Машина характеризуется высокой скоростью и селективностью флотации, в том числе труднофлотируемых частиц размером +200 и — 10 мкм, низкими энергетическими затратами (в 3—4 раза меньшими, чем в механических флотационных машинах). Расход воздуха составляет 0,2—1,3 м3/мин на 1 м3 потока пульпы.
Конечные результаты достигаются в машине при обогащении обычно в одну стадию, лишь при обогащении сложных руд требуются две операции флотации. Срок службы аэраторов не указывается. Отмечается, что наряду с аэраторами из пористых материалов в машине применяются также щелевые аэраторы.
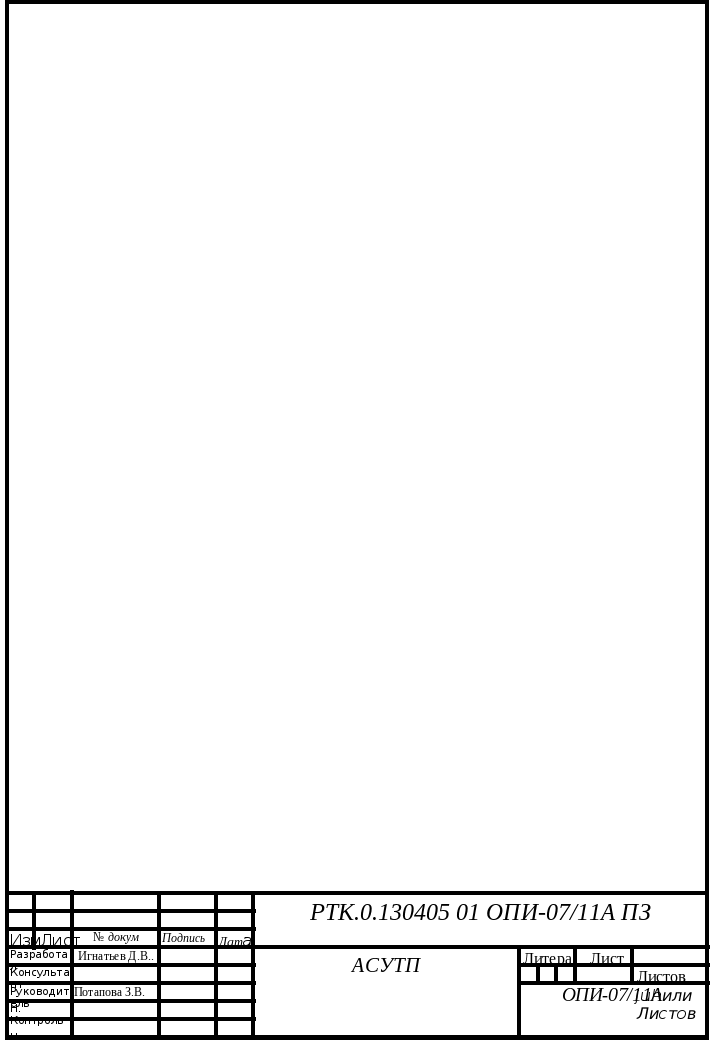
Для эффективного ведения технологического процесса на обогатительной фабрике предусматривается Автоматизированная система управления технологическими процессами (АСУТП).
Технологические процессы контролируются измерением вручную или автоматически различных технологических параметров. Непрерывные измерения служат основой для автоматического регулирования процессов обработки поденного ископаемого на обогатительной фабрике.
Задачу автоматизации технологического процесса можно решить только при комплексном проектировании, когда все части проекта взаимно увязаны и каждый технологический узел выполнен так, что может хорошо работать без постоянного вмешательства рабочего.
На обогатительных фабриках применяются приборы автоматического контроля для измерения и определения следующих величин: количества обрабатываемого сырья; расхода используемых в качестве реагентов твердых веществ; содержания твердого в пульпе и плотности пульпы; дебита и суммарного расхода воды, растворов реагентов, пульпы и пара; уровня воды, растворов и пульпы в чанах; числа прошедших вагонеток с сырьем; скорости вращения и числа оборотов отдельных деталей машин (валов, шкивов и т, д.); концентрации водородных ионов в пульпе или в растворе; остаточной концентрации ионов некоторых реагентов в пульпе; температуры пульпы. воды, растворов, масла и газов; давления поды и пара; давлении разрежения воздуха и газов; времени работы, простоя и холостого хода механизмов; напряжения, потребляемой величины тока, мощности, расхода электроэнергии и т. д.
Для измеряемых величин можно в отдельных случаях предусматривать сигнализацию о соответствии их заранее заданным значениям.
4.2. Системы контроля и управления технологическими процессами
Система управления фабрикой включает в себя как традиционные средства получения и обмена информацией (проводная и беспроводная связь, промышленное телевидение), так и современные средства управляющей вычислительной техники.
Автоматизированная система охватывает как технологический, так и производственный уровни управления фабрикой.
4.2.1. Структура системы:
В структуре системы выделяются два уровня управления производственными процессами фабрики:
уровень технологического управления, на котором осуществляется оперативное управление технологическим процессом и оборудованием.
уровень административного управления, на котором осуществляется, преимущественно, организационно-экономическое управление фабрикой;
В структуре технологического уровня управления предусматривается рациональная децентрализации управляющих вычислительных комплексов с учетом сложившейся практики оперативного управления технологическим процессом на обогатительных фабриках. При таком подходе управляющие комплексы располагаются, преимущественно, в центрах управления (операторских пунктах) технологическим процессом. Распределение управляющих функций по управляющим комплексам в пределах одного центра управления предусматривается таким образом, чтобы обеспечить максимальную надёжность и автономность реализации низовых (базовых) функций, обеспечивающих работу технологического оборудования (пуск, стоп, блокировки, контроль и др.), т.е. для каждого сложного (с точки зрения управления) технологического агрегата предусматривается отдельный контроллер.
На технологическом уровне в системе предусматривается 7 центров оперативного управления технологическим процессом фабрики
центральный диспетчерский пункт
операторский пункт управления отделением рудоподготовки;
операторский пункт управления приёмом руды (на площадке бункеров);
операторский пункт управления отделением гравитационного обогащения (отсадка);
операторский пункт управления отделением рентгенолюминесцентной сепарации;
операторский пункт управления участком доводки;
операторский пункт управления хвостовым хозяйством и водоснабжением.
На административном уровне предусматриваются автоматизированные рабочие места (АРМы) для всего управляющего персонала фабрики.
Контроль и управление работой фабрики осуществляется с использованием средств управляющей вычислительной техники, средств связи и промышленного телевидения.
Управляющая вычислительная техника объединяется локальной вычислительной сетью (ЛВС) типа Enthernet. Для повышения надежности работы сети она разделяется на два сегмента - технологического и административного уровня.
4.3. Технологический уровень управления фабрикой
Общефабричные функции:
Стержнем автоматизированной системы является система централизованного контроля (СЦК), которая создаётся на основе SCADA- и предусматривает как стандартные для SCADA–пакетов функции, так и нестандартные (не входящие в пакет) функции контроля.
Стандартные функции:
опрос аналоговых, дискретных, числоимпульсных датчиков;
выдача управляющих воздействий на исполнительные механизмы;
первичная обработка данных (масштабирование, фильтрация, линеаризация);
представление данных оперативному персоналу на мониторах в текстовом и графическом видах;
сигнализация и протоколирование нарушений технологического процесса;
архивирование и просмотр трендов технологических параметров;
обмен информацией между узлами по локальной вычислительной сети.
Нестандартные функции:
дистанционное управление оборудованием (групповой пуск отдельных участков оборудования, сблокированный останов оборудования);
информационный обмен с внешними объектами ;
расчет неизменяемых технологических переменных (показателей);
учет наработки и простоев оборудования с указанием причин;
интегрирование и усреднение технологических параметров на регламентированных интервалах времени (час, смена, сутки, месяц);
расчет сводок (рапортов) о работе отдельных узлов, технологических смен и фабрики в целом на регламентированных интервалах времени (час, смена, сутки, месяц).
Работа всей фабрики во многом определяется работой узла рудоподготовки, а эффективная работа узла, в свою очередь, определяется ритмичной подачей руды на мельницы, поэтому на этом переделе предусматривается набольшее количество средств контроля и систем управления.
Узел приема исходной руды. На этом узле предусматривается:
- автоматизированная система загрузки приёмных бункеров. Система осуществляет распределение самосвалов по приёмным бункерам с учётом их загрузки, количества работающих мельниц, их состояния и степени загрузки с использованием путевых светофоров.
Отделение рудоподготовки.На узле рудоподготовки предусматриваются следующие системы автоматического управления:
система контроля работы мельниц (пуск, стоп, блокировки, контроль температуры подшипников, масла, давления масла, работы маслостанций и др.);
система управления загрузкой мельниц. Включает стабилизацию и максимизацию загрузки по активной мощности привода и заполнению барабана мельниц рудой; управление осуществляется изменением скорости пластинчатого питателя подачи исходной руды в мельницы;
система управления распределением циркуляционных нагрузок по мельницам. Осуществляет пропорциональное или заданное распределение циркуляционных нагрузок по мельницам изменением положения регулирующих задвижек пульподелителя. Контроль осуществляется по величине загрузки классификаторов.
система управления плотностью слива мельниц. Система осуществляет как стабилизацию плотности слива мельницы, так и оптимизацию плотности, обеспечивающую максимум производительности мельницы и высокую сохранность кристаллов. Регулирование осуществляется изменением расхода воды в мельницы.
система управления плотностью слива классификаторов. Регулирование осуществляется изменением расхода воды в классификаторы.
комплекс средств контроля режимов работы оборудования отделения, расхода рудных и водных потоков.
Отделение гравитационного обогащения. Установка тяжелосредного обогащения.Системы автоматического управления включаются в комплектную поставку установки.
Дополнительно к комплектной поставке предусматривается система контроля извлечения по магнитной фракции, а также комплекс средств контроля режимов работы оборудования отделения, расхода рудных, водных и воздушных потоков не вошедших в комплектную поставку.
Отделение рентгенолюминесцентной сепарации (РЛС).В отделении рентгенолюминесцентной сепарации предусматриваются следующие системы автоматического управления:
- система управления загрузкой сепараторов (поддержание уровня в бункерах изменением количества включенных сепараторов);
- системы индикаторного контроля сепараторов;
- система контроля основных параметров работы сепараторов;
- система стабилизации температуры воды на охлаждение рентгеновских трубок сепараторов;
комплекс средств контроля режимов работы оборудования отделения, расхода рудных, водных и воздушных потоков.
Участок доводки концентратов.На участке доводки концентратов предусматривается:
комплекс средств контроля режимов работы оборудования участка, расхода рудных, водных и воздушных потоков.
Узел хвостового хозяйства.На узле хвостового хозяйства предусматривается следующие системы автоматического управления:
система дистанционного управления пуском, переключением и остановом оборудования;
система автоматического регулирования водных и пульповых потоков;
система контроля состояния пульповодов и водоводов;
система контроля состояния плотин;
комплекс средств контроля режимов работы оборудования узла, расхода водных и пульповых потоков.
4.4 Технические и программные средства.
Общий подход к выбору технических средств.Предусматривается применение в минимальном объеме аналоговыхаппаратных средств контроля, управления, отображения информации (самопишущих приборов, аналоговых регуляторов, мнемосхем технологических процессов). Подавляющее большинство функций предусматривается осуществлять нацифровыхсистемах управления и представления информации на базе микропроцессорных управляющих вычислительных комплексов, имеющих более высокие технические и функциональные характеристики, меньшую стоимость.
Компьютеры.Для АРМов управленческого персонала предусматривается применение персональных компьютеров с операционной системой Windows98/2000, на базе процессора класса не ниже Pentium-III (частота 800 МГц, ОЗУ 128МВ, «Винчестер» 20GB, пишущий CD ROM, монитор 19”-21” дюйм ).
Датчики.Предусматривается применение датчиков с унифицированным выходным токовым сигналом4-20 мА, которые обеспечивают более высокую точность и надежность измерения параметров, чем стандарт 0-5мА и снижают стоимость одного измерительного канала. Предусматриваются датчики для измерения следующих видов технологических параметров: давление, температура, расход воды, расход воздуха, расход руды, уровень, электрическая мощность, электрический ток, плотность пульпы, положение исполнительных механизмов, специальные параметры.
Состав и количество датчиков должны обеспечивать максимально полный контроль материальных потоков и состояния технологического оборудования.
Везде, где это возможно, предусматривается бесконтактный способ измерения.
Для измерения уровней предусматриваются радарные или ультазвуковые датчики уровня.
Для измерения расхода воды предусматриваются электромагнитные расходомеры, обеспечивающие более высокую эксплуатационную надежность и точность измерения.
Подключение существующих датчиков и устройств с цифровым интерфейсом предусматривается по каналу RS –485 или по токовой петле.
Питание датчиков осуществляется от источников питания постоянного тока на нгапряжении 24В.
Использование сухих контактов датчиков типа БКС, индуктивных, ультразвуковых и т.д. предусматривается только в цепях 24В постоянного тока.
Для измерения давления ипользуются датчики Метран-49, которые предназначены для работы в системах автоматического контроля, регулирования, управления технологическими процессами и обеспечивают непрерывное преобразование значения измеряемого параметра в унифицированный токовый выходной сигнал дистанционной передачи. В датчиках давления "Метран-49" за счет реализации схемы трехмембранного приемника давления достигнуто сочетание высокой точности и стабильности измерений с высокой коррозионной стойкостью.
Для измерения уровня используются ультразвуковые датчики фирмы VEGA (Германия) т.к. они обеспечивают максимальную точность измерения бесконтактным способом. А также имеют:
специальное, коррозионностойкое исполнение.
Преобразователь звука из UP с мембраной из высококачественной стали (1.4571)
Интегрированный температурный датчик для корректировки времени распространения звука
Точность измерения ±10 мм.
Рабочая температура -40...80°C
Исполнительные механизмы.Для управления материальными потоками предусматривается использование регулирующих шаровых клапанов (вода), регулирующих дисковых затворов (воздух), регулирующих шиберных задвижек (руда, пульпа) с электрическимиисполнительными механизмами, обеспечивающих более высокую эксплуатационную надежность и экономичность по сравнению с пневматическими. Электрическиеисполнительные механизмы предусматриваются с аналоговым управляющим сигналом. Для регулирующих шиберных задвижек на руде и пульпе возможно применение исполнительных механизмов с пневматическим приводом.
Для управления скоростью пластинчатых питателей, насосов перекачки хвостов и оборотной воды предусматриваются регулируемые преобразователи частоты.
Промышленные компьютеры (контроллеры).На технологическом уровне управления предусматривается применение двух типов управляющих вычислительных комплексов (УВК) – индивидуальных и групповых.
Индивидуальные УВК предусматриваются в качестве замены аппаратных шкафов управления отдельными крупными и ответственными агрегатами (мельницы, отсадочные машины). Поскольку такие УВК осуществляют реализацию основных, базовых функций управления агрегатом (пуск, останов, контроль работы, поддержание основных режимов), то и требования к надёжности их функционирования наиболее высокие. Индивидуальные УВК создаются на основе промышленных микропроцессорных контроллеров (МПК).
Групповые УВК осуществляют управление группами агрегатов и реализуют более сложные (логические, связанные, оптимизирующие) функции управления, функции представления и хранения информации, функции связи и диагностики. Групповые УВК создаются на основе программируемых логических контроллеров или промышленных персональных компьютеров (ППК).
При выборе УВК целесообразно руководствоваться следующими соображениями: - УВК должен быть РС-совместимым (IBM PC-based), т.е. совместимым с персональными компьютерами. РС-совместимость обеспечивает единую для всей системы аппаратную и программную базу средств вычислительной техники, что, в свою очередь, облегчает их эксплуатацию. Кроме того, РС-совместимые УВК значительно дешевле любых других УВК, не уступая им в надёжности, и имеют широкую номенклатуру технических и программных средств;
УВК предпочтительней использовать с системной шиной типа PCI-ISA. УВК на базе этой системной шины, по сравнению с УВК на базе других системных шин (Compact PCI, VME, STD-32 и др.), на сегодняшний день имеют более широкий выбор средств ввода-вывода сигналов, достаточно надежны и значительно дешевле.
Электропитание.Электропитание всего оборудования системы (вычислительная техника, датчики, исполнительные механизмы и др.) должно быть организовано от отдельного фидера на котором не должно быть силовых энергопотребителей. Для всех устройств должны быть предусмотрены групповые или индивидуальные источники бесперебойного электропитания.
4.5 Автоматизация и контроль процесса флотации
Совершенствование технологических процессов обогащения и создание эффективных флотомашин невозможны без решения вопросов автоматизации, так как достижение наилучших технико – экономических показателей, закладываемых при разработке комплекса «технология – оборудование», невозможно лишь при условии, что данный комплекс оснащен средствами автоматического контроля и управления.
Основные направления автоматизации флотомашин имеют целый ряд специфических особенностей, определяемых дисперсным составом газовой фазы по высоте машины; раздельным регулированием расхода воздуха в диспергаторе, высоты пенного слоя и аэродинамических параметров в камере; положением загрузочного устройства на границе раздела пенного слоя и пульповоздушной среды; плотностью пульповоздушной среды; регулированием без остановки машины высоты камеры и энергетических воздействий (электрических, магнитных полей и др.) на обогащаемый материал, а также раздельной подачей реагентов в камеру с учетом степени флотируемости твердых частиц.
Система автоматического регулирования расхода флотационных машин, подаваемого в устройство для разгрузки камерного продукта, в зависимости от расхода воздуха происходит следующим образом. Исходная пульпа, обработанная реагентами, поступает в загрузочное устройство, которое равномерно распределяет пульпу по всему сечению камеры машины. Воздух, подаваемый в камеру через диспергаторы, образует пульповоздушную смесь. В слуае необходимости изменения степени аэрации пульпы регулируют расход подаваемого в диспергаторы воздуха, который фиксируется расходомером, и сигнал поступает на регулятор расхода воздуха, подаваемого в устройство разгрузки камерного продукта через диспергаторы. Регулятор поддерживает соотношение расхода воздуха, подаваемого в камеру машины и в устройство для разгрузки камерного продукта. Степень аэрации пульпы обуславливает изменение высоты пенного слоя и соответственно соотношений высот зон очистки и минерализации.
Система регулирования соотношения высот зон минерализации и очистки работает следующим образом. При перемещении диспергаторов приводным устройством изменяется соотношение высоты зон очистки и минерализации. Сигнал, пропорциональный перемещению диспергаторов по высоте, с датчика перемещения поступает на вход функционального преобразователя. Выходной сигнал с него подается на вход приводного устройства, которое по направляющим перемещает загрузочное устройство. Система автоматического регулирования обеспечивает заданное соотношение высот зоны минерализации и зоны очистки с учетом сигнала от регулятора.
При изменении гранулометрического состава исходной пульпы, плотности, степени аэрации и других параметров процесса возникает необходимость оперативного регулирования высоты камеры машины /15/.
Для управления процессом флотационного процесса алмазосодержащих кимберлитов разработаны и внедрены следующие вопросы:
- высокоточная система автоматического регулирования подачи пенообразователя в области низких его расходов, система автоматического регулирования уровня пульпы в камере флотомашины с регулированием расхода оборотной воды в зависимости от величины выгрузки камерного продукта, система и устройство для автоматического регулирования выгрузки хвостов;
- работа системы автоматического регулирования подачи пенообразователя основана на достаточно тесной зависимости между плотностью аэрированной пульпы и концентрацией пенообразователя в области низких его расходов при стабилизированном расходе воздуха на аэрацию пульпы и её жидкой фазы.
Разработка и внедрение указанных средств контроля и регулирования позволили достичь стабильно высоких показателей при флотационном обогащении алмазосодержащего сырья, а также повысить культуру производства и практически исключить ручной труд при управлении флотационным процессом.
В настоящее время процесс флотации кимберлитов достаточно изучен отечественными и зарубежными исследованиями и продолжает изучаться и интенсифицироваться в различных направлениях, основными из которых являются усовершенствование существующих технологических схем обогащения, изменение реагентных режимов и конструирование нового обогатительного оборудования. Построение систем автоматического управления флотационным оборудованием требует тщательного изучения сложной взаимосвязи факторов процесса с целью создания его математического описания и алгоритмов управления, правильного выбора критериев оценки эффективности работ флотации /1, 5, 3/.
К входными параметрами являются:
α– содержание кристаллов алмаза в руде; φ – флотируемость (окисленность, шламистость, фазовый состав руды и прочие характеристики); А или γ – производительность флотационной машины; λ – гранулометрический состав пульпы; δ – плотность пульпы; μi – концентрация реагентовв пульпе; h1 – уровень пульпы в камере; h2– уровень пены в камере.
К выходным параметрам относятся:
υ – содержание кристаллов алмаза в хвостах; β– содержание кристаллов алмаза в концентрате; γβ– выход концентрата; γν – выход хвостов.
В процессе роботы вышеперечисленные параметры изменяются и представляют собой в большинстве случаев стационарные случайные функции. Входные параметры могут изменяться весьма значительно. В связи с этим выходные параметры при ручном управлении изменяются также очень сильно.
Геологическая часть
1.1. Общие сведения
Рудник "Интернациональный" характеризуется весьма сложными горногеологическими условиями разработки. Наибольшую опасность представляет метегеро-ичерский водоносный горизонт, расположенный в интервале абсолютных отметок +40м/-130м. Подземные воды этого горизонта содержат растворенные в них газы: азот, метан, сероводород, углекислый газ. Учитывая это, при ведении горных работ должны приниматься меры, исключающие возможность обрушения и сдвижения как вмещающих пород, так и рудного тела. Рудник отнесен к опасным по выделению горючих газов и нефтебитумопроявлениям, поэтому одним из условий безопасного ведения работ является предварительная дегазация массива пород. Рудное тело месторождения – кимберлитовая овальной формы трубка вертикального падения. Руда характеризуется малой прочностью и средней степенью трещиноватости. Вмещающие породы представлены каменной солью, известняками, доломитами, ангидритами, переслаивающихся друг с другом. Породы не отличаются высокой прочностью (крепость по шкале Протодъяконова 3-8). Толща пород, в которой будут располагаться выработки проектируемых горизонтов, в основном, водоупорна. Максимальный водоприток в рудник не превысит 30 м3 /сутки.
Трубка “Интернациональная” расположена в бассейне р. Ирелях в верховьях ее правых притоков – ручьев Улахан-Юрях и Маччоба-Салаа в 16км юго-западнее г. Мирного – административного центра Мирнинского района Республики Саха (Якутия).
Территория района месторождения географически принадлежит восточной части Средне-Сибирской плоской возвышенности и представляет собой слаборасчлененную современной гидросетью равнину.
Абсолютные отметки рельефа колеблются от 310м на востоке, до 402м – на западе, непосредственно на месторождении – в пределах 390-400м. Относительные превышения вершин водоразделов над тальвегами долин не превышают 40-90м. Для района характерны пологие увалистые формы рельефа. Уклон склонов речных долин редко превышает 3-5о.
На участке месторождения гидросеть представлена временными водотоками в верховьях р. Юлигер и правыми притоками р. Ирелях – ручьями Улахан-Юрях и Маччоба-Салаа, лишенными постоянного водотока.
Климат района месторождения резко континентальный с продолжительной и суровой зимой (6-7месяцев) и коротким, часто жарким летом. Среднегодовая температура составляет –7.8.
Положительные среднесуточные температуры наблюдаются в среднем около 220 дней в году. Самым холодным месяцем является январь, со средней максимальной температурой 35, абсолютный минимум - 63С. Самый теплый месяц - июль со средне дневными температурами 28-30, абсолютный максимум +36С. Амплитуда абсолютных температур составляет 99, внутрисуточная амплитуда температур достигает 40С(1).
Месторождение расположено в зоне развития многолетнемерзлых пород, мощность которых составляет 300-330м. Мощность деятельного слоя изменяется от 0.2 до 0.5м на залесенных склонах северной экспозиции, до 1.5 – 5.0м - на открытых склонах южной экспозиции.
Среднегодовое количество осадков в районе г. Мирного (для бассейна р. Ирелях) составляет 250 - 290мм при колебаниях от 150 до 450мм (1). На период с июня по сентябрь приходится до 70% годового количества осадков.
Снежный покров устанавливается в первых числах октября и исчезает в начале мая, высота его в среднем составляет 35 - 50 см, для участков с ровной поверхностью - до 65 см.
В районе господствуют западные, юго-западные и южные ветры, наибольшие скорости ветра наблюдаются в осенний и весенний периоды, среднегодовая скорость ветра составляет 3.3 м/сек.
Месторождение расположено в средней подзоне редкостойной лиственичной тайги с мохово-лишайниковым покровом, подзолистыми и торфяно-болотными почвами. Растительность района скудная, строительный лес отсутствует, на отдельных участках выборочно возможна заготовка крепежного леса и дров.
Из полезных ископаемых в районе месторождения, помимо собственно алмазов в кимберлитах трубки, имеются месторождения глин, песков, гравийно-галечникового материала.
Кроме того, к полезным ископаемым района относятся соль и подземные воды.
Каменная соль (галит) приурочена к отложениям чарской и толбачанской свит. Запасы соли практически неограничены. По химическому анализу содержание хлорида натрия изменяется в пределах 97-99.2%. В качестве примесей в переменных количествах отмечается кальций, магний, железо и калий.
1.2. Геологическое строение
Коренное месторождение алмазов кимберлитовая трубка “Интернациональная” расположена в пределах Мало-Ботуобинского алмазоносного района, относящегося к Западно-Якутскому алмазоносному региону.
В платформенном комплексе выделяются три, разделенных перерывами и местами несогласиями, структурных яруса. Первый ярус включает архейские отложения (кристаллический фундамент), второй - венд - нижнекарбоновые и третий - верхний палеозой - нижний мезозой.
Характерной особенностью кимберлитов верхних горизонтов трубки «Интернациональная» (до глубины 370 м) является относительно высокое содержание примеси терригенного материала вмещающих пород. Последний представлен песчанистой, алевритистой и глинистыми фракциями и состоит из кварца, полевого шпата, турмалина, плагиоклаза, сфена. Глинистая составляющая имеет монтмориллонитовый состав. Глубже 370 м количество перечисленных минералов резко снижается, а, начиная с глубины более 500 м, они фактически исчезают.
Архейский кристаллический фундамент сложен глубоко метаморфизованными породами и вскрыт нефтепоисковыми скважинами на глубинах 1900-2100м.
Нижняя часть второго структурного яруса представлена вендским комплексом мощностью до 440м, сложенным песчанниками, доломитами с прослоями аргиллитов.
Отложения нижнего кембрия (1300-1400м) представлены сульфатно-галогенно-карбонатными породами и расчленяются на шесть свит (снизу вверх): пестроцветную, эльгянскую, толбачанская, олекминскую и чарскую. Кроме того, в состав этой толщи входит нижняя часть (30м) ичерской свиты нижнего-среднего кембрия. Чисто карбонатная формация в этой толще выделяется в олекминскую свиту.Отложения среднего кембрия (175м) разделены на ичерскую и метегерскую свиты и характеризуются кремнисто-карбонатно-доломитовым составом.
В результате среднепалеозойского тектоно-магматического этапа развития района были заложены гигантские зоны разломов, которые предопределили очертания основных структур: Вилюйско-Мархинской и Ахтарандинской. В пределах первой выделяются Западный, Центральный, Параллельный, Восточный и Аппаинский субмеридиональные разломы. По этой зоне на протяжении среднего палеозоя происходили наиболее интенсивные проявления магматизма.
В пределах разведанного интервала глубин преобладающим развитием пользуются карбонатные породы - доломиты и известняки с их многочисленными фациальными разностями. Взаимные переходы среди последних, как в плане, так и в разрезе могут происходить на весьма небольших расстояниях.
Мощности отдельных разновидностей пород колеблются в широких пределах от первых метров до 20-30м.
Соленасыщенность чарской свиты достигает 61%, а вскрытой части разреза толбачанской - 26%. Характерной особенностью карбонатных пород этих двух свит является их засоленность которая наиболее интенсивно развита в прослоях этих пород небольшой мощности.
Перекрываются кембрийские отложения осадочного чехла маломощной (до 10м) толщей современных преимущественно делювиальных и элювиальных образований. Представлены они крупнообломочными и супесчано-суглинистыми отложениями.
Ниже приводится более подробная характеристика вмещающих пород и кимберлитов в пределах интервала глубин проектируемых горизонтов месторождения трубки “Интернациональная”.
1.3. Рудное тело
Рудным телом месторождения является близцилиндрическая субвертикальная трубка овальной формы в горизонтальных сечениях, прорывающая вышеописанные породы и заполненная алмазосодержащими кимберлитовыми породами. Размеры трубки в плане по длинной и короткой осям в пределах отметок –200…-560м приведены в таблицах 1-2.
На поверхности характеризуемая трубка имеет форму неправильного овала, вытянутого на северо-запад (340°).
Трубка разведана до глубины 955 м. В среднепалеозойское и мезозойское время около 470 м верхней части диатремы было уничтожено в результате длительной эрозии. От раструба сохранилась нижняя 120-метровая его часть. Далее на глубину остатки раструба переходят в цилиндрический канал с почти вертикальными контактами. Угол падения контактов раструба на юго-востоке равен 60 — 700, на северо-западе, где сохранился своеобразный "козырек", — 40 — 60°.
До глубины 1000 м размеры трубки существенно не уменьшаются. Тело ее в целом склоняется в юго-восточном направлении. Трубка прорывает горизонтально залегающие терригенно-карбонатные породы нижнего ордовика и кембрия и перекрывается нижнеюрскими отложениями мощностью от 2,1 до 9,2 м. В раннетриасовое время трубка была перекрыта пластовым телом долеритов.
Под перекрывающими трубку терригенными отложениями нижней юры, по данным К.Г. Чумирина, установлена переотложенная кора выветривания кимберлитов мощностью 12 — 50 см. В составе минералов тяжелой фракции переотложенного материала содержание пиропа составляет 2,75 кг/т, хромшпинелида - 0,29 кг/т, пикроильменита — 0,21 кг/т; по сравнению с плотным кимберлитом верхних горизонтов трубки в переотложенных продуктах коры выветривания произошло относительное увеличение концентраций пикроильменита и хромшпинелида и уменьшение пиропа.
Кимберлиты представлены однообразными по составу породами, состоящими на 93% из кимберлитовых брекчий, с неравномерно распределенными среди них кимберлитами массивной текстуры (7%). Выделены три генетических фазы кимберлитов, различающихся по положению в трубке, содержанию минералов тяжелой фракции, химсоставу и алмазоносности. Преимущественным развитием пользуются кимберлиты 2 и 3 фаз внедрения (54.2 и 40.4%).
Кимберлиты интенсивно серпентинизированы и карбонатизированы. На контакте с галогеновыми породами они засолены, что проявляется в виде прожилков галита и боратов. В некоторых случаях объем прожилков достигает 17% от объема керна.
Контакты трубки с вмещающими породами четкие. Кимберлиты, слагающие рудное тело, характеризуются малой прочностью и имеют среднюю степень трещиноватости. По трещиноватости кимберлиты относятся к мелко- и среднеобломочным породам с размером отдельности до 300мм и от 300 до 600мм.
Р
ис. 1. Блок-диаграмма кимберлитовой трубки «Интернациональная».
1 – кимберлитовая брекчия; 2 – порфировый кимберлит; 3 – кимберлитовые дайки.
Вещественный состав
2.1. Общие сведения
Вещественный состав полезных ископаемых – это совокупность данных о содержании компонентов и примесей; минеральных формах проявления и характера срастания зерен важнейших элементов; их кристаллохимических и физических свойствах /20/.
Химический состав характеризует содержание основных и сопутствующих полезных компонентов, а также полезных и вредных примесей. Данные химического состава полезного ископаемого являются основной для определения технологии его переработки и обогащения.
Минералогический состав характеризует минеральные формы проявления элементов, входящих в состав полезного ископаемого. Минералогический состав полезных ископаемых оказывает существенное влияние как на выбор методов, так и на технологические показатели обогащения.
Текстурно-структурные особенности в строении полезного ископаемого характеризуются крупностью, формой, пространственным определением минеральных включений и агрегатов. Текстура руды характеризует взаимное расположение минеральных агрегатов и может быть самой разнообразной.
Характеристика минеральных выделений является основной для разработки технологии и прогноза показателей и переработки полезных ископаемых. Чем крупнее вкрапленность минералов и совершеннее форма их выделений, тем проще технология и выше показатели обогащения полезных ископаемых.
Гранулометрический состав – состав материала, выраженный через
содержание в нем частиц различных классов крупности в процентном отношении к целому.
Для определения гранулометрического состава полезного ископаемого
проводят ситовый анализ с разделением на классы крупности, ограниченные размерами максимального и минимального зерен в них.
В качестве признаков разделения минеральных компонентов при обогащении полезных ископаемых используют их физические и химические свойства, важнейшим из которых являются: механическая прочность, плотность, магнитная проницаемость, электропроводность и диэлектрическая проницаемость, различные виды излучений, смачиваемость и др.
Механическая прочность руд характеризуется дробимостью, хрупкостью, твердостью, абразивностью, временным сопротивлением сжатию и определяет энергетические затраты при их дроблении и измельчении, а также выбор дробильно-измельчительного и обогатительного оборудования.
Плотность горных пород определяется плотностью слагающих их минералов, которые делятся на тяжелые (больше 3 т/м3), средние (3-2,5 т/м3) и легкие (меньше 2,5 т/м3).
Магнитные свойства минералов возникают и проявляются в магнитном поле. Мерой оценки магнитных свойств минералов служит их магнитная проницаемость и связанная с ней магнитная восприимчивость. По магнитной восприимчивости и характеру зависимости магнитных свойств от напряженности внешнего магнитного поля минералы делятся на диамагнитные, парамагнитные и ферромагнитные.
Различия в магнитных свойствах минералов используют для из разделения методами магнитного обогащения.
Электрические свойства минералов определяются электропроводностью и диэлектрической проницаемостью. Различия в электрических свойствах минералов используют для их разделения методами электрического обогащения.
Смачивание – проявление межмолекулярного взаимодействия на границе
соприкосновения трех фаз – твердого тела, жидкости и газа, выражающееся в
растекании жидкости по поверхности твердого тела. Различия в смачиваемости поверхности тонкоизмельченных минеральных частиц используют для их разделения методами флотационного обогащения /20/.
2.2. Минералогический состав
Для кимберлитовых пород трубки «Интернациональная» типичны низкие содержания минералов тяжелой фракции (0,09 – 1,58 %, среднее по 58 пробам – 0,44 %). Распределение индикаторных минералов по фазам внедрения приведено в таблице 1.
Таблица 1. Состав и содержание (кг/т) тяжелой кимберлитовых пород трубки «Интернациональная»
Минералы | Фазы внедрения | Среднее (I-III) | Плотность, т/м3 | ||
I | II | III | |||
Всего тяжелой фракции Пироп Ильменит Оливин Хромшпинелид Моноклинный пироксен Глубинные минералы Сульфиды Сульфаты Алмаз | 6,03 3,17 0,03 0,00 0,36 0,03 3,59 0,41 1,50 0,68 | 8,0 2,78 0,04 0,33 0,32 0,01 3,48 1,70 1,73 0,56 | 11,73 2,85 0,04 3,52 0,49 0,78 7,68 1,07 0,28 0,36 | 7,53 2,63 0,06 1,05 0,37 0,21 4,32 1,41 0,80 1,6 | 3,51 4,72 3,25 4,9 3,41 3,2 3,71 3,28 3,51 |
Пироп преобладает над хромитом и пикроильменитом. Соотношение концентрации этих минералов по трубке в целом составляет 20:2,7:1. Редко встречаются оливин, хромдиопсид, циркон.
По сравнению и составу глубинных минералов кимберлиты трубки
«Интернациональная» отличаются от подавляющего большинства кимберлитовых тел Мирнинского поля и Якутии. Одной из характерных особенностей кимберлитов трубки является низкое содержание минералов титанистой ассоциации (пикроильменит, оранжевый пироп) и повышенное 0 хромистой (хромшпинелид, хромдиопсид, хромистый пироп). Среди гранатов распространены разновидности пироп уваровитового состава, окрашенные в грязно-зеленый цвет. Наблюдается повышенное количество желвачков граната, содержащих многочмсленные включения других минералов. Распространены зерна граната зонального и блокового строения.
Хромшпинелид образует идиоморфные кристаллы и зерна, покрытые множеством вицинальных граней. Повышено количество высокохромистых зерен и разностей, относящихся к алмазной ассоциации.
Ксенолиты пород мантии в трубке «Интернациональная» редки. Они интенсивно серпентинизированы, из первичных минералов сохранились только пироп, хромит, редко клинопироксен и оливин. Резко преобладают деплетированные разности пород, представленные гранатовыми хромитовыми оливинитами, редко гранатовыми лерцолитами. Пироксениты и эклогиты занимают всего лишь 6,2 % общего количества нодулей. В ряде образцов пород мантии установлены высокохромистые разности пиропа и хромита, некоторые из них принадлежат к алмазной ассоциации. Микрозондовый анализ, дополнивший оптические исследования, показал, что в целом гранаты из кимберлитового концентрата имеют более высокую среднюю хромистость, чем гранаты модулей.
Кимберлиты трубки «Интернациональная» уникальны по содержанию
алмазов. В этом отношении они приближаются к лампроитовой трубке Аргайл, но качество алмазов более чем на порядок выше /21/.
Вывод: Тяжелые минералы представлены пиропом, хромшпинелидом, оливином и пикроильменитом с низким содержанием по рудному телу (0,09 – 1,58 %). Плотность тяжелых минералов превышает 3 т/м2. Зная, что алмаз относится к тяжелым минералам (плотность 3,5 т/м3), целесообразно применить гравитационный метод обогащения, основанный на разности плотности минералов.
2.2. Физические свойства
Породы по трубке «Интернациональная» не отличаются высокой прочностью (крепость по шкале Протодъяконова 3-8). Средняя плотность
рудного тела составляет 2,68 т/м2.
До глубины 300 м трубка сложена слабомагнитными кимберлитами. Их магнитная восприимчивость в интервалах 0 - 50, 50-100 и 100-300 м составляет в среднем соответственно 37 • 10-6, 65 - 10-6 и 35 - 10-6 СГС. Лишь на глубине 460-480 м подсечен участок кимберлитов с высокой магнитной восприимчивостью, достигающей 2100 – 10-6 СГС. Остаточная намагниченность кимберлитов трубки также низкая, в большинстве случаев она меньше индуцированной.
Преобладающий состав кимберлитовых пород на разных глубинах определяет уровень значений их электрических параметров. Удельное электрическое сопротивление мерзлых кимберлитовых брекчий верхних горизонтов на частоте 0,625 МГц находится в интервале значений 100 – 300 Ом∙м, ε – 67 – 80 εо, k// - 0,07 – 0,26 Нп/м.
Алмаз по отношению к другим минералам трубки обладает отличительными свойствами, например как, высоким преломлением при рентгеновских лучах, высокой твердостью (по шкале Мооса 10) и теплопроводностью (146,538 Вт/м∙К). Температурный коэффициент алмаза обычно составляет от 0,9∙10-6 до 1,45∙10-6 К-1.. Средний показатель преломления бесцветных кристаллов в желтом свете 2,4175±0,0003, а для желтоватых алмазов он колеблется в пределах 2,419-2,421 и чаще 2,417. Диэлектрическая постоянная кристаллов алмаза составляет 16-16,5; удельное электрическое сопротивление его очень велико и равно в среднем 1012 – 1014 Ом∙см.
Вывод: Таким образом, исходя из выше приведенной физической характеристики руды трубки «Интернациональная» целесообразно применить электрический, радиометрический и магнитный методы обогащения.
2.4. Химический состав
В общем ряду кимберлитов породы трубки «Интернациональная» выделяются несколько пониженной общей железистостью, главным образам за счет более низкого содержания трехвалентно железа. В вертикальном разрезе отмечается определенная петрохимическая зональность, выраженная в том, что в верхней части трубки, включая интервал 300 — 400 м, повышено содержание SiO2, Al2O3 и понижено MgO. В верхних горизонтах повышено также содержание СаО и СО2. С глубины примерно 400 м возрастает концентрация Nа2O и К2О. Выявленная вертикальная неоднородность химического состава кимберлитов довольно четко увязывается с литологическими особенностями вмещающих толщ, оказывающими влияние на состав кимберлитов.
Вывод: Таким образом, при применении флотационного метода руды данной трубки не повлияют на процесс флотации мелких кристаллов алмаза
2.5. Текстурно-структурный состав
Ксенолиты осадочных пород представлены неправильной формы остроугольными обломками вмещающих карбонатных пород нижнепалеозойского возраста. Размеры ксенолитов колеблются в широких пределах: от микроскопических до 4,1 см.
Вкрапленники представлены псевдоморфозами серпентина по энстатику, реже оливину, изредка наблюдаются флогопит, пироп, хромшпинелиды и пикроильменит. Среднее содержание псевдоморфоз составляет 12,8%, при колебаниях от 8,9 до 18,3%. В порфировых выделениях различаются всевдоморфозы двух генераций. Псевдоморфоз серпентина по энстатику установлены во вкрапленниках первой генерации, размерам от 1 до 6 мм, реже 11-12 мм.
В отличие от беститовых образований по предполагаемому энстатику псевдоморфозы по оливину имеют размеры в пределах 1-6,8 мм и петельчатое, пластинчато-метельное строение.
Серпентин развивается по трещинам в оливине, постепенно замещая все зерно. Отсюда петельчатые, пластинчато-петельчатые и очень редко пластинчатые структуры. Пластины и петли сложены гамма-хризолитов. Между ними наблюдаются линзовидные гнезда пиролита. В карбонатизированных участках кимберлитов брекчиевой текстуры вокруг псевдоморфоз наблюдаются цепочковидные выделения карбоната, отделенные от основной массы агрегатом серпентина и рудного минерала.
Основная масса кимберлитов перовой фазы внедрения представляет собой агрегат магнезиального хлорита, серпентина, флогопита, кальцита и доломита. Перечисленные минералы в выделенных разновидностях содержатся в крайне переменных количествах. В породах брекчиевой текстуры кальцит и доломит в большинстве случае преобладают, а в кимберлите массивной текстуры нередко отсутствуют. Карбонат основной массы образует политоморфные агрегаты и отмечаются в виде микролитов, содержание которых в породе не постоянное.
Кимберлиты второй фазы внедрения являются преобладающими в разведанном участке теле (54,2 % объема), имеют темно-серую с голубовато-зеленым оттенком и серую (брекчии) окраску. Для брекчий характерен также пятнистый (серый, зеленый) цвет, выраженный наличием различных по составу и интенсивности окраски включений.
В кимберлитах второй фазы внедрения содержание ксенолитов колеблется в широких пределах (от единичных до 36 %), но среднее содержание их не высокое (8,4 %).
Характерной особенностью обломочного материала кимберлитов второй фазы внедрения является широкий спектр их петрографического состава.
Карбонатные породы представлены доломитовыми известняками, известковистыми доломитами преимущественно вмещающих трубку тела в шлифах доломитов были обнаружены своеобразные округлые проблематические органические образования.
Кимберлиты третьей фазы внедрения – серые и темно –серые породы, отличающиеся от первой и второй фаз внедрения несколько пониженным содержанием ксеногенного карбонатного материала вмещающих пород (5,4%), небольшими размерами вкрапленников, часто образующих крупные (до 15-25) монокристаллические зерна изометрической формы и содержащих нередко включения пиропа и хрошпинелидов.
Ксенолиты карбонатных пород представлены не разновидностями, что и во второй фазе внедрения кимберлитов, но обломки ксенолитов имеют более
угловатую форму. Включения диабазов встречаются в единичных обломках.
Характерной особенностью для оливинов третьей фазы внедрения являются наименьшая степень замещения оливина. Его содержание в 7,1 раза
выше, чем в кимберлитах второй фазы внедрения.
В псевдоморфозах по оливину можно выделить следующие минеральные ассоциации: а) серпентин-магнетит; б) серпентин-доломит-кальцит, сидерит, флогопит; в) доломит-кальцит-серпентин9сидерит гидротальеит, г) доломит-кальцит-хлорит.
Основная масса мелко- и среднезернистого строения карбонатсерпентиновая, участками существенно карбонатная. Карбонатные минералы представлены монокристаллическим и поликристаллическим кальцитом. Часто кальцит образует и микролиты. Кроме этого попадается доломит и сидерит, а также мелкая вкрапленность слюды.
По морфологии кристаллы алмаза распределяются следующим образом (%): октаэдры — 63, ромбододекаэдры – 9, комбинационные формы — 28. Подавляющее большинство алмазов бесцветные (70,7%).
Вывод: Таким образом, из выше приведенной характеристики по текстурно-структурному составу минимальный размер зерен составляет 0,5 мм, содержание в исходном сырье не превышает 14 %. Следовательно, нет необходимости применять многостадиальное дробление (измельчение) и классификацию исходного материала.
2.6. Гранулометрический состав
Гранулометрический состав – состав минерала, выраженный через содержание в нем частиц различных классов крупности в процентном отношении к целому.
Для определения гранулометрического состава полезного ископаемого
проводят ситовой анализ с разделением на классы крупности, ограниченные размерами максимального и минимального зерен в них, и сопровождается анализом распределения отдельных элементов в различных классах крупности, а также соотношения между свободными зернами и сростками в них при различной степени измельчения полезных ископаемых.
Гранулометрический состав поступающей руды из рудника «Интернациональная» характеризуется меньшим (0,9 %) содержанием мелющей среды. Максимальная крупность руды в исходном материале составляет -200+100 мм. Кумулятивные кривые исходной руды и дробленной руды представлены на рис.
Относительное содержание раскрытых алмазов (класса -4,75+2 – в 1,25 раза; -2+1 – в 1,43 раза; -1+0,5 – в 1,5 раза). Содержание алмазов крупностью -4,75+0,5 составляет 51,6%. Гранулометрический состав исходной руды трубки «Интернациональная» приведена в таблице 2.
Из выше приведенной таблицы гранулометрического состава исходной руды можно отметить, что содержание крупных кусков руды очень низкое. Это сказывается отрицательно на процесс измельчения в мельницах типа ММС. Увеличивается время измельчения, износ оборудования на 1 тонну руды,
Таблица 2. Гранулометрический состав исходной руды трубки «Интернациональная»
Способ добычи | -200+100 | -100+50 | -50+20 | -20+10 | -10+6 | -6+4 | -4+1,6 | -1,6+0,5 | -0,5 | Итого |
Комбайновый | 0,9 | 3,3 | 19,4 | 23,2 | 12,1 | 8 | 12,6 | 6,7 | 13,8 | 100 |
расход электроэнергии на переработку 1 тонны руды и снижается производительность оборудования. Поэтому целесообразно применить дробилку объемного сжатия 45-4680-GR, фирмы «Крупп полизиус».
Руда поступает на фабрику автотранспортом в виде кусков различной крупности -200+0 мм, максимальный кусок достигает 200 мм. Ценный компонент находится в тесном срастании с рудными минералами, чтобы освободить ценные минералы, необходимо куски раздробить. В качестве аппаратов для дробления плотных пород, работающих на принципе объемного сжатия, применяется валковая дробилка
Конструкция дробилки обеспечивает сохранение всех параметров при температуре окружающего воздуха от +40°С до -40°С.
Основным показателем дробления является степень дробления:
где: Dmax - максимальный кусок до дробления, мм
dmax - максимальный кусок после дробления, мм
Вывод: применение дробилки в начале технологической схемы не целесообразно, т.к. степень дробления исходной руды с крупностью 200 мм составляет 400. Целесообразно её применять для додрабливания (до раскрытия) руды.
Таким образом, из вышеуказанных свойств руды трубки «Интернациональная» можно отметить, что целесообразно применять радиометрический, гравитационный, электрический и магнитный методы обогащения.
Технологическая часть
3.1. Основные положения
Извлечение алмазов отличается от других полезных ископаемых некоторыми особенностями. Прежде всего, следует указать на чрезвычайно низкое содержание ценного компонента по сравнению с другими видами минерального сырья. Можно считать, что в среднем одна часть алмазов приходится на 20 млн. частей руды.
Кроме того, в процессе обработки руды необходимо осторожно применять операции дробления и измельчения ввиду хрупкости алмазов и резкого снижения их ценности с уменьшением размеров кристаллов.
Большая стоимость алмазов требует применения таких процессов, которые обеспечили бы высокую степень извлечения. Даже небольшие по количеству потери алмазов могут оказаться значительными в ценностном выражении. Иногда один только кристалл высокого качества, оставшихся в хвостах, представляет собой крупные потери.
Технология извлечения алмазов обычно включает следующие процессы:
дезинтеграцию исходного сырья и превращение его в рыхлую смесь для освобождения алмазов от их связи с другими компонентами;
получение первичных концентратов разделением рыхлой смеси на два продукта, в одном из которых, значительно меньшем по объёму, сконцентрированы алмазы;
извлечение алмазов из полученных таким образом первичных концентратов.
Цель рудоподготовки – подготовка сырья к последующему обогащению с учетом возможности применения тех или иных методов обогащения.
При выборе технологии руподготовки алмазосодержащих кимберлитов необходимо решить несколько вопросов:
1. Сохранность кристаллов алмаза при раскрытии сростков минералов;
2. Эффективность раскрытия сростков минералов;
3. Определение начальной и конечной крупностью дробимого материала
К технологическим свойствам алмаза, используемым при разделении от пустой породы в процессе обогащения, относится его плотность (3,51 т/м3), а также механические (твердость 10 по шкале Мооса, высокая абразивность, очень хрупкий), радиометрические (высокое показатель преломления), магнитные (не магнитен),электрические (не электропроводен) и физико-химические (алмаз природно гидрофобен) свойства
Следовательно, на различии алмаза и породы в вышеприведенных свойствах при обогащении алмазосодержащего сырья применяют гравитационный, радиометрический, магнитный, электрический и флотационный методы обогащения.
Высокое извлечение можно достичь при последовательном применении всех вышеуказанных методов обогащения.
Следовательно, необходимо отметить, что основное извлечение осуществляется за счет радиометрического метода. Применение за основу извлечения одного метода обогащения недостаточно, чтобы получить высокие технологические показатели.
Применение тяжелосредного сепаратора (гравитационный метод) может повысить технологические показатели. За счет большой разности в плотности минералов. Большим недостатком является то, что не недостаточно применяются все свойства алмаза, по которым можно значительно повысить содержание алмазов в концентратах и также не возможно извлечь кристаллы мелких размеров алмаза.
Применение флотационного метода обогащения дает возможность извлечь мелкие кристаллы алмазов. Этот метод значительно повышает эффективность обогащения (извлечение) по схеме в целом. Также применение двух стадиального грохочения заметно улучшает процесс тяжелосредной сепарации и значительно удаляет мелких шламов из технологической схемы. Максимальное удаление шламов улучшает показатели обогащения. Следовательно, при применении описываемой схемы можно достичь оптимальных показателей обогащения.
- применение флотационного обогащения увеличивает технологические показатели схемы;
- низкую циркуляционную нагрузку, за счет этого не подвергаются кристаллы алмаза к большим механическим нагрузкам. Уменьшение механических нагрузок на алмазы не приводит к техногенным разрушениям;
- максимальное удаление шламов из процессов обогащения;
3.2 Описание схемы
Исходная руда поступает на фабрику автотранспортом в виде кусков различной крупности. Питателями руда подаётся на передел I стадии грохочения, где разделяется на классы крупности +50, -50+0.
Руда классом +50, а также хвосты ТСС и отсадки подаются на измельчение в валковый пресс, который обеспечивают достаточное раскрытие сростков алмазов с породой, при этом достигая максимальной природной сохранности алмазов.
В схеме обогащения алмазосодержащих руд перед гравитационными процессами может быть предусмотрены грохочение и классификация, что обеспечивает большую эффективность обогатительных операций. Преимущества обогащения классифицированного материала по сравнению с неклассифицированным, заключается в том, что можно проводить обогащение в оптимальных условиях для данной фракции, что неосуществимо при обогащении неклассифицированного материала.
Продукт разгрузки валкового пресса транспортируется на спиральный классификатор. Так же туда поступает продукт после грохочения классом -50+0. Слив классификации поступает в хвостохранилище.
Пески классификации поступают на 2 стадию грохочения. На грохотах материал рассеивается на 2 класса крупности -50+20 мм, -20+0 мм. Классифицируя, таким образом, материал на классы крупности -50+20 мм и -20+0 мм, мы обеспечиваем максимальную эффективность работы сепараторов РЛС. Это наиболее эффективный метод обогащения крупных классов алмазосодержащего сырья.
Первый продукт грохочения - 2 -50+20 мм следует на РЛС, второй продукт -20+0 мм поступает на третью стадию грохочения.
Концентрат РЛС уходит в цех доводки, а хвосты доизмельчаются в валковом прессе.
После третьей стадии грохочения - 3 класс крупности –20+5 мм поступает на ТСС-1, -5+0 на обесшламвливание
Продукты операции ТСС направляются следующим образом: концентрат в цех доводки, а хвосты - на доизмельчение в валковом прессе. После обесшламвливания, пески уходят на четвертую стадию грохочения, а слив направляется в отвал
Далле продукты поступают на грохочение, где делятся на классы: -32+16, -16+6, -6+3 и -3+1. Затем продукт следует на рентгенолюменисцентную сепарацию.
На четвертой стадии грохочения происходит процесс разделения по следующим классам: -5+2, который уходит на винтовую сепарацию, и класс -2+0, уходящий на пенную сепарацию. Концентрат пенной сепарации уходит в цех доводки, а хвосты – в отвал.
После винтовой сепарации продукт попадает в отсадочную машину. Концентрат отсадки уходит в цех доводки, а хвосты доизмельчаются в валковом прессе.
Расчет качественно-количественной схемы
Целью расчёта качественно-количественной схемы обогащения, является определение для всех продуктов и операций схемы ряда показателей, характеризующих технологический процесс качественно и количественно. К числу таких показателей относятся веса и выхода продуктов (θ; γ); извлечения (ε, Ε) и содержания (β) полезных компонентов.
Задача расчета качественно-количественной схемы сводится к решению следующих вопросов:
• установление необходимого и достаточного числа исходных показателей для полного расчета схемы;
• выбор исходных показателей;
• определение остальных показателей схемы с помощью составления и решения уравнений баланса.
При расчете качественно-количественной схемы используем уравнения баланса:
по руде и продуктам обогащения:
;
по ценному компоненту:
Расчёт качественно-количественной схемы обогащения алмазосодержащих руд имеет ряд специфических особенностей:
Масса исходной руды должна быть равна массе отвальных хвостов, т.к. массой конечной продукции (алмазов) пренебрегают вследствие её незначительной величины сравнении с исходным продуктом;
;
Исходное содержание алмазов в руде задано в условных единицах;
Расчёт качественно-количественной схемы сначала производится по выходам продуктов обогащения (γ, %) и извлечениям ценного компонента в продукты обогащения (ε, %), затем вычисляется содержание ценного компонента в продуктах обогащения (β, кар/т);
Расчёт схемы осуществляется по стандартной методике по узлам снизу вверх.
Исходные данные: Q- 74,61 т/ч, α-0,00018 кар/т.
Рассчитываем по формулам 100 = к + n, 100 = кк + nn недостающие показатели выходов, извлечения и заносим полученные данные в таблицу.
Таблица 3. Результаты расчета качественно-количественной схемы
№ | Процесс | Q, т/ч | γ, % | β, % | ε, % |
I | Грохочение | ||||
поступает: | |||||
1 | исходная руда | 74,61 | 100 | 1,8*10-6 | 100 |
ИТОГО: | 74,61 | 100 | 1,8*10-6 | 100 | |
выходит: | |||||
2 | продукт класса +50 | 3,13 | 4,19 | 203,8*10-6 | 33,5 |
3 | продукт класса -50+0 | 71,48 | 95,8 | 1,37*10-6 | 73 |
ИТОГО: | 74,61 | 100 | 1,8*10-6 | 100 | |
II | Дробление | ||||
поступает: | |||||
2 | продукт класса +50 | 3,13 | 4,19 | 203,8*10-6 | 33,5 |
16 | хвосты ТСС | 20,6 | 27,61 | 0,03*10-6 | 0,5 |
26 | хвосты отсадки | 1,08 | 1,44 | 0,99*10-6 | 0,8 |
ИТОГО: | 24,815 | 33,25 | 1,78*10-6 | 33,5 | |
выходит: | |||||
5 | дробленный продукт -50+0 | 24,815 | 33,25 | 1,78*10-6 | 33,5 |
ИТОГО: | 24,815 | 33,25 | 1,78*10-6 | 33,5 | |
III | Классификация | ||||
поступает: | |||||
3 | продукт класса -50+0 | 71,48 | 95,8 | 1,37*10-6 | 73 |
5 | дробленный продукт -50+0 | 24,815 | 33,25 | 1,78*10-6 | 33,5 |
15 | дробленный продукт -16+0 | 1,63 | 2,19 | 4,6*10-6 | 5,7 |
ИТОГО: | 97,93 | 131,26 | 1,53*10-6 | 112,2 | |
выходит: | |||||
7 | пески классификации | 54,995 | 73,27 | 2,75*10-6 | 112 |
8 | слив классификации | 43,29 | 58,03 | 0,62*10-8 | 0,2 |
ИТОГО: | 97,93 | 131,26 | 1,53*10-6 | 112,2 | |
IV | Грохочение 2 | ||||
поступает: | |||||
7 | пески классификации | 54,637 | 73,27 | 2,75*10-6 | 112 |
63 | хвосты цеха доводки | 0,358 | 0,43 | 0,0187 | 44,62 |
ИТОГО: | 54,995 | 73,7 | 2,75*10-6 | 156,62 | |
выходит: | |||||
9 | продукт класса -50+20 | 1,64 | 2,19 | 71,21*10-6 | 87 |
10 | продукт класса -20+0 | 53,39 | 71,56 | 3,8*10-6 | 151,82 |
ИТОГО: | 54,995 | 73,7 | 2,75*10-6 | 156,62 | |
V | РЛС | ||||
поступает: | |||||
9 | продукт класса -50+20 | 1,64 | 2,19 | 71,21*10-6 | 87 |
ИТОГО: | 1,64 | 2,19 | 71,21*10-6 | 87 | |
выходит: | |||||
11 | к-т РЛС | 0,0023 | 0,003 | 0,048 | 81,3 |
12 | хв. РЛС | 1,63 | 2,19 | 4,6*10-6 | 5,7 |
ИТОГО: | 1,64 | 2,19 | 71,21*10-6 | 87 | |
VI | Грохочение 3 | ||||
поступает: | |||||
10 | продукт класса -20+0 | 53,39 | 71,56 | 3,8*10-8 | 151,82 |
ИТОГО: | 53,39 | 71,56 | 3,8*10-6 | 151,82 | |
выходит: | |||||
13 | продукт классом -20+5 | 20,73 | 27,79 | 3,62*10-6 | 56 |
14 | продукт классом -5+0 | 32,65 | 43,77 | 3,9*10-6 | 95,32 |
ИТОГО: | 53,39 | 71,56 | 3,8*10-6 | 151,82 | |
VII | ТСС | ||||
поступает: | |||||
13 | продукт классом -20+5 | 20,73 | 27,79 | 3,62*10-6 | 56 |
ИТОГО: | 20,73 | 27,79 | 3,62*10-6 | 56 | |
выходит: | |||||
16 | хв. ТСС | 20,6 | 27,61 | 0,03*10-6 | 0,5 |
17 | к-т ТСС | 0,13 | 0,17 | 579,3*10-6 | 55,5 |
ИТОГО: | 20,73 | 27,79 | 3,62*10-6 | 56 | |
VIII | Обесшламливание | ||||
поступает: | |||||
14 | продукт классом -5+0 | 32,65 | 43,77 | 3,9*10-6 | 95,32 |
ИТОГО: | 32,65 | 43,77 | 3,9*10-6 | 95,32 | |
выходит: | |||||
18 | пески обесшламливания (-5+1) | 4,84 | 6,49 | 10,17*10-6 | 36,7 |
19 | слив обесшламвливания (-1+0) | 27,77 | 37,22 | 0,015*10-6 | 0,32 |
ИТОГО: | 32,65 | 43,77 | 3,9*10-6 | 95,32 | |
IX | Дробление 2 | ||||
поступает: | |||||
12 | хв. РЛС | 1,63 | 2,19 | 4,6*10-6 | 5,7 |
ИТОГО: | 1,63 | 2,19 | 4,6*10-6 | 5,7 | |
выходит: | |||||
15 | дробленный продукт -16+0 | 1,63 | 2,19 | 4,6*10-6 | 5,7 |
ИТОГО: | 1,63 | 2,19 | 4,6*10-6 | 5,7 | |
X | Грохочение 4 | ||||
поступает: | |||||
18 | пески обесшламливания (-5+1) | 4,84 | 6,49 | 10,17*10-6 | 36,7 |
ИТОГО: | 4,84 | 6,49 | 10,17*10-6 | 36,7 | |
выходит: | |||||
20 | продукт класса -5+2 | 4,5 | 6,03 | 24,77*10-6 | 83,08 |
21 | продукт класса -2+1 | 0,34 | 0,45 | 47,15*10-6 | 11,92 |
ИТОГО: | 4,84 | 6,49 | 10,17*10-6 | 36,7 | |
XI | Пенная Сепарация | ||||
поступает: | |||||
21 | продукт класса -2+1 | 0,34 | 0,45 | 47,15*10-6 | 11,92 |
ИТОГО: | 0,34 | 0,45 | 47,15*10-6 | 11,92 | |
выходит: | |||||
22 | к-т Пенной сепарации | 0,03 | 0,04 | 527,4*10-6 | 11,72 |
23 | хв пенной сепарации | 0,31 | 0,41 | 0,86*10-6 | 0,2 |
ИТОГО: | 0,34 | 0,45 | 47,15*10-6 | 11,92 | |
XII | Винтовая сепарация | ||||
поступает: | |||||
20 | продукт класса -5+2 | 4,5 | 6,03 | 24,77*10-6 | 83,08 |
ИТОГО: | 4,5 | 6,03 | 24,77*10-6 | 83,08 | |
выходит: | |||||
25 | к-т винтовой сепарации | 1,35 | 1,81 | 82,16*10-6 | 82,8 |
24 | хв винтовой сепарации | 3,15 | 4,42 | 0,11*10-6 | 0,28 |
ИТОГО: | 4,5 | 6,03 | 24,77*10-6 | 83,08 | |
XIII | Отсадка | ||||
поступает: | |||||
25 | к-т винтовой сепарации | 1,35 | 1,81 | 82,16*10-6 | 82,8 |
ИТОГО: | 1,35 | 1,81 | 82,16*10-6 | 82,8 | |
выходит: | |||||
27 | к-т отсадки | 0,27 | 0,36 | 402,17*10-6 | 82 |
26 | хв отсадки | 1,08 | 1,44 | 0,99*10-6 | 0,8 |
ИТОГО: | 1,35 | 1,81 | 82,16*10-6 | 82,8 |
Технологический баланс: 98,86~100
Баланс металлов: 100*1,8*10-6~0,018
3.4. Расчет водно-шламовой схемы
Целью проектирования шламовой схемы является: обеспечение оптимальных отношений Ж:Т в операциях схемы; определение количества волы, добавляемой в операции или. наоборот. выделяемой из продуктовпри операциях обезвоживания; определение отношений Ж:Т в продуктах схемы; определение объёмов пульпы для всех продуктов и операций схемы; определение общей потребности воды по проектируемой обогатительной фабрики и составление баланса по воде.
Принятые обозначения:
R - весовое отношение жидкого к твердому в операции или в продукте,
численно равное отношению м3 воды/1 т твердого;
W - количество воды в операции или в продукте, м3 в единицу времени;
L - количество воды, добавляемой в операцию или к продукту, м3 в единицу времени;
S - влажность продукта в долях единицы;
δ - плотность твердого в продукте, т/м3;
V - объем пульпы в продукте, м3 в единицу времени;
L - удельный расход свежей воды, добавляемой в отдельные операции,
м3/т твердого
Для успешного осуществления некоторых технологических операций необходимо не только обеспечить оптимальное отношение Ж:Т в питании, но и подавать в операцию определенное количество дополнительной воды. Нормы расхода дополнительной воды на 1т обрабатываемого продукта являются также исходными показателями при расчете схемы.
Оптимальные отношения Ж:Т в операциях и продуктах, а также расход дополнительной воды колеблются в широких пределах в зависимости от свойств обрабатываемого материала и требований, предъявляемых к продуктам обработки. Поэтому исходные показатели должны устанавливаться на основании результатов исследовательских работ и по практическим данным обогатительных фабрик.
Водно-шламовые схемы алмазоизвлекающих фабрик состоят на 90-95 % из оборотного водоснабжения и, только 10% от общего водопотребления, обеспечивается за счет подпитки свежей водой. В основном, свежая вода используется на хозбытовые нужды фабрики (питьевое водоснабжение, приготовление пищи, санитарно-бытовые потребности, в очень незначительной мере — в отдельные точки технологического процесса, например, на охлаждение рентгеновских трубок рештенолюминесцентных сепараторов, в сальниковые уплотнения насосов и т. д.).
На фабриках, как правило, два контура оборотного водоснабжения. Внешний контур — через хвостохранилище. Вода этого контура после осветления в хвостохранилище подается на цех рудоподготовки, на гравитационное обогащение, на транспорт зернистой массы внутри фабрики и, наконец, для транспорта хвостовых продуктов к месту их складирования в хвостохранилище. Внутренний контуру — это замкнутый цикл водооборота пенной сепарации. Этот замкнутый контур изолирован от всей остальной системы водопотребления фабрики, чтобы не допустить потерь реагентов и сократить расходы тепла на водоподогрев для технических нужд. Если осветление воды первого контура проходит достаточно эффективно, то очистка технологических вод пенной сепарации, шламоосаждение и шламоотделение требует специальных технологий и оборудования и осуществляется, как правило, с низким качеством, что отрицательно отражается на технологических показателях процесса.
Количество твердого вещества берем из качественно — количественной схемы, а содержание твердого - берем из справочника.
Таблица 4. Результаты расчета водно-шламовой схемы
№ | Процесс | Q, т/ч | T | R | W | V |
I | Грохочение | |||||
поступает: | ||||||
1 | исходная руда | 74,61 | 95 | 0,053 | 3,927 | 30,573 |
L1 | свежая вода | 46,63 | 46,63 | |||
ИТОГО: | 74,61 | 59,61 | 0,678 | 50,557 | 77,20 | |
выходит: | ||||||
2 | продукт класса +50 | 3,13 | 82 | 0,220 | 0,687 | 1,805 |
3 | продукт класса -50+0 | 71,48 | 58,90 | 0,698 | 49,870 | 75,40 |
ИТОГО: | 74,61 | 59,61 | 0,678 | 50,557 | 77,20 | |
II | Дробление | |||||
поступает: | ||||||
2 | продукт класса +50 | 3,13 | 70 | 0,429 | 1,341 | 2,459 |
16 | хвосты ТСС | 20,6 | 52,4 | 0,908 | 18,713 | 26,070 |
26 | хвосты отсадки | 1,08 | 45,8 | 1,183 | 1,278 | 1,664 |
ИТОГО: | 24,815 | 53,77 | 0,860 | 21,332 | 30,193 | |
выходит: | ||||||
5 | дробленный продукт -50+0 | 24,815 | 53,77 | 0,860 | 21,332 | 30,193 |
ИТОГО: | 24,815 | 53,77 | 0,860 | 21,332 | 30,193 | |
III | Классификация | |||||
поступает: | ||||||
3 | продукт класса -50+0 | 71,48 | 58,90 | 0,698 | 49,870 | 75,398 |
5 | дробленный продукт -50+0 | 24,815 | 53,77 | 0,860 | 21,332 | 30,193 |
15 | дробленный продукт -16+0 | 1,63 | 98 | 0,020 | 0,033 | 0,615 |
ИТОГО: | 97,93 | 57,89 | 0,727 | 71,236 | 106,207 | |
выходит: | ||||||
7 | пески классификации | 54,995 | 80 | 0,250 | 13,749 | 33,390 |
8 | слив классификации | 43,29 | 42,96 | 1,328 | 57,487 | 72,82 |
ИТОГО: | 97,93 | 57,89 | 0,727 | 71,236 | 106,207 | |
IV | Грохочение 2 | |||||
поступает: | ||||||
7 | пески классификации | 54,637 | 80 | 0,25 | 13,749 | 33,390 |
63 | хвосты цеха доводки | 0,358 | 95 | 0,053 | 0,019 | 0,147 |
L2 | свежая вода | 32,18 | 32,18 | |||
ИТОГО: | 54,995 | 54,48 | 0,835 | 45,948 | 65,717 | |
выходит: | ||||||
9 | продукт класса -50+20 | 1,64 | 63 | 0,587 | 0,963 | 1,549 |
10 | продукт класса -20+0 | 53,39 | 54,27 | 0,843 | 44,984 | 64,17 |
ИТОГО: | 54,995 | 54,48 | 0,835 | 45,948 | 65,717 | |
V | РЛС | |||||
поступает: | ||||||
9 | продукт класса -50+20 | 1,64 | 63 | 0,587 | 0,963 | 1,549 |
ИТОГО: | 1,64 | 97 | 0,031 | 0,051 | 0,636 | |
выходит: | ||||||
11 | к-т РЛС | 0,0023 | 91 | 7,590 | 0,017 | 0,021 |
12 | хв. РЛС | 1,63 | 98 | 0,020 | 0,033 | 0,615 |
ИТОГО: | 1,64 | 97 | 0,031 | 0,051 | 0,636 | |
VI | Грохочение 3 | |||||
поступает: | ||||||
10 | продукт класса -20+0 | 53,39 | 54,272 | 0,843 | 44,984 | 64,168 |
L3 | свежая вода | 31,405 | 31,405 | |||
ИТОГО: | 53,39 | 41,14 | 1,431 | 76,389 | 95,573 | |
выходит: | ||||||
13 | продукт классом -20+5 | 20,73 | 55 | 0,818 | 16,961 | 24,364 |
14 | продукт классом -5+0 | 32,65 | 35,46 | 1,820 | 59,429 | 71,21 |
ИТОГО: | 53,39 | 41,139 | 1,431 | 76,389 | 95,573 | |
VII | ТСС | |||||
поступает: | ||||||
13 | продукт классом -20+5 | 20,73 | 55 | 0,818 | 16,961 | 24,364 |
L4 | свежая вода | 25,918 | 25,918 | |||
ИТОГО: | 20,73 | 32,59 | 2,068 | 42,879 | 50,282 | |
выходит: | ||||||
16 | хв. ТСС | 20,6 | 32,52 | 2,075 | 42,754 | 50,111 |
17 | к-т ТСС | 0,13 | 51 | 0,961 | 0,125 | 0,171 |
ИТОГО: | 20,73 | 32,59 | 2,068 | 42,879 | 50,282 | |
VIII | Обесшламливание | |||||
поступает: | ||||||
14 | продукт классом -5+0 | 32,65 | 35,459 | 1,820 | 59,429 | 71,208 |
L5 | свежая вода | 15,887 | 15,887 | |||
ИТОГО: | 32,65 | 30,24 | 2,307 | 75,316 | 87,095 | |
выходит: | ||||||
18 | пески обесшламливания (-5+1) | 4,84 | 75 | 0,333 | 1,613 | 3,342 |
19 | слив обесшламвливания (-1+0) | 27,77 | 27,37 | 2,654 | 73,702 | 83,75 |
ИТОГО: | 32,65 | 30,24 | 2,307 | 75,316 | 87,095 | |
IX | Дробление 2 | |||||
поступает: | ||||||
12 | хв. РЛС | 1,63 | 98 | 0,020 | 0,033 | 0,615 |
ИТОГО: | 1,63 | 98 | 0,020 | 0,033 | 0,615 | |
выходит: | ||||||
15 | дробленный продукт -16+0 | 1,63 | 98 | 0,020 | 0,033 | 0,615 |
ИТОГО: | 1,63 | 98 | 0,020 | 0,033 | 0,615 | |
X | Грохочение 4 | |||||
поступает: | ||||||
18 | пески обесшламливания (-5+1) | 4,84 | 75 | 0,333 | 1,613 | 3,342 |
L6 | свежая вода | 2,2 | 2,2 | |||
ИТОГО: | 4,84 | 55,93 | 0,788 | 3,813 | 5,542 | |
выходит: | ||||||
20 | продукт класса -5+2 | 4,5 | 57 | 0,754 | 3,395 | 5,002 |
21 | продукт класса -2+1 | 0,34 | 44,82 | 1,231 | 0,419 | 0,54 |
ИТОГО: | 4,84 | 55,93 | 0,79 | 3,81 | 5,54 | |
XI | Пенная сепарация | |||||
поступает: | ||||||
21 | продукт класса -2+1 | 0,34 | 44,82 | 1,231 | 0,419 | 0,540 |
L7 | свежая вода | 0,21 | 0,21 | |||
ИТОГО: | 0,34 | 35,10 | 1,849 | 0,629 | 0,750 | |
выходит: | ||||||
22 | к-т пенной сепарации | 0,03 | 44 | 1,273 | 0,038 | 0,049 |
23 | хв пенной сепарации | 0,31 | 34,43 | 1,905 | 0,590 | 0,70 |
ИТОГО: | 0,34 | 35,102 | 1,849 | 0,629 | 0,750 | |
XII | Винтовая сепарация | |||||
поступает: | ||||||
20 | продукт класса -5+2 | 4,5 | 57 | 0,754 | 3,395 | 5,002 |
L8 | свежая вода | 11,25 | 11,25 | |||
ИТОГО: | 4,5 | 23,51 | 3,254 | 14,645 | 16,252 | |
выходит: | ||||||
25 | к-т винтовой сепарации | 1,35 | 50 | 1 | 1,350 | 1,832 |
24 | хв винтовой сепарации | 3,15 | 19,16 | 4,221 | 13,295 | 14,42 |
ИТОГО: | 4,5 | 23,51 | 3,254 | 14,645 | 16,252 | |
XIII | Отсадка | |||||
поступает: | ||||||
25 | к-т винтовой сепарации | 1,35 | 50 | 1 | 1,350 | 1,832 |
L9 | свежая вода | 0,45 | 0,45 | |||
ИТОГО: | 1,35 | 42,86 | 1,333 | 1,8 | 2,282 | |
выходит: | ||||||
27 | к-т отсадки | 0,27 | 34,09 | 1,933 | 0,522 | 0,618 |
26 | хв отсадки | 1,08 | 45,8 | 1,183 | 1,278 | 1,664 |
ИТОГО: | 1,35 | 42,86 | 1,333 | 1,800 | 2,282 |
Таблица 5. Баланс воды
№, п/п | Поступает | W, м3/ч | №, п/п | Уходит | W, м3/ч |
ИСХОДНАЯ РУДА | 3,927 | 8 | слив классификации | 57,487 | |
L1 | СВЕЖАЯ ВОДА | 46,630 | Удал. вода перед РЛС | 0,912 | |
L2 | СВЕЖАЯ ВОДА | 32,180 | 11 | к-т РЛС | 0,017 |
L3 | СВЕЖАЯ ВОДА | 31,405 | 19 | слив обесшламвливания (-1+0) | 73,702 |
L4 | СВЕЖАЯ ВОДА | 25,918 | 23 | хв пенной сепарации | 0,590 |
L5 | СВЕЖАЯ ВОДА | 15,887 | 17 | к-т ТСС | 0,125 |
L6 | СВЕЖАЯ ВОДА | 2,200 | 22 | к-т пенной сепарации | 0,038 |
L7 | СВЕЖАЯ ВОДА | 0,210 | 27 | к-т отсадки | 0,522 |
L8 | СВЕЖАЯ ВОДА | 11,25 | 24 | хв винтовой сепарации | 13,295 |
L9 | СВЕЖАЯ ВОДА | 0,45 | |||
ИТОГО | 146,64 | ИТОГО | 146,69 |
Выбор и расчет оборудования
Выбор и расчет грохотов.
На первую стадию грохочения выбираем вибрационные инерционные грохоты с самобалансным вибратором, так как эти грохоты рекомендуются для грохочения с отмывкой, для обезвоживания.
Для первой стадии грохочения выбираем валковый грохот Грохот ГВII-50 с площадью грохочения 4,5 м2. Размер отверстий сит: 50мм.
Производительность определяется по формуле:
Q = F q к l m n o p ), где
Q - производительность по питанию, т/час;
q - удельная производительность на 1м2 сита, м3/час;
- насыпная плотность материала 2,55 т/м3.
к - коэффициент, учитывающий влияние мелочи;
l - коэффициент,учитывающий влияние крупных зерен ;
m - коэффициент,учитывающий эффективность грохочения;
n - коэффициент, учитывающий форму зерен материала ;
о - коэффициент,учитывающий влияние влажности;
р - коэффициент,учитывающий способ грохочения.
q = 25,5 м3/час на 1м2 сита; к = 2; l =0,97; m =1; n =1; о =0,85; р =1,3
Расчет потребности грохотов производим по сетке 16 мм:
n = 72,834:74 =0,97, принимаем 1 грохот.
2. Для второй стадии грохочения выбираем грохот ГИСТ-51. Размер отверстий сит: 20 мм.
Необходимое число грохотов:
n = 53,81:54,995=0,97, принимаем к установке 1 грохот.
Для остальных стадий по 1 грохоту ГИЛ-42 и ГИЛ-11 соответственно.
Выбор и расчет рентгенолюминесцентных сепараторов.
Исходя из практики для обогащения материала крупностью -50+20 мм выбираем рентгенолюминесцентные сепараторы ЛС-20-05-2М. Для каждого класса крупности сепараторы имеют свою производительность:
кл.-50+20 мм – до 50 т/час (optim –30 т/час);
Определяем количество сепараторов:
класс -50+20 мм:
Qисх= 1,64 т/час
n =Qисх:Qсеп= 1,64:30=0,05, принимаем к установке 3 аппарата, с учетом резерва.
Выбор и расчет винтовых сепараторов.
Перед процессом пневмофлотации и переделом ТСС материал предварительно обогащается на винтовых сепараторах. Выбираем хорошо зарекомендовавшие себя винтовые сепараторы – СВ3-1500.
Производительность сепаратора на 1 желоб -70 т/час.
Сепарация для класса –5+2 мм:
при исходной нагрузке 4,50 т/час, потребуется сепараторов:
n = 4,50 : 70 = 0,64, к установке принимаем 1 сепаратор СВ3-1500.
Выбор и расчет классификаторов.
Для обезвоживания продуктов обогащения успешно применяют спиральные классификаторы типа 1КСН-12,1КСН-5.
Для обесшламвливания выбираем классификатор 1КСН-5 с производительностью по пескам Qксн-5 =70 т/час. При исходной нагрузке на передел Qисх=32,65т/час потребуется классификаторов:
n = 32,65 : 70 =0,46, к установке принимаем 1 классификатора 1КСН-5, и один классификатор 1КСН-12 на классификацию
Выбор и расчет пневмофлотационых машин.
Институт “Якутнипроалмаз” разработал и внедрил на обогатительных фабриках АК “АЛРОСА” пневматические флотационные машины различных модификаций- ПФМ-5М, ПФМ-10М, ПФМ-12М. Перечисленные машины являются базовыми объектами технологии крупнозернистой флотации.
Для процесса флотации выбираем пневмофлотомашину ПФМ-5М.
Определяем необходимое количество машин по формуле:
n = Qисх: QПФМ-5М, где
Qисх - исходная нагрузка на передел флотации;
QПФМ-5М - производительность пневмофлотомашины ПФМ-10М,
Qисх=0,34 т/час;
QПФМ-5М= 50-120т/час (optim - 100т/час).
n = 0,34:100 = 0,034, к установке принимаем 1 машину ПФМ-10М.
Выбор и расчет валкового пресса
Для дробления куска материала +32 мм применяем валковый пресс объемного сжатия 45-4680-GR, производительностью до 80 т/час. Эти дробилки в основном использовались в качестве вторичных дробилок, поскольку они были существенно лучше конусных дробилок с точки зрения характеристик по высвобождению и обеспечению сохранности алмазов.
Нагрузка на данную стадию дробления составляет 58,48 т/час.
Необходимое количество дробилок будет равно:
n = Qр / Qп = 24,815/80 ≈ 1
Для второй стадии:
n=1,63/80 ≈ 1
К установке применяем 2 дробилки типа валковый валковый пресс объемного сжатия.
ВВЕДЕНИЕ. Алмаз («Адамас» - греч.) - твердый, несокрушимый, непреодолимый - один из самых необыкновенных и интересных материалов известной нам неорганической природы. Наиболее красивый из драгоценных камней и наиболее твердый из всех минералов, он широко распространяется в металлообрабатывающей промышленности, а некоторые разновидности его нашли применение в современной полупроводниковой технике. Кроме того, алмаз может служить ценнейшим средством наблюдения физико-химических процессов, происходивших некогда в недрах земной коры и недоступных для непосредственного изучения: благодаря устойчивой кристаллической решетке он дошел до поверхности несет информацию об этих процессах в почти неизмененном виде.
В настоящее время, несмотря на открытие новых месторождений и значительное увеличение добычи алмазов, цены на ювелирные алмазы продолжают возрастать.
В зависимости от качества и величины кристаллов цены на алмазы колеблются от нескольких долларов до нескольких тысяч долларов за 1 кар. Так, цены на самый дешевый сорт технических алмазов «крашинг борт», идущий на дробление и изготовление порошков составляет 2-8 долларов за 1 кар. Цены на технические алмазы средних сортов составляют 10-25 долларов за 1 кар. Стоимость высокосортных технических алмазов колеблется в пределах 45-55 долларов за 1 кар.
Качество добываемых алмазов в разных странах различное. Очень высокое качество отмечено в месторождении ЮАР - до 80 % добываемых кристаллов - ювелирные. В то же время в Заире, который добывает 50-60% всех алмазов, стоимость их составляет всего 15-17% от стоимости мировой добычи.
Центром добычи алмазов стали – Мирный, Айхал, Удачный. Алмазные фабрики и карьеры оборудованы современной техникой, шагающими экскаваторами, бесшаровыми мельницами, люминесцентными сепараторами.
Добыча алмазов из россыпей также имеет небольшой удельный вес в общей добыче, но за счет высокого содержания алмазов ювелирных сортов, разработка многолетних мерзлых алмазоносных россыпей, включая повторную отработку техногенных месторождений, является экономически эффективной.
АК «АЛРОСА» создана в соответствии с Указом Президента Российской Федерации «об образовании акционерной компании «Алмазы России – Саха» от 19 февраля 1992 года № 158С. 13 августа 1992 года была зарегистрирована. Начало свою работу АК «АЛРОСА» 1 января 1993 года.
Деятельность Компании регулируется Уставом «АЛРОСА», договорами об аренде с Республикой Саха (Якутия), законодательствами России и Республики Саха (Якутия), а так же соответствующими Указами Президента. Согласно соответствующим статьям устава Компании; «АЛРОСА» является компанией закрытого типа, т.е. её акции не образуются в фондовом рынке.
И, наконец, лучше всего характеризующая масштабы и направления деятельности компании, - в ближайшие пять лет российские алмазодобытчики инвестируют в основное – алмазодобывающее производство более 2,6 млрд. долл. США. ТНК «Де Бирс» участвует и контролирует добычу алмазов в ряде африканских стран – в Бостване, ЮАР, Намибии и т.д. «Де Бирс» через ЦСО контролирует подавляющее большинство продаж алмазного сырья на рынке поскольку через нее продаются алмазы и из истоков своих и других стран.