Скачать .docx |
Реферат: История цемента
История цемента. |
![]() ![]() ![]() ![]() ![]() ![]() |
Цемент начали производить в прошлом столетии. В начале 20-х годов XIX в. Е. Делиев получил обжиговое вяжущее из смеси извести с глиной и опубликовал результаты своей работы в книге, изданной в Москве в 1825 г. В 1856 г. был пущен первый в России завод портландцемента.
Цемент является одним из важнейших строительных материалов. Его применяют для изготовления бетонов, бетонных и железобетонных изделий, строительных растворов, асбестоцементных изделий. Изготовляют его на крупных механизированных и автоматизированных заводах.
Цемент - это собирательное название группы гидравлических вяжущих веществ, главной составной частью которых являются силикаты и алюминаты кальция, образовавшиеся при высокотемпературной обработке сырьевых материалов, доведенных до частичного или полного плавления.
В группу цемента входят все виды портландцемента, пуццоланового портландцемента, шлакопортландцемента, глиноземистый цемент, расширяющиеся цементы и некоторые другие.
Цемент каждого вида может при твердении развивать различную прочность, характеризуемую маркой. Марки цемента регламентированы строительными нормами и правилами (СНиП) и ГОСТом. Выпускают цементы преимущественно марок 200, 300, 400, 500 и 600 (по показателям испытания в пластичных растворах).
С повышением марки цемента эффективность его применения в бетонах часто возрастает за счет уменьшения удельного расхода вяжущего.
Из числа цементов разных видов наиболее важное значение имеет портландцемент.
Портландцемент не всегда удовлетворяет отдельным специальным требованиям, которые предъявляют к бетонам и строительным растворам при различных условиях их применения. Поэтому промышленность выпускает некоторые разновидности портландцемента: сульфатостойкий, с умеренной экзотермией, быстротвердеющий, гидрофобный, пластифицированный и некоторые другие цементы.
Сульфатостойкий портландцемент изготовляют из клинкера нормированного минералогического состава: в клинкере должно быть не более 5% трехкальциевого алюмината и не более 50% трехкальциевого силиката.
Низкое предельное содержание трехкальциевого алюмината требуется потому, что сульфатная коррозия развивается в результате взаимодействия сульфатов, находящихся в окружающей среде, с трехкальциевым гидроалюминатом цементного камня. Если в цементном камне С3А присутствует в малых количествах, то образуется незначительное количество гидросульфоалюмината кальция. Тогда он не опасен, так как распределяется в порах бетона, вытесняя оттуда воду или воздух, и внутренних напряжений в бетоне не вызывает. В небольших количествах гидросульфоалюминат кальция даже иногда полезен, так как уплотняет бетон.
В клинкере сульфатостойкого портландцемента ограничивается также содержание трехкальциевого силиката для уменьшения величины тепловыделения цемента. Поэтому сульфатостойкий портландцемент обладает повышенной сульфатостойкостью и пониженной экзотермией, т.е. качествами, необходимыми при изготовлении бетонов для отдельных зон гидротехнических и иных сооружений, работающих в условиях сульфатной агрессии. Сульфатостойкий портландцемент обычно выпускают двух марок - 300 и 400.
Портландцемент с умеренной экзотермией изготовляют из клинкера, который должен содержать не более 50% трехкальциевого силиката и не более 8% трехкальциевого алюмината. Такой цемент при умеренной экзотермии отличается также несколько повышенной сульфатостойкостью, поскольку в нем обычно содержится умеренное количество трехкальциевого алюмината.
Этот вид портландцемента применяют в гидротехническом строительстве в массивных бетонных конструкциях, подвергающихся частому попеременному замораживанию и оттаиванию в пресной или слабо минерализованной воде. Марка по прочности обычно 300 и 400.
Быстротвердеющий портландцемент содержит много трехкальциевого силиката и трехкальциевого алюмината и очень тонко измельчен. Поэтому такой цемент характеризуется интенсивным нарастанием прочности в первый период твердения - через 1 и 3 суток. Выпускается также особо быстротвердеющий цемент. Он показывает через трое суток прочность при сжатии 450- 500 кГ/кв. см (при испытании в жестких растворах).
Гидрофобный портландцемент изготовляют, вводя при помоле клинкера 0,1 - 0,2% мылонафта, асидола, окисленного петролатума, синтетических жирных кислот, их кубовых остатков и других гидрофобизующих поверхностно-активных добавок.
Эти вещества, адсорбируясь на частицах цемента, образуют тончайшую - в среднем мономолекулярную, т. е. толщиной в одну молекулу, оболочку. Но эта тончайшая оболочка придает цементу особые свойства. В этом сущность гидрофобизации цемента как метода, позволяющего в определенной степени управлять свойствами цемента в отношении действия воды на различных этапах его использования.
Как известно, взаимодействие цемента с водой есть двуединый противоречивый процесс. Сродство к воде органически присуще цементу, без этого свойства он не мог бы служить вяжущим веществом. Но вместе с тем на определенных стадиях применения цемента вода для него вредна. Так, при хранении и перевозках цемент портится от влаги, вода с содержащимися в ней примесями вызывает коррозию цементного камня и при частом попеременном замораживании и оттаивании цементных материалов разрушает их.
Задача преодоления противоречий, заложенных в самой природе цемента, в известной мере решается его гидрофобизацией.
Гидрофобный цемент при перевозках и хранении даже в очень влажных условиях не портится. Поверхностно-активные вещества, содержащиеся в нем, оказывают пластифицирующее действие на бетонные (растворные) смеси, а также уменьшают водопроницаемость и повышают коррозионную стойкость и морозостойкость бетона. Например, если обычный бетон выдерживает 300 циклов попеременного замораживания и оттаивания, то гидрофобизированный может выдержать 1000 и более циклов.
Марки гидрофобного цемента те же, что и портландского. Гидрофобный цемент был создан в СССР. На основе советского опыта было начато изготовление этого цемента и за границей (например, в Англии).
Пластифицированный портландцемент получают, вводя при помоле клинкера около 0,25% сульфитно-спиртовой барды (считая на сухое вещество) от веса цемента. Это поверхностно-активное вещество пластифицирует бетонные смеси, преимущественно жирные, позволяет снижать водоцементное отношение без ухудшения подвижности смесей и в ряде случаев дает возможность уменьшать расход цемента. Вместе с тем повышается морозостойкость отвердевшего бетона.
Белый портландцемент изготовляют из маложелезистого клинкера (серый цвет обычного цемента обусловлен главным образом наличием соединений железа в исходных сырьевых материалах).
Цветные цементы получают на основе белого портландцементного клинкера путем совместного помола с пигментами различных цветов, например с охрой, железным суриком, окисью хрома. Можно также получать цветные цементы смешиванием белого цемента с пигментами. Применение белого и цветных портландцементов, способствующее архитектурно-декоративному оформлению сооружений, имеет большое значение в индустриальной отделке крупноэлементных зданий. Эти цементы применяют также для цветных цементнобетонных дорожных покрытий, например на площадях у монументальных сооружений. Кроме перечисленных, имеются еще некоторые специальные сорта портландцемента, например тампонажный, для производства асбестоцементных изделий.
Цемент начали производить в прошлом столетии. В начале 20-х годов XIX в. Е. Делиев получил обжиговое вяжущее из смеси извести с глиной и опубликовал результаты своей работы в книге, изданной в Москве в 1825 г. В 1856 г. был пущен первый в России завод портландцемента.
Цемент является одним из важнейших строительных материалов. Его применяют для изготовления бетонов, бетонных и железобетонных изделий, строительных растворов, асбестоцементных изделий. Изготовляют его на крупных механизированных и автоматизированных заводах.
Цемент - это собирательное название группы гидравлических вяжущих веществ, главной составной частью которых являются силикаты и алюминаты кальция, образовавшиеся при высокотемпературной обработке сырьевых материалов, доведенных до частичного или полного плавления.
В группу цемента входят все виды портландцемента, пуццоланового портландцемента, шлакопортландцемента, глиноземистый цемент, расширяющиеся цементы и некоторые другие.
Цемент каждого вида может при твердении развивать различную прочность, характеризуемую маркой. Марки цемента регламентированы строительными нормами и правилами (СНиП) и ГОСТом. Выпускают цементы преимущественно марок 200, 300, 400, 500 и 600 (по показателям испытания в пластичных растворах).
С повышением марки цемента эффективность его применения в бетонах часто возрастает за счет уменьшения удельного расхода вяжущего.
Из числа цементов разных видов наиболее важное значение имеет портландцемент.
Портландцемент не всегда удовлетворяет отдельным специальным требованиям, которые предъявляют к бетонам и строительным растворам при различных условиях их применения. Поэтому промышленность выпускает некоторые разновидности портландцемента: сульфатостойкий, с умеренной экзотермией, быстротвердеющий, гидрофобный, пластифицированный и некоторые другие цементы.
Сульфатостойкий портландцемент изготовляют из клинкера нормированного минералогического состава: в клинкере должно быть не более 5% трехкальциевого алюмината и не более 50% трехкальциевого силиката.
Низкое предельное содержание трехкальциевого алюмината требуется потому, что сульфатная коррозия развивается в результате взаимодействия сульфатов, находящихся в окружающей среде, с трехкальциевым гидроалюминатом цементного камня. Если в цементном камне С3А присутствует в малых количествах, то образуется незначительное количество гидросульфоалюмината кальция. Тогда он не опасен, так как распределяется в порах бетона, вытесняя оттуда воду или воздух, и внутренних напряжений в бетоне не вызывает. В небольших количествах гидросульфоалюминат кальция даже иногда полезен, так как уплотняет бетон.
В клинкере сульфатостойкого портландцемента ограничивается также содержание трехкальциевого силиката для уменьшения величины тепловыделения цемента. Поэтому сульфатостойкий портландцемент обладает повышенной сульфатостойкостью и пониженной экзотермией, т.е. качествами, необходимыми при изготовлении бетонов для отдельных зон гидротехнических и иных сооружений, работающих в условиях сульфатной агрессии. Сульфатостойкий портландцемент обычно выпускают двух марок - 300 и 400.
Портландцемент с умеренной экзотермией изготовляют из клинкера, который должен содержать не более 50% трехкальциевого силиката и не более 8% трехкальциевого алюмината. Такой цемент при умеренной экзотермии отличается также несколько повышенной сульфатостойкостью, поскольку в нем обычно содержится умеренное количество трехкальциевого алюмината.
Этот вид портландцемента применяют в гидротехническом строительстве в массивных бетонных конструкциях, подвергающихся частому попеременному замораживанию и оттаиванию в пресной или слабо минерализованной воде. Марка по прочности обычно 300 и 400.
Быстротвердеющий портландцемент содержит много трехкальциевого силиката и трехкальциевого алюмината и очень тонко измельчен. Поэтому такой цемент характеризуется интенсивным нарастанием прочности в первый период твердения - через 1 и 3 суток. Выпускается также особо быстротвердеющий цемент. Он показывает через трое суток прочность при сжатии 450- 500 кГ/кв. см (при испытании в жестких растворах).
Гидрофобный портландцемент изготовляют, вводя при помоле клинкера 0,1 - 0,2% мылонафта, асидола, окисленного петролатума, синтетических жирных кислот, их кубовых остатков и других гидрофобизующих поверхностно-активных добавок.
Эти вещества, адсорбируясь на частицах цемента, образуют тончайшую - в среднем мономолекулярную, т. е. толщиной в одну молекулу, оболочку. Но эта тончайшая оболочка придает цементу особые свойства. В этом сущность гидрофобизации цемента как метода, позволяющего в определенной степени управлять свойствами цемента в отношении действия воды на различных этапах его использования.
Как известно, взаимодействие цемента с водой есть двуединый противоречивый процесс. Сродство к воде органически присуще цементу, без этого свойства он не мог бы служить вяжущим веществом. Но вместе с тем на определенных стадиях применения цемента вода для него вредна. Так, при хранении и перевозках цемент портится от влаги, вода с содержащимися в ней примесями вызывает коррозию цементного камня и при частом попеременном замораживании и оттаивании цементных материалов разрушает их.
Задача преодоления противоречий, заложенных в самой природе цемента, в известной мере решается его гидрофобизацией.
Гидрофобный цемент при перевозках и хранении даже в очень влажных условиях не портится. Поверхностно-активные вещества, содержащиеся в нем, оказывают пластифицирующее действие на бетонные (растворные) смеси, а также уменьшают водопроницаемость и повышают коррозионную стойкость и морозостойкость бетона. Например, если обычный бетон выдерживает 300 циклов попеременного замораживания и оттаивания, то гидрофобизированный может выдержать 1000 и более циклов.
Марки гидрофобного цемента те же, что и портландского. Гидрофобный цемент был создан в СССР. На основе советского опыта было начато изготовление этого цемента и за границей (например, в Англии).
Пластифицированный портландцемент получают, вводя при помоле клинкера около 0,25% сульфитно-спиртовой барды (считая на сухое вещество) от веса цемента. Это поверхностно-активное вещество пластифицирует бетонные смеси, преимущественно жирные, позволяет снижать водоцементное отношение без ухудшения подвижности смесей и в ряде случаев дает возможность уменьшать расход цемента. Вместе с тем повышается морозостойкость отвердевшего бетона.
Белый портландцемент изготовляют из маложелезистого клинкера (серый цвет обычного цемента обусловлен главным образом наличием соединений железа в исходных сырьевых материалах).
Цветные цементы получают на основе белого портландцементного клинкера путем совместного помола с пигментами различных цветов, например с охрой, железным суриком, окисью хрома. Можно также получать цветные цементы смешиванием белого цемента с пигментами. Применение белого и цветных портландцементов, способствующее архитектурно-декоративному оформлению сооружений, имеет большое значение в индустриальной отделке крупноэлементных зданий. Эти цементы применяют также для цветных цементнобетонных дорожных покрытий, например на площадях у монументальных сооружений. Кроме перечисленных, имеются еще некоторые специальные сорта портландцемента, например тампонажный, для производства асбестоцементных изделий.
Портландцемент |
Белый портландцемент |
Быстротвердеющий портландцемент |
Водонепроницаемый расширяющийся цемент |
Гидрофобный портландцемент |
Глинозёмистый цемент |
Карбонатный портландцемент |
Магнезиальный цемент |
Напрягающий цемент |
Песчанистый портландцемент |
Пластифицированный портландцемент |
Пуццолановый цемент |
Расширяющийся цемент |
Сульфатостойкий портландцемент |
Тампонажный цемент |
Шлаковый цемент |
Марки цемента, ГОСТы, основные отличия |
свойства цемента, определения ... |
технология производства цемента, схемы |
cухой способ производства цемента |
Сухой способ производства цемента
При сухом способе производства дробленые сырьевые материалы высушиваются и тонко измельчаются. Полученная сырьевая мука после корректирования и усреднения до заданного химического состава обжигается во вращающихся или шахтных печах. Схемы производства портландцемента по сухому способу производства в шахтных и вращающихся печах приведены ниже.
Схема производства портландцемента по сухому способу в механизированных шахтных печах

Схема производства портландцемента по сухому способу во вращающихся печах

При сухом способе производства цемента на обжиг клинкера расходуется от 750 до 1200 ккол/кг клинкера, при мокром способе производства—от 1200 до 1600 и выше ккал/кг клинкера, Сухой способ производства экономически целесообразен тогда, когда сырьевые материалы имеют низкую влажность и по возможности однородный химический состав, и в результате суммарный расход тепла на сушку сырьевых материалов и на обжиг клинкера ниже, чем расход тепла на обжиг этих материалов при мокром способе производства. Установлено, что экономически целесообразно применять сухой способ при влажности сырья до 12%.
мокрый способ производства цемента |
Мокрый способ производства цемента
При мокром способе производства твердые сырьевые материалы— известняк, мергель, глинистые сланцы — после их дробления тонко измельчаются в присутствии воды в мельницах и образуют сметанообразную массу — шлам. Мягкие сырьевые материалы — мел, глина и др. — после предварительного дробления полаются в болтушку, где при перемешивании с водой образуют однородный шлам. Меловой и глиняный шламы при необходимости тонко измельчаются в мельницах, поступают в бассейны, где корректируются и усредняются до заданного химического состава, и затем готовый шлам направляется для обжига в печь.
Схема производства портландцемента по мокрому способу во вращающихся печах
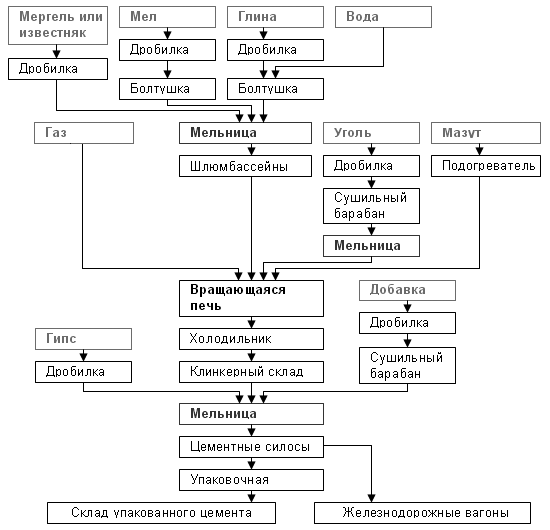
комбинированный способ производства цемента |
Комбинированный способ производства цемента
Комбинированный способ производства заключается в том, что сырьевые материалы перерабатываются мокрым способом в шлам и затем перед поступлением в печь обезвоживаются в шлам фильтрах до остаточной влажности 16—19%. Отфильтрованный «сухарь» смешивается с пылью, уловленной из печных газов, для того чтобы предотвратить слипание «сухаря». Смесь сухаря и пыли разрыхляют и подают с влажностью 12—13% в печь для обжига. К комбинированному способу производства относят также обжиг сырьевого шлама во вращающихся печах, оснащенных концентраторами. Шлам подсушивается в запечных концентраторах отходящими газами вращающихся печей до остаточной влажности 6—10% и затем поступает почти сухой в печь для обжига.
Схема производства портландцемента по комбинированному способу во вращающихся печах

Список цементных заводов |
ОАО "Ангарский цементно-горный комбинат" Местонахождение: г. Ангарск, Иркутской области. Год ввода в эксплуатацию: 1957 Мощность: 0,9 млн. тонн в год ООО "Атакайцемент" Местонахождение: Новороссийск, посёлок Гайдук, ул. Заводская, д.6 Год ввода в эксплуатацию:1913 Мощность: 0,6 млн. тонн в год ОАО "Ачинский глиноземный комбинат" Местонахождение: Красноярский край, г. Ачинск Год ввода в эксплуатацию: 1955 Мощность: 3,5 миллиона тонн в год ООО "Ачинский цемент" Местонахождение: Красноярский край., г. Ачинск Год ввода в эксплуатацию: 1965 Мощность: 3,5 миллиона тонн в год ЗАО "Белгородский цемент" Местонахождение: г. Белгород, ул. Сумская, площадка Цемзавода Год ввода в эксплуатацию: 1949 Мощность: 2,6 миллиона тонн в год ОАО "Верхнебаканский цементный завод" Местонахождение: г.Новороссийск, п. Верхнебаканский, ул. Орловская, строение 11 Год ввода в эксплуатацию:1965 Мощность: 0,3 млн. тонн в год ЗАО "ВолгаЦемент" Местонахождение: Саратовская обл., г. Вольск Год ввода в эксплуатацию: 1914 Мощность: 0.6 миллиона тонн в год ОАО "Вольскцемент" Местонахождение: Саратовская область г.Вольск-2 , ул. Цементников, 1 Год ввода в эксплуатацию: 1897 Мощность: 2,5 млн. тонн в год ООО "Воркутинский цементный завод" Местонахождение: Республика Коми, г. Воркута, поселок Цементнозаводской. Год ввода в эксплуатацию:1950 Мощность: 0,45 млн. тонн в год ОАО "Воскресенский Цементный Завод" Заводы - "Воскресенский цементный завод" и "Гигант" Местонахождение: Московская область, г. Воскресенск, ул. Коммуны, д.4 Год ввода в эксплуатацию:1949 Мощность: 1 млн. тонн в год ОАО "Горнозаводскцемент" Местонахождение: Пермская область, г. Горнозаводск Год ввода в эксплуатацию:1955 Мощность: 2,7 миллион тонн в год ОАО "Горно-металлургическая компания Норильский никель" Местонахождение: Красноярский край, г. Норильск, а/я 65. Год ввода в эксплуатацию: 1939 Мощность: 0,7 млн. тонн в год ЗАО "Жигулёвские Стройматериалы" Местонахождение: Самарская обл., г. Жигулевск-7. Год ввода в эксплуатацию: 1958 Мощность: 1,9 млн. тонн в год ОАО "Искитимцемент" Местонахождение: г. Искитим, ул. Заводская, 1а. Год ввода в эксплуатацию: 1934 Мощность: 2.6 млн. тонн в год ЗАО "Кавказцемент" Местонахождение: Карачаево-Черкесская Республика, г. Черкесск Год ввода в эксплуатацию: 1974 Мощность: 2,6 миллиона тонн цемента в год ОАО "Камчатцемент" Местонахождение: Камчатский край, Елизовский р-н, пос. Светлый Год ввода в эксплуатацию: 1975 Мощность: 0,35 миллиона тонн в год ЗАО "Катавский цемент" Местонахождение: Челябинская область, г. Катав-Ивановск Год ввода в эксплуатацию: 1914 Мощность: 1,5 миллиона тонн цемента в год ОАО "Колымацемент" Местонахождение: Магаданская обл., г. Магадан Год ввода в эксплуатацию: 1975 Мощность: 0,15 миллиона тонн в год ООО "Красноярский цемент" Местонахождение: г. Красноярск, Красноярский край. Год ввода в эксплуатацию: 1944 Мощность: 0,93 млн. тонн в год ООО "ПК Кузнецкий цементный завод" Местонахождение: Кемеровская обл., г. Новокузнецк, ул. Чайкиной, 15 Год ввода в эксплуатацию:1943 Мощность: 1,0 млн. тонн в год ЗАО "Липецкий цементный завод" Местонахождение: г. Липецк Год ввода в эксплуатацию: 1963 Мощность: 1,6 миллиона тонн в год ОАО "Магнитогорский цементно-огнеупорный завод" Местонахождение: Челябинская область, г. Магнитогорск, Белорецкое шоссе, 11. Год ввода в эксплуатацию:1950 Мощность: 1 млн. тонн в год ЗАО "Мальцовский портландцемент" Местонахождение: Брянская обл., г. Фокино Год ввода в эксплуатацию: 1899 Мощность: 4,0 миллиона тонн в год ОАО "Махачкалинский цементно-помольный производственный комбинат" Местонахождение: р. Дагестан, г. Махачкала Год ввода в эксплуатацию: 1996 Мощность: 0,9 миллиона тонн в год ЗАО "Михайловский цементный завод" Местонахождение: Рязанская обл., Михайловский район, п. Октябрьский Год ввода в эксплуатацию: 1963 Мощность: 1,8 миллиона тонн в год ОАО "Мордовцемент" (Староалексеевский и Алексеевский цемзаводы) Местонахождение: Республика Мордовия, Чамзинский район, посёлок Комсомольский. Год ввода в эксплуатацию:1956 Мощность: 3,45 млн. тонн в год ЗАО "Невьянский цементник" Местонахождение: Свердловская область, Невьянский район, пос. Цементный Год ввода в эксплуатацию: 1987 Мощность: 1,1 миллиона тонн цемента в год ОАО "Новоросцемент" Местонахождение: Краснодарский край, г. Новороссийск, Сухумское шоссе, д.60 Год ввода в эксплуатацию: 1882 Мощность: 4,0 млн. тонн в год ОАО "Новотроицкий цементный завод" Местонахождение: Оренбургская область, г. Новотроицк, ул. Заводская, д.3 Год ввода в эксплуатацию: Мощность: 1,2 млн. тонн в год ЗАО "Осколцемент" Местонахождение: Белгородская обл., г. Старый Оскол, площадка Цемзавода. Год ввода в эксплуатацию: 1969 Мощность: 3,7 миллиона тонн в год ОАО "Опытный цементный завод" Местонахождение: г. Санкт-Петербург Год ввода в эксплуатацию: 1961 Мощность: - ОАО "Пашийский цементно-металлургический завод" Местонахождение: Пермский край, Горнозаводский район, п. Пашия Год ввода в эксплуатацию: - Мощность: 0,25 миллиона тонн в год ЗАО "Пикалевский цемент" Местонахождение: Ленинградская область, г. Пикалёво. Год ввода в эксплуатацию: 1947 Мощность: 2,7 миллиона тонн в год ЗАО "Подгоренский цементник" Местонахождение: Воронежская область, пгт. Подгоренский, пос. Цемзавода Год ввода в эксплуатацию: 1932 Мощность: 800 тыс. тонн цемента в год, при условии выпуска цемента марки ШПЦ 300 ОАО "Подольский опытный цементный завод ЦЕМДЕКОР" Местонахождение: Московская область, г. Подольск, ул. Плещеевская, д.15 Год ввода в эксплуатацию: 1874 Мощность: 0,33 млн. тонн в год ЗАО "Савинский цементный завод" Местонахождение: пос. Савинский Архангельской обл. Год ввода в эксплуатацию: 1966 Мощность: 1,4 миллиона тонн цемента в год ОАО "Себряковцемент" Местонахождение: Волгоградская область, г. Михайловка, ул. Индустриальная, д. 2 Год ввода в эксплуатацию: 1953 Мощность: 2,4 млн. тонн в год ОАО "Сода" Местонахождение: Республика Башкортостан, г. Стерлитамак, ул. Бабушкина, д.7 Год ввода в эксплуатацию: 1952 Мощность: ОАО "Спасскцемент" Местонахождение: г. Приморский край, г. Спасск-Дальний Год ввода в эксплуатацию: 1907 (1976) Мощность: 3,1 млн. тонн в год ОАО "Сухоложскцемент" Местонахождение: Свердловская область, г. Сухой Лог, ул. Кунарская, д.20 Год ввода в эксплуатацию:1930 (1972) Мощность: 1,8 млн. тонн ГП "Сенгилеевский цемент" Местонахождение: Ульяновская обл., г. Сенгилей Год ввода в эксплуатацию: 1913 Мощность: 0,3 миллиона тонн в год ОАО "Теплозерский центный завод" Местонахождение: г. Еврейский автономный округ, Хабаровский край, г. Теплоозёрск. Год ввода в эксплуатацию:1949 Мощность: 0,8 млн. тонн в год ООО "Тимлюйский цементный завод" Местонахождение: пгт. Каменск, Республика Бурятия. Год ввода в эксплуатацию: 1948 Мощность: 0,66 млн. тонн в год ООО "Топкинский цемент" Местонахождение: г. Топки, Кемеровской области. Год ввода в эксплуатацию: 1966 Мощность: 3,0 млн. тонн в год ЗАО "Углегорск-цемент" Местонахождение: Ростовская область, Тацинский район, посёлок Углегорский Год ввода в эксплуатацию: 1986 Мощность: 80 тыс. тонн в год ОАО "Ульяновскцемент" Местонахождение: Ульяновская обл., г. Новоульяновск, Промплощадка Год ввода в эксплуатацию: 1961 Мощность: 2,4 млн. тонн в год ОАО "Уралцемент" Местонахождение: Челябинская область, г. Коркино, пос. Первомайский, ул. Заводская, д1. Год ввода в эксплуатацию:1957 Мощность: 2,3 млн. тонн в год ОАО "Цемент" Местонахождение: Алтайский край, Заринский район, станция Голуха Год ввода в эксплуатацию: Мощность: 0,45 млн. тонн в год ОАО "Цесла" (Сланцевский цементный завод) Местонахождение: Ленинградская область, г. Сланцы, Кингисеппское шоссе, д.1 Год ввода в эксплуатацию:1960 Мощность: 1,2 млн. тонн в год ОАО "Челябинский цементный завод" Местонахождение: Челябинская обл., г. Челябинск Год ввода в эксплуатацию: - Мощность: - ОАО "Щуровский цемент" Местонахождение: Московская обл., г. Коломна, ул. Цементников, д.1 Год ввода в эксплуатацию: 1870 Мощность: 1,3 млн. тонн в год ОАО "Якутцемент" Местонахождение: Республика Саха (Якутия), Хангаласский улус, посёлок Мохсоголлох. Год ввода в эксплуатацию: 1971 Мощность: 0,37 млн. тонн ОАО "Яшкинский завод строительных материалов" Местонахождение: Кемеровская область, Яшкино Год ввода в эксплуатацию: - Мощность: 0,4 миллиона тонн в год |
ГОСТ 24640-91. Добавки для цементов. Классификация
ГОСТ 24640-91
(СТ СЭВ 6824-89)
УДК 666.971.16.001.33:006.354 Группа Ж12
ГОСУДАРСТВЕННЫЙ СТАНДАРТ СОЮЗА ССР
ДОБАВКИ ДЛЯ ЦЕМЕНТОВ
Классификация
Additions for cements. Classification
ОКП 57 4325
Датавведения 01.07.91
Настоящий стандарт распространяется на все виды добавок, применяемых при изготовлении цемента, и устанавливает их классификацию.
Определения к терминам, применяемым в настоящем стандарте, - по СТ СЭВ 4772.
1. Добавки для цементов в зависимости от основного воздействия на свойства цемента или технологию его изготовления подразделяют на:
1) компоненты вещественного состава;
2) регулирующие свойства цемента;
3) технологические, облегчающие процесс помола цемента, но не оказывающие существенного влияния на его свойства.
2. Добавки-компоненты вещественного состава
2.1. Добавки-компоненты вещественного состава по роли в процессе гидратации и твердения цемента подразделяют на:
1) активные минеральные;
2) наполнители;
2.2. Активные минеральные добавки по роду активности подразделяют на:
1) обладающие гидравлическими свойствами;
2) обладающие пуццоланическими свойствами.
3. Добавки, регулирующие свойства цемента
3.1. Добавки, регулирующие свойства цемента, по характеру регулируемых свойств подразделяют на:
1) регулирующие основные строительно-технические свойства цемента;
2) регулирующие специальные свойства цементов.
3.2. Добавки, регулирующие основные строительно-технические свойства цемента, подразделяют на:
1) регуляторы сроков схватывания (ускорители и замедлители начала схватывания цемента);
2) ускорители твердения – повышающие начальную прочность цемента;
3) повышающие прочность – повышающие активность цемента в возрасте, установленном стандартами на продукцию для марочной прочности;
4) пластификаторы – снижающие водопотребность цемента.
3.3. Добавки, регулирующие специальные свойства цемента, подразделяют на:
1) водоудерживающие – повышающие седиментационную устойчивость цементного теста, снижающие водоотделение;
2) гидрофобизирующие – повышающие устойчивость цемента к воздействию влаги воздуха.
3) регулирующие объемные (линейные) деформации цементного камня (расширение или усадку цемента);
4) регулирующие тепловыделение – снижающие или повышающие теплоту гидратации за установленный срок;
5) улучшающие декоративные свойства цементов – повышающие белизну, а также придающие или улучшающие цвет;
6) регулирующие плотность цементного теста – утяжеляющие и облегчающие;
7) регулирующие тампонажно-технические свойства цемента.
ПРИЛОЖЕНИЕ
Справочное
КРИТЕРИИ ОЦЕНКИ СВОЙСТВ ДОБАВОК
Вид добавки | Основной эффект воздействия | Критерии | Метод испытания |
Компоненты вещественного состава | Экономия клинкера | Снижение доли клинкера больше, чем снижение активности цемента | Стандарты на методы испытаний цемента и добавок |
Технологические | Интенсификация процесса помола | Сокращение продолжительности помола цемента до заданной дисперсности не менее чем на 10% | ГОСТ 310.2 |
Регуляторы сроков схватывания | Ускорение или замедление схватывания | Изменение классификационного признака по ГОСТ 23464 | ГОСТ 310.3 |
Ускорители твердения | Повышение прочности в ранние сроки | Не менее 10 % в возрасте 1 или 3 сут | ГОСТ 310.4 |
Повышающие прочность | Повышение марочной прочности | По группам (ГОСТ 23464): высокопрочные – не менее 7 %; рядовые – не менее 10 % низкомарочные – не менее 15 % |
ГОСТ 310.4 |
Пластификаторы | Снижение водопотребности | Увеличение расплыва конуса не менее чем на 15 % или снижение нормальной густоты не менее чем на 3 % | ГОСТ 310.4 |
Водоудерживающие | Уменьшение водоотделения | Не менее 10 % относительных | ГОСТ 310.6 |
Гидрофобизаторы | Повышение сохранности цемента | Увеличение времени всасывания капли воды, нанесенной на поверхность цемента | - |
Регулирующие деформацию при твердении цементного камня | Снижение усадки или изменение расширения в заданных пределах | Изменение линейных деформаций не менее 50 % относительных | Любым методом с точностью до 0,1 мм/м |
Регулирующие тепловыделение | Снижение тепловыделения | Через 7 сут не менее 10 % | ГОСТ 310.5 |
Улучшающие декоративные свойства | Улучшение цвета, повышение белизны | Соответствие эталону цвета, повышение сортности | ГОСТ 15825, ГОСТ 965 |
Регулирующие плотность цементного теста и растворов тампонажных цементов | Облегчение, утяжеление | Изменение классификационного признака | ГОСТ 26798.1 |
ИНФОРМАЦИОННЫЕ ДАННЫЕ
1. РАЗРАБОТАН И ВНЕСЕН Государственной ассоциацией «Союзстройматериалов»
РАЗРАБОТЧИКИ
З. Б. Энтин, канд. техн. наук (руководитель темы); Н. В. Фартунина, канд. техн. наук; А. Б. Морозов
2. УТВЕРЖДЕН И ВВЕДЕН В ДЕЙСТВИЕ Постановлением Государственного строительного комитета СССР от 11.03.91 № 6
3. Стандарт полностью соответствует СТ СЭВ 6824-89
4. ВЗАМЕН ГОСТ 24640-81
5. ССЫЛОЧНЫЕ НОРМАТИВНО-ТЕХНИЧЕСКИЕ ДОКУМЕНТЫ
Цемент
[править]
Материал из Википедии — свободной энциклопедии
Цемент (в переводе с латинского «битый камень») — oдин из основных строительных материалов; гидравлическое минеральное вяжущее, приобретающее при затвердевании высокую прочность, также используемое при изготовлении бетона, вещество. Его называют гидравлическим, поскольку набор прочности и затвердевание происходит в присутствии воды; полученные из цементных минералов и воды твёрдые соединения водостойки, то есть нерастворимы в воде. Его называют минеральным, поскольку исходные материалы, используемые для его получения, — минеральной природы (горные породы или продукты их выветривания).
Цемент принципиально отличается от других минеральных вяжущих (гипса, воздушной и гидравлической извести), которые твердеют только на воздухе или, затвердев на воздухе, иногда продолжают твердеть во внешней среде.
Содержание· 1 Исторические сведения · 2 Изготовление · 3 Виды цемента · 4 См. также · 5 Источники · 6 Ссылки |
[править]Исторические сведения
Римляне подмешивали к извести определённые материалы для придания ей гидравлических свойств. Это были:
- пуццоланы (отложения вулканического пепла Везувия);
- дроблёные или измельчённые кирпичи;
- трасс, который они нашли в районе г. Эйфеля (затвердевшие отложения вулканического пепла).
Несмотря на различия, все эти материалы содержат в своем составе оксиды: диоксид кремния SiO2 (кварц или кремнекислота), оксид алюминия Al2 O3 (глинозём), оксид железа Fe2 O3 — и вызывают взаимодействие с ними извести; при этом происходит присоединение воды (гидратация) с образованием в первую очередь соединений с кремнезёмом. В результате кристаллизуются нерастворимые гидросиликаты кальция. В средние века было случайно обнаружено, что продукты обжига загрязнённых глиной известняков по водостойкости не уступают римским пуццолановым смесям и даже превосходят их.
После этого начался вековой период усиленного экспериментирования. При этом основное внимание было обращено на разработку специальных месторождений известняка и глины, на оптимальное соотношение этих компонентов и добавку новых. Только после 1844 года пришли к выводу, что, помимо точного соотношения компонентов сырьевой смеси, прежде всего необходима высокая температура обжига (порядка 1450° С) для достижения прочного соединения извести с оксидами. Эти три оксида после спекания с известью определяют гидравлические свойства, и их называют оксидами, обусловливающими гидравличность (факторами гидравличности).
[править]Изготовление
Для изготовления цемента сначала добывают известняк и глину из карьеров. Известняк (приблизительно 75 % количества) измельчают и тщательно перемешивают с глиной (примерно 25 % смеси). Дозировка исходных материалов является чрезвычайно трудным процессом, так как содержание извести должно отвечать заданному количеству с точностью до 0,1 %.
Эти соотношения определяются в специальной литературе понятиями «известковый», «кремнистый» и «глиноземистый» модули. Поскольку химический состав исходных сырьевых материалов вследствие зависимости от геологического происхождения постоянно колеблется, легко понять, как сложно поддерживать постоянство модулей. На современных цементных заводах хорошо зарекомендовало себя управление с помощью ЭВМ в комбинации с автоматическими методами анализа.
Правильно составленный шлам, подготовленный в зависимости от избранной технологии (сухой или мокрый метод), вводится во вращающуюся печь (длиной до 200 м и диаметром до 2—7 м) и обжигается при температуре около 1450 °C — так называемой температуре спекания. При этой температуре материал начинает оплавляться (спекаться), он покидает печь в виде более или менее крупных комьев клинкера (называемого иногда и портландцементным клинкером). Происходит обжиг.
В результате этих реакций образуются клинкерные материалы. После выхода из вращающейся печи клинкер попадает в охладитель, где происходит его резкое охлаждение от 1300 до 130 °С. После охлаждения клинкер измельчается с небольшой добавкой гипса (максимум 6 %). Размер зерен цемента лежит в пределах от 1 до 100 мкм. Его лучше иллюстрировать понятием «удельная поверхность». Если просуммировать площадь поверхности зёрен в одном грамме цемента, то в зависимости от толщины помола цемента получатся значения от 2000 до 5000 см² (0,2—0,5 м²). Преобладающая часть цемента в специальных емкостях перевозитсяавтомобильным или железнодорожным транспортом. Все перегрузки производятся пневматическим способом. Меньшая часть цементной продукции доставляется во влаго- и разрывостойких бумажных мешках. Хранится цемент на стройках в силосах(промышленное производство бетона), а также в биг-бегах или бумажных мешках.
[править]Виды цемента
По прочности цемент делится на марки, которые определяются главным образом пределом прочности при сжатии половинок образцов-призм размером 40*40*160 мм, изготовленных из раствора цемента состава 1 к 3 с кварцевым песком. Марки выражаются в числах 100—600 (как правило с шагом 100) обозначающим прочность при сжатии соответственно в 10-60 МПа. Цемент с маркой 600 благодаря своей прочности называется «Военным» и стоит заметно больше марки 500. Применяется для строительства военных объектов, таких как бункеры, ракетные шахты и т. д.
Также по прочности в настоящее время цемент делится на классы. Основное отличие классов от марок состоит в том, что прочность выводится не как средний показатель, а требует не менее 95 % обеспеченности (то есть из 100 образцов 95 должны соответствовать заявленному классу). Класс выражается в числах 30-60, которые обозначают прочность при сжатии (в МПа).
Портландцемент
Материал из Википедии — свободной энциклопедии
Портландцемент — вид цемента, наиболее широко применяемый во всех странах; название получил от г. Портленд (Portland) вАнглии. Основой портландцемента является силикат кальция, также известный как портландит.
Узнать данный вид цемента можно по внешнему виду - это зеленовато-серый порошок. Как и все цементы, если к нему добавить воду, он при высыхании принимает каменеобразное состояние и не имеет существенных отличий по своему составу и физико-химическим свойствам от обычного цемента.
Существуют следующие виды портландцемента:
- быстросохнущий;
- пластифицированный;
- гидрофобный;
- сульфатостойкий;
- дорожный;
- белый и цветной;
- с умеренной экзотермией;
- с поверхностноактивными органическими добавками.
Гидратация цемента
[править]
Материал из Википедии — свободной энциклопедии
Гидратация цемента — химическая реакция клинкерных составляющих цемента с водой (присоединение воды), причем образуются твердые новообразования (гидраты), которые заполняют первоначально залитый цементом и водой объём плотным наслоением гелевых частиц, вызывая тем самым упрочнение. Первоначально жидкий или пластичный, цементный клей превращается в результатегидратации в цементный камень. Первая стадия этого процесса называется загустеванием, или схватыванием, дальнейшая — упрочнением, или твердением.
Содержание· 1 Гидратация как пространственный процесс · 2 Гидратация как химический процесс · 3 Литература · 4 Ссылки |
[править]Гидратация как пространственный процесс
Цементные частицы в виде дробленых зерен окружены водой затворения, объём которой относительно велик (50—70 объёмных процентов). Этот объём заполняется новообразованиями, чтобы возникла прочная структура (цементный камень). Благодаря химическим реакциям с водой уже через несколько минут как на поверхности зерен, так и в воде возникают иглообразные кристаллы. Через 6 часов образуется уже так много кристаллов, что между цементными зернами возникают пространственные связи. Через 8—10 часов весь объём между постепенно уменьшающимися зернами цемента заполнен скелетом иглообразных кристаллов. Его также называют «алюминатной структурой», так как он возникает из 3CaO*Al2 O3 . Будучи до сих пор пластичной, масса начинает застывать, при этом происходит быстрое нарастание прочности. В оставшихся пустотах возникают одновременно (но поначалу не слишком интенсивно) продукты гидратации клинкерных минералов 2(3CaO*SiO2 ) и 2(2CaO*SiO2 ). Последние образуют гомогенный чрезвычайно тонкопористый ворс из малых кристаллов (так называемую "силикатную структуру"). Значение этой структуры вce более увеличивается. Она становится носителем прочности цементного камня и приблизительно через сутки начинает вытеснять алюминатную структуру. Через 28 суток (обычный срок испытания цемента и бетона) обнаруживается только силикатная структура.
Возникновение продуктов гидратации рассматривают как гелеобразование, а продукты гидратации — как гель. Скорость, с котором протекают эти процессы, зависит от:
- крупности цементных зерен (тонины помола цемента);
- минерального состава клинкера цемента;
- количества воды, которым замешивается цемент;
- температуры гидратации;
- введения добавок
Для полной гидратации цементного зерна необходимо присутствие 0,4-кратного (по массе) количества воды. Из неё только 60 % (то есть 0,25 массы цемента) связывается химически. Остальные 40 % исходной воды остаются слабо связанными в порах геля. Размер гелевых пор около 3-10 мм. Их образование неизбежно, именно они определяют тонко-пористое строение гелевой массы.
[править]Гидратация как химический процесс
Безводные минералы клинкера при реакции с водой превращаются в гидросиликаты, гидроаллюминаты и гидроферраты кальция.
3CaO*SiO2 +H2 O -> 3Ca2 SiO4 *H2 O+Ca(OH)2 +502 Дж / г
Ca2 SiO4 +H2 O -> Ca2 SiO4 *H2 O +206 Дж / г
3CaO*Al2 O3 +6H2 O -> 3CaO*Al2 O3 *6H2 O +867 Дж / г
Образовавшийся Ca(OH)2 под действием CO2 воздуха постепенно превращается в CaCO3 , гидроаллюминаты кальция с гипсом в присутствии воды дают двойные основные сульфаты, например Ca6 Al2 (OH)12 (SO4 )3 *26H2 O и Ca4 Al2 (OH)12 SO4 *6H2 O При получении бетона образовавшийся Ca(OH)2 с CO2 воздуха и SiO2 превращается в очень прочную массу, состоящую из карбонатов и силикатовкальция.
[править]Литература
Райхель В., Конрад Д. Бетон: В 2-х ч. Ч. 1. Свойства. Проектирование. Испытание. — М.: М.: Стройиздат, 1979. С. 33.Пер. с нем./Под ред. В. Б. Ратинова.
Террази́т — сухая, окрашеная смесь извести-пушонки, цемента (20—30 %), мраморной (каменной, гранитной) крошки, песка и минеральних красок. Иногда добавляется порошок слюды (для блеска).
Цвет и фактура терразита такая же, как у песчаника или туфа, но с блеском.
Разделяют по номерам или по буквам:
- № 1, или М (мелкозернистая), с зернами заполнителя величиной 1—2 мм
- № 2, или С (среднезернистая), с зернами заполнителя 2—4 мм
- № 3, или К (крупнозернистая), с зернами заполнителя 4—6 мм
После смачивания водой применяется для декоративных штукатурок.
Насосы для цемента
[править]
Материал из Википедии — свободной энциклопедии
Насосы для цемента — это группа специального строительного оборудования, которая обеспечивает перекачку и подачу сухих мелкодисперсных веществ, и прежде всего — цемента.
Содержание· 1 Использование · 2 Принцип действия · 3 Виды цементных насосов o 3.1 Пневмовинтовой насос o 3.2 Камерный насос типа Монжус o 3.3 Пневморазгрузчики o 3.4 Пневмоподъемники · 4 Стандарты · 5 См. также · 6 Производители · 7 Источники |
[править]Использование
Насосы для цемента используются для внутрипроизводственного транспорта цемента, сухих строительных смесей на бетонных заводах и узлах, складах цемента, погрузке и разгрузке специальных средств перевозки: железнодорожных бункерных вагонов-хопров, автомобильных цементовозов. Насосы различаются по конструкции, мощности и методу транспорта материала (инжекторные или струйные, всасывающие, всасывающее-нагнетательные, пневматические насосы).
[править]Принцип действия
Общий принцип действия насосов цемента — использование сжатого воздуха, за счёт которого осуществляется псевдоразжижение мелкодисперсного вещества и его подача в нужном направлении.
Максимальная длина подачи материала современными насосами составляет: по горизонтали — четыреста метров, по вертикали — пятьдесят метров.
[править]Виды цементных насосов
[править]Пневмовинтовой насос
Пневмовинтовой насос предназначен для транспорта цемента и других инертных материалов по трубопроводам. Данный тип насосов цемента обеспечивает бесперебойную подачу сыпучих веществ. Используют пневмовинтовые насосы для внутрипроизводственнго транспорта больших масс пылевидных сыпучих материалов (цемент, угольная пыль, порошкооборазные заполнители смесей) на заводах железобетонных изделий, растворобетонных узлах, строительных площадках. Пневмовинтовые насосы надежны в эксплуатации, что обеспечивает небольшой расход средств на техобслуживание.
Конструкция пневмовинтового насоса состоит из: приемной камеры, смесительной камеры с обратным грузовым клапаном, напорного быстроходного шнека с приводом от электродвигателя, броневой гильзы, коллектора для подвода сжатого воздуха. Подача цемента осуществляется при помощи винтов из камеры сжатым воздухом.
Из загрузочного бункера вяжущий материал под действием сил гравитации перемещается в приемную камеру насоса. Из приемной камеры материал подается быстровращающимся напорным шнеком в смесительную камеру, куда поступает через форсунки сжатый воздух. В смесительной камере материал разрыхляется и транспортируется в потоке сжатого воздуха по трубопроводу к месту назначения.
[править]Камерный насос типа Монжус
Камерный Монжус (от французского montejus) обеспечивает пневматический транспорт цемента, извести, гипса и других мелкодисперсных порошков минерального происхождения при выгрузке их из железнодорожных вагонов в силосы склада цемента, для выдачи цемента в бетонорастворные установки и для внутрискладских перекачек.
Действие насоса для цемента основано на вытеснении цемента энергией сжатого воздуха, подаваемого в камеру насоса под давлением. Преимуществом пневмокамерного насоса Монжус по сравнению с другими насосами для подачи и перекачки цемента является то, что в его системе отсутствуют движущиеся детали, которые находились бы в непосредственном контакте с подаваемым материалом. В других видах цементных насосов детали подвергаются большему износу и коррозии за счет контакта с транспортируемым материалом, что является основными причинами сбоя в работе насосов.
[править]Пневморазгрузчики
Пневморазгрузчики предназначены для разгрузки сыпучих материалов из ЖД вагонов — крытых, бункерных, а также хопров и других емкостей. Самовсасывающая пневмовинтовая конструкция данных рагрузчиков обладает высокой производительностью (значительная дальность подачи как по горизонтали, так и по вертикали). Пнвморазгрузчик состоит из следующих элементов: циклон, установленный на приемной горловине — в нем создается вакуум; заборное устройство — в нем происходит перемещение воздуха с частицами перекачиваемого материала в область пониженного давления (всасывание); нагнетательный пневмовинтовой насос — материал, попадая в него перекачивается потребителям.
[править]Пневмоподъемники
Предназначены для перемещения инертных материалов, в том числе и цемента по вертикальным трубопроводам с помощью сжатого воздуха. Пневмоподъемники сходны по своей конструкции с пневмонасосами, отличием является их большая мощность и производительность. Механизм действия — несамовсасывающий, материал самотеком подаётся в загрузочную горловину, перемещается винтовым транспортером (шнеком) в напорную камеру и под действием избыточного давления сжатого воздуха выдувается через напорный патрубок и поступает к месту приемки.
[править]Стандарты
![]() |
Этот раздел статьи ещё не написан . Согласно замыслу одного из участников Википедии, на этом месте должен располагатьсяспециальный раздел. |
[править]См. также
- Цемент
- Насос
[править]Производители
- Стройтехника
[править]Источники
- Дуда В. Цемент / Пер. с нем. Е. Ш. Фельдмана.- М.: Стройиздат, 1981. — 464 с.
- Борщевский, А. А. / — Механическое оборудование для производства строительных материалов и изделий: Учебник для вузов/Борщевский, А. А. , -Высш. школа, 1987. −367 c.
- Пневмотранспортное оборудование: Справочник / М. П. Калинушкин, М. А. Коппель, В. С. Серяков, М. М. Шапунов ; Под общ. ред. М. П. Калинушкина. — Л.: Машиностроение. Ленингр. отд-ние, 1986. — 286 с: ил.
- Бауман В. А. Механическое оборудование предприятий строительных ма-териалов, изделий и конструкций: Учебник для строительных вузов / В. А. Бауман, Б. В. Клушанцев, В. Д. Мартынов. — М.: Машиностроение, 1981. — 324 с.
- Перов В. А. Дробление, измельчение и грохочение полезных ископаемых / В. А. Перов, Е. Е. Андреев, Л. Ф. Биленко.- М.: Недра, 1990.- 301 с.
- Сапожников М. Я. Механическое оборудование предприятий строитель-ных материалов, изделий и конструкций.- М.: Высшая школа, 1971.-
382 с.
- Серго Е. Е. Дробление измельчение и грохочение полезных ископаемых.-М.: Недра, 1985.- 285 с.
- В. С. Богданов, И. А. Семикопенко, А. С. Ильин «Основные процессы в производстве строительных материалов» Белгород 2008 год. — 550 стр.
- В. С. Богданов, С. Б. Булгаков, А. С. Ильин, А. Ю. Крот «Технологические комплексы и механическое оборудование для предприятий строительной индустрии» 2008 год. — 528 стр.
- Проектирование цементных заводов. под редакцией к.т. н. Зозули П. В. и к.т. н. Никифорова Ю. В.
1994 год.
Объёмы производства цемента в России 2005—2009 года
В данном разделе представлены данные об объёмах цемента в России начиная с 2005 года. Источником служат данные Федеральной службы государтственной статистики РФ (Росстат).
Данные обновляются ежемесячно, 21 числа следующего месяца.
Производство цемента в РФ 2008—2009 года:
Всего, в 2008 году в России было произведено 53,41 млн. тонн цемента
Производство цемента в РФ 2007 год:
Всего, в 2007 году в России было произведено 59,6 млн. тонн цемента
Произвоство цемента в РФ 2006 год:
Всего, в 2006 году в России было произведено 48,18 млн. тонн цемента
Производство цемента в РФ 2005 год:
Всего, в 2005 году в России было произведено 44,95 млн. тонн цемента
Специальные цементы
Химический состав портландцементного клинкера
Фазовый состав портландцементного клинкера
Приготовление сырьевой шихты
Обжиг сырьевой шихты
Тонкое измельчение цемента
Химические реакции при твердении цементов
Механизм гидратации и твердения
Свойства цементов
Быстротвердеющие и особобыстротвердеющие высокопрочные портландцементы
Цементы с поверхностно-активными добавками
Пластифицирований портландцемент
Гидрофобный портландцемент
Коррозия портландцемента в растворах солей
Коррозия, вызываемая щелочами цемента
Сульфатостойкие портландцементы
Активные минеральные добавки
Пуццолановый портландцемент
Доменные шлаки
Шлакопортландцемент
Быстротвердеющий шлакопортландцемент
Сульфатно-шлаковый цемент
Известково-шлаковый цемент
Цементы в условиях темповлажностной обработки
Портландцементы для бетонных покрытий автомобильных дорог
Портландцемент для производства асбестоцементных изделий
Тампонажные цементы
Специальные тампонажные цементы
Белый портландцемент
Цветные портландцементы
Важнейшие свойства белого и цветных цементов
Цементы с инертными минеральными добавками (микронаполнителями)
Цементы для строительных растворов (кладочные цементы)
Цементы для защиты от радиационных излучений
Цементы для жаростойких бетонов
Гипсоцементнопуццолановые вяжущие вещества (ГЦПВ)
Белито-портландцемент (нефелиновый цемент)
Сланцезольный портландцемент
Магнезиальный портландцемент
Глиноземистый цемент
Строительно-технические свойства
Ангидрито-глиноземистый цемент (АГ-цемент)
Белито-глиноземистый цемент
Расширяющиеся цементы
Кислотоупорный кварцевый кремнефтористый цемент и его разновидности
Фосфатные цементы
Главная
История бетона
Состав бетона
Водонепроницаемый бетон
Монолитный бетон
Электропроводный бетон
Железобетон
Полимербетон
Добавки в бетон
Материалы для бетонной смеси
Специальные цементы
Заполнители бетона
Производство цем
ента
Разновидности портландцемента
Сырьевые материалы
. Основными видами сырья, применяемого для производства портландцементного клинкера, являются известковые, мергелистые и глинистые породы. Используются и другие виды природного сырья, а также искусственные материалы, являющиеся отходами (попутными продуктами) других отраслей промышленности. Это сырье может быть применено и при комплексном производстве портландцемента и других важных промышленных продуктов.
Для получения сырьевой шихты необходимого химического состава пригодны в небольшом количестве так называемые «корректирующие добавки», представляющие собой искусственные либо естественные материалы, используют и активные минеральные добавки, в том числе гранулированные доменные шлаки для получения портландцемента, пуццолановых и шлакопортландцементов.
Требования к составу и физической структуре сырьевых материалов могут быть примерно следующими. Карбонатный компонент должен быть сложен тонкодисперсным кальцитом; включения трудно измалываемого крупнокристаллического кальцита недопустимы из-за слабой его реакционной способности при обжиге цементного клинкера. Глинистый компонент также должен иметь равномерную структуру, не содержать включений крупных зерен кварца и других крупнообломочных пород, вызывающих затруднения при помоле и трудно осваиваемых при обжиге.
Для технологии производства весьма важно, чтобы при мокром способе производства необходимая текучесть сырьевой шихты (шлама) достигалась при возможно меньшем содержании воды, обычно в пределах 36—42%. Однако некоторые разновидности мела и в особенности мергелей вызывают существенное повышение влажности шлама до 50—52% из-за присутствия монтмориллонита, например, в амвросиевских мергелях.
Большое значение приобретает постоянство химического состава сырьевых материалов. Необходимо, чтобы сырьевая шихта, составляемая обычно из карбонатного и глинистого компонентов и корректирующей добавки, удовлетворяла принятым на данном заводе требованиям по значениям коэффициента насыщения кремнезема известью, силикатного и глиноземного модулей. Строго ограничивается содержание в шихте оксидов магния, фосфорного ангидрида, щелочей, серного ангидрида, диоксида титана, оксидов марганца и хрома. Содержание каждого из этих оксидов в установленном количестве оказывает положительное действие на процессы обжига клинкера. Наряду с основными видами сырья, такими как глины и известняки, большое значение приобретают доменные шлаки, представляющие собой силикаты и алюмоспликатные расплавы, получающиеся при выплавке чугуна в доменных печах; они обычно гранулируются путем быстрого охлаждения водой либо совместным действием воздуха и воды. Применение гранулированных доменных шлаков в качестве сырьевого компонента для получения клинкера возможно однако лишь при сухом способе производства, когда нет взаимодействия его с водой при помоле и хранении, вызывающего загустевание (схватывание) шлама. В состав сырьевой шихты вводят и электротермофосфорные шлаки. Они отличаются от обычных доменных шлаков содержанием до 3% фтора и 3% пентаксида фосфора, причем фосфор несколько ограничивает применение шлака в сырьевой смеси.
Нефелиновый (белитовый) шлам.
При комплексной переработке нефелинов, в результате которой выпускаются глинозем (перерабатываемый в дальнейшем в металлический алюминий), сода и другие виды щелочей, получается нефелиновый шлам, из которого и изготовляют портландцемент. Минерал нефелин представляет собой алюмосиликат натрия. Обычно он загрязнен примесями и содержит в избытке кремнекислоту. Нефелин получают в виде хвостов при обогащении апатитовых руд Хибинского месторождения (Кольский полуостров); эти хвосты, в свою очередь, обогащаются, причем выход нефелинового концентрата превышает 50%. Технология комплексной переработки нефелинового концентрата заключается в следующем. Концентрат в смеси с известняком обжигается во вращающихся печах при температуре около 1573 К, при этом получается спек, состоящий из двухкальциевого силиката и твердого его раствора (в количестве около 30%) и щелочных алюминатов. Спек подвергается выщелачиванию, щелочные растворы алюминатов отделяются от осадка, который после промывки представляет собой довольно грубую суспензию, называемую нефелиновым шламом.
Белитовый шлам транспортируется в цементный цех с влажностью 38—40%; содержащаяся в нем твердая фаза очень легко осаждается и способна схватываться, поэтому необходимо непрерывно его перемешивать с помощью сжатого воздуха и механических мешалок. Кроме этого, весьма нежелательно повышенное содержание в нем до 2,5% щелочей и из них до 1% —растворимых; для получения сырьевой шихты необходимого химического состава приходится для повышения содержания в клинкере глинозема добавлять боксит.
Сырьевая шихта для получения цементного клинкера содержит, примерно, (в расчете на сухое вещество) 41% белитового шлама, 53% известняка, 4,5% боксита и 1,5% железистых огарков. Влажность шихты понижена и составляет около 30%. Готовят ее по обычной схеме мокрым тонким измельчением указанных компонентов и после корректирования до заданного химического состава обжигают во вращающихся печах. При этом производительность печей повышается, примерно, на 30% и соответственно понижается удельный расход топлива на обжиг.
Исследования показали, что при приготовлении сырьевой шихты можно отказаться от применения дефицитного боксита путем введения в состав шихты 0,5% фтористого кальция — эффективного минерализатора обжига. Заводские опыты показали, что сырьевая шихта может состоять из 50% белитового шлама и, примерно, 50% известняка без добавок.
Для повышения силикатного модуля применяют трепел, опоку, маршалит, кварцевый песок и др. Увеличения глиноземного модуля достигают применением бокситов, зол некоторых видов твердого топлива и др.
Способы приготовления сырьевой шихты
. Добыча сырьевых компонентов на карьерах цементных заводов производится открытым способом. Твердые породы известняка дробятся в мощных стационарных и передвижных дробилках, мягкие — мел, глина, подвергаются предварительному измельчению в специальных агрегатах комбинированного дробления. При неоднородных физико-химических свойствах сырьевых компонентов необходимо обеспечить их усреднение и поточность процесса, для чего создаются специально оборудованные много-секционные склады, па которых складируют сырьевые компоненты по характерному качественному показателю. Усреднительные склады бывают разной мощности до 30 и более тыс. т. Ускоренные методы анализа сырья с применением автоматизации способствуют стабилизации качества сырьевой шихты. В цементной промышленности в основном применяют мокрый и сухой способы производства; небольшая доля приходится на комбинированный способ.
Мокрый способ.
При этом способе возможны различные схемы приготовления шихты в зависимости от физико-химических свойств сырьевых компонентов. Дробление известняка производится в две стадии с использованием для первичного дробления щековых или мощных конусных дробилок. Для мягких сырьевых компонентов применяют валковые дробилки разной конструкции, бесшаровые мельницы. Дозирование н смешение сырьевых компонентов осуществляют в сырьевых мельницах с сепарацией материалов в гидроциклонах и дуговых классификаторах.
Создаются необходимые запасы полученного шлама, содержащего примерно 36— 40% воды, который подвергается корректированию и усреднению пневматическим способом до достижения заданного химического состава.
Процесс измельчения в присутствии воды заметно облегчается в связи с тем, что вода, по П. А. Ребиндеру, является понизителем твердости и способствует ускорению процесса диспергирования твердых материалов.
Практическое значение приобрело применение добавок поверхностно-активных веществ, электролитов, либо их композиции для снижения влажности шлама при сохранении необходимой его текучести или вязкости. Снижение содержания воды в шламе на 1 % в пределах 35—40% приводит к повышению производительности вращающихся печей на 1—1,5% и снижению удельного расхода тепла примерно на 1%. Для этой цели применяют сульфитно-дрожжевую бражку, соду, щелочные вытяжки торфа либо бурого угля, разные виды фосфатов натрия и др. Для снижения влажности шлама на одном зарубежном заводе применяли вдувание отходящих, богатых содержанием углекислоты, газов вращающихся печей; значительную роль играло, по-видимому, наличие в этих газах не только С02, но и возогнапных щелочей.
По-видимому, процессы воздействия на структурно-механические свойства сырьевых шламов базируются на явлениях ионного обмена, которые характерны для глинистых минералов. Как известно, глинистые суспензии представляют собой по существу коллоидные системы; они способны к обменным реакциям, сорбции воды и характеризуются электрокинетическими явлениями. В коллоидной системе, состоящей из твердой фазы, взвешенной в жидкости, поверхностно-активные вещества адсорбируются преимущественно на поверхности отдельных частиц.
Полагают, что вокруг зерен известняка, либо мела, образуются структурированные диффузные оболочки из коллоидных глинистых частиц, которые прочно удерживаются силами адгезии на поверхности этих зерен. Диффузные оболочки коагуляционной структуры способны удерживать в своих ячейках значительное количество воды. Прочность и подвижность таких структур зависит от толщины глинистых прослоек в местах контактов, числа контактов в единице объема и физико-химических свойств глины. Так как эти явления проявляются у разных шламов в разной степени, в зависимости от физико-химических свойств составляющих их компонентов, удельной поверхности, химического состава воды и др., действие добавок-разжижптелей оказывается избирательным. Поэтому для каждого вида шлама приходится экспериментально подбирать наиболее эффективный разжижитель. Больше всего применяется добавка 0,3— 0,5% сульфитно-дрожжевой бражки, снижающая в некоторых шламах влажность на 3—4% (абсолютных).
Практическое значение начинают приобретать угле-щелочные и торфощелочные добавки, получаемые путем обработки бурого угля или торфа щелочью преимущественно в виде соды. Они могут снизить влажность мело-глиняного шлама на 6—7% (абсолютных). Эффективными оказались сульфатный шлам лигнина, водный нейтрализованный гудрон, триполифосфат, гексамета-фосфат и другие фосфорные соли натрия; их применение лимитируется однако сравнительной их дороговизной и необходимостью применять воду с (малым содержанием гипса и других солей в воде. Многие виды разжижителей обладают свойством повышать вязкость шлама через двое-трое суток хранения. Поэтому при подборе вида разжижителя особое внимание уделяется испытанию шлама, содержащего добавку, на длительность сохранения текучести.
Сложившееся у нас преобладание мокрого способа производства явилось следствием ряда технических и экономических факторов. Высокий расход топлива на обжиг клинкера окупается сравнительно высокой производительностью печных агрегатов, лучшей гомогенизацией сырьевой смеси, несомненным упрощением ее приготовления, сравнительной простотой технологии. Большое значение имеет возможность интенсификации процесса обжига за счет совершенствования тепло- и массообмена в зонах подогрева и дегидратации сырьевой шихты путем устройства различных теплообменных устройств, таких, как цепные завесы, теплообменники различной конструкции, фильтры-подогреватели и др.
Сухой способ.
Несмотря на многие достоинства мокрого способа и постоянно вносимые в него технические усовершенствования, он не может конкурировать с сухим. Решающим в новой технике обжига «линкера по сухому способу является сочетание вращающихся печей с циклонными теплообменниками и декарбонизаторами, что обеспечивает снижение удельного расхода тепла при обжиге «линкера на 40—50%. В условиях необходимости экономии топливно-энергетических ресурсов большое значение имеет ориентация нашей цементной промышленности на расширение сухого способа производства.
При сухом способе дробленые сырьевые материалы высушиваются и измельчаются в специальных помольных агрегатах; корректируют и усредняют полученную сырьевую муку до заданного химического состава перемешиванием в специальных силосах большой вместимости. Для этой цели, так же как и для транспортирования муки, применяют специальные пневматические винтовые или камерные насосы. Возможно совмещение процессов сушки сырьевой шихты с дроблением в ударных и других одно- и двухроторных дробилках с обогреванием горячими газами, благодаря чему значительно уменьшается нагрузка сырьевых мельниц. Примерный расход электроэнергии в таких дробилках составляет 2—4 кВт-ч/т.
В ряде европейских стран, в США и Японии для помола мягких видов сырья применяют валковые мельницы разной конструкции производительностью 300 т/ч и выше. Валковые мельницы по принципу действия аналогичны обычным бегунам, измельчение в которых происходит под действием собственной массы катков. Измельчение материала в такой мельнице осуществляется за счет его раздавливания между вогнутой поверхностью вращающейся опорной чаши и катящимися по ней преимущественно тремя валками. Валковые мельницы работают в замкнутом цикле с сепараторами, которые устанавливают вне корпуса мельницы или встраивают в верхнюю часть кожуха. В установках с валковыми мельницами благодаря высокой кратности циркуляции материала можно использовать в большом объеме отходящие печные газы и измельчать сырье влажностью до 8%. Для обработки сырья повышенной влажности устанавливают дополнительные топки. При применении этих мельниц можно исключить одну стадию дробления. Тонкость помола регулируется скоростью воздушного потока с помощью дымососа. Тонкий продукт, уносимый отходящим воздухом (газами), поступает в пылеосадитель.
По зарубежным данным одна четырехвалковая мельница благодаря различной частоте вращения каждой пары валков позволяет осуществлять в одном агрегате грубый и тонкий помол. При диаметре тарелки 4,6 м и массе двух пар валков 54 т частота ее вращения составляет 25,4 мин. Производительность мельницы 220 т/ч при тонкости помола, характеризуемой остатком на сите, 0,09 мм, и исходной влажности материала — 11,5%. Удельный расход электроэнергии, включая весь процесс от забора материала из штабеля до загрузки сырьевой муки в силос с учетом работы электрофильтра и других пылеосадителей, составляет 14,3 кВт-ч на Гт сырьевой муки. Сырьевая смесь в мельнице сушится за счет тепла отходящих печных газов. Работа мельницы автоматизирована.
Для предварительного измельчения и сушки сырьевых материалов применяют также барабанные мельницы самоизмельчения типа «Аэрофолл». На торцевых стенках мельницы расположены дефлекторы, ускоряющие измельчение и препятствующие агрегации продукта; через эти мельницы можно пропускать большое количество горячих газов, отходящих из других установок. Большую часть полезного объема мельницы занимает загруженный материал, в мельницу добавляют небольшое количество мелющих тел. Измельченный продукт выносится из мельницы в потоке газов и поступает в осадительную камеру, где улавливается и осаждается крупка; затем он направляется в два параллельных циклона, служащих для осаждения тонких фракций материала. Мельница «Аэрофолл» обладает высокой производительностью по помолу и сушке. Диаметр корпуса мельницы 6—9 м при отношении диаметра к длине от 3:1 до 4:1. Корпус мельницы вращается со скоростью, составляющей 85—90% от критической.
Комбинированный способ применяется для обезвоживания сырьевого шлама способом фильтрации. Осуществляется он в вакуум-фильтрах либо в фильтр-прессах до получения так называемых горжей с остаточной влажностью 18—20%. Дальнейшая обработка коржа для подготовки его к подаче во вращающуюся печь производится по разным схемам. При этом способе повышается производительность печи с заметным снижением удельного расхода тепла на обжиг клинкера.
Быстротвердеющие и особобыстротвердеющие высокопрочные портландцементы
Быстротвердеющие высокопрочные портландцементы характеризуются более интенсивным нарастанием прочности как в начальный, так и последующий периоды твердения.
Оптимальный фазовый состав и соответствующая высокоактивным цементам микроструктура клинкера зависят не только от правильности расчета сырьевых материалов, но и от всего комплекса производственных факторов, к которым относятся: а) тонкий помол и высокая гомогенность сырьевой смеси; б) сильный и равномерный обжиг клинкера; в) правильный подбор вида и зольности топлива; г) резкое охлаждение клинкера, начиная от 1523 К. Важным и обязательным условием является высокий технический уровень работы цементного завода и строгая система контроля технологических процессов производства. При выборе фазового состава клинкера учитывают, что наибольшей интенсивностью твердения при одинаковой тонкости помола обладают следующие минералы цементного клинкера (в трехсуточном возрасте): трехкальциевый алюминат — около 100% от 28-суточной прочности, четырехкальциевый алюмоферрит — 80, трехкальциевый силикат — 57 и двухкальциевый силикат — 14%. По абсолютной прочности, достигаемой через 1 — 3 сут, на первом месте находится трехкалышевый силикат. Интересно, что еще большая, чем у С3Б, прочность получена при твердении смеси, состоящей на 80—85% минерала C3S и 10—15% минерала С3А. При оптимальном соотношении C3S и С3А в цементном клинкере концентрация СаО и Аl203 в жидкой фазе цементноводной суспензии будет такой, при которой образуются кристаллогидраты типа гидросульфоалюминатов кальция относительно стабильного состава. Эти данные являются результатом лабораторных исследований синтетических минералов. Клинкерные фазы промышленной продукции, содержащие в виде твердых растворов различные примеси, отличаются от них. Но это обстоятельство не оказывает решающего влияния на порядок расположения клинкерных фаз по интенсивности их твердения. При подборе рационального фазового состава клинкера при производстве этих цементов приходится учитывать ряд факторов. Так, большое значение для активности клинкера (цемента) имеет его микрокристаллическая структура. Известно, что в процессе кристаллизации не образуются идеально-упорядоченные структуры, особенно у поликристаллических веществ; кристаллические решетки обычно имеют дефекты. Установлено, что между формой кристаллов алита в клинкере и качеством цемента есть непосредственная связь: цемент лучшего качества получается преимущественно при отчетливой правильной кристаллизации алита.
Упомянутые выше исследования показали, что при содержании в клинкере нежелательных с точки зрения влиянияна качество цемента щелочных оксидов, оксида магния выше 2—3%, повышенного содержания фосфатов и др. кристаллы алита приобретают неправильную форму. Они бывают окаймлены мельчайшими зернами двухкальциевого силиката вторичного происхождения, часто содержат включения мелких зерен периклаза и жидкой фазы. Кристаллы белитовой фазы при этом также имеют неправильную форму зерен с зазубренными краями. Реакционная способность алита зависит от состава примесей, содержащихся в нем в виде твердых растворов, от дефектов структуры, трещин и характера дисперсности, которые ускоряют его взаимодействие с водой.
Для клинкера некоторых заводов характерны две структурные разновидности. Первая — неравномерно зернистая с распределением алита и белита в виде чередующихся различных по размерам групповых скоплений. Минералом, характерным для этой структуры, является белит, причем она возникает преимущественно тогда, когда сырьевая шихта недостаточно тонко измельчена и содержит значительное количество крупных зерен кварца. Вторая структура равномерпозерниста, характеризуется отсутствием скоплений либо агрегатов. Силикаты кальция рассредоточены по всему шлифу. Встречается и клинкер с двумя этими структурами. На микроструктуру клинкера влияет таким образом равномерность состава и тонкость измельчения исходной сырьевой шихты, а также химико-минералогические особенности сырьевых компонентов, в том числе содержание щелочей. Поэтому при производстве особобыстротвердеющих и высокопрочных портландцементов большое внимание уделяется физико-химической характеристике исходных сырьевых компонентов.
Сырьевая шихта должна характеризоваться равномерным распределением кремнезема и минимальным содержанием нежелательных (вредных) примесей. Шихту следует исключительно тонко измельчить с тем, чтобы кремнезем, в особенности в виде кварца, был сосредоточен во фракциях с размером зерна менее 15 мкм. При контрольном просеве такой сырьевой шихты через сито № 02 навеска проходит полностью, а остаток на сите № 008 минимальный (2—3%).
Выше уже говорилось о том, что клинкер следует быстро обжигать и охлаждать. Быстрый обжиг способствует формированию кристаллов малых размеров в наиболее метастабильном состоянии при питании печи сырьевой шихтой с постоянными физико-химическими свойствами. Для получения быстротвердеющих и высокопрочных портландцементов клинкер целесообразно обжигать в коротких вращающихся печах; быстрый обжиг достигается и в современных длинных печах при работе на короткой зоне спекания, максимально приближенной к головке печи. Это дает возможность не только быстро обжигать, но и быстро охлаждать клинкер.
Как известно, сырьем для значительного числа цементных заводов служат мелко- и крупнокристаллические известняки, часто обогащенные кремнеземом в результате окремнения. Встречаются известняки, для которых характерна некоторая доломитизация. Глинистые сырьевые компоненты имеют часто весьма неблагоприятный состав, содержат много кварцевого песка, полевых шпатов и др. Исследования показали, что увеличение размера зерен кварца с 17 до 91 мкм в составе сырьевой смеси может значительно замедлить спекание. Предотвратить это можно соответствующим повышением температуры. Широкое применение должны найти рассмотренные выше минерализаторы обжига, а также легирующие добавки, которые существенно влияют на кристаллизацию алита и активность клинкера. Известно, что кристаллизация часто прерывается вследствие изменения степени химической насыщенности питательной среды. Если в момент такой остановки кристалл еще не сформировался, возможен обратный процесс — растворение (резорбция). Минерализаторы, по данным Н. В. Белова, блокируют эти кристаллы и предохраняют их от резорбции, чему способствует также быстрое охлаждение клинкера. При резком мгновенном охлаждении (замораживании) жидкая фаза полностью переходит в стекловидное состояние без какой-либо кристаллизации; содержание стекла теоретически может достигнуть 25%; практически оно составляет примерно 6—10% (а иногда и больше), поскольку клинкер обычно охлаждается со средней скоростью.
Стекловидная фаза клинкера не гомогенна по структуре. Резкое охлаждение клинкера, как показали наши исследования, значительно увеличивает содержание двухкальнисвого силиката в жидкой фазе примерно до 15%; остальное же количеетво двухкальциевого силиката фиксируется преимущественно в виде белита, переход его в гидравлически инертную модификацию предотвращается. При быстром охлаждении клинкер должен проходить интервал температур менее 1523 К с большой скоростью, разложения алита при этом не наблюдается.
В зависимости от значения глиноземного модуля различное количество клинкерной жидкости переходит в стекловидное состояние. При этом существенно снижается содержание С3А, что повышает сульфатостойкость цемента. Содержание периклаза в клинкере резко снижается, так как он частично растворяется в стекле, а оставшаяся его часть приобретает тонкокристаллическую структуру. Существенно уменьшается взаимодействие клинкерной жидкости с образовавшимися кристаллическими фазами, что задерживает рост кристаллов и способствует образованию мелкокристаллического элита. Все это вместе с наблюдаемым повышением тепловыделения при гидратации быстро охлажденного клинкера способствует ускорению твердения цемента.
В результате термического удара от резкого охлаждения клинкерные зерна приобретают макро- и микротрещины, которые облегчают процесс тонкого измельчения и способствует тем самым повышению активности получаемого цемента, так как в нем больше тонких фракций. Однако наличие стекла в клинкере несколько затрудняет процесс особо тонкого измельчения. Прочность цемента через сутки зависит от содержания зерен размером менее 3 мкм. Однако некоторые исследователи придают наибольшее значение размеру зерен менее 5 и 7 мкм. Желательный верхний предел размера зерен не более 30 мкм. Односуточная прочность портландцемента определяется содержанием зерен цемента размером менее 10 мкм, а трехсуточная — до 30 мкм. По процентному содержанию указанных фракций применительно к составу клинкера можно рассчитать примерно ожидаемую односуточную и трехсуточную прочность. При помоле цемента с интенсификато-ром триэтаноламином увеличивается содержание фракций цемента размером 10—30 мкм; при добавке же СДБ повышается содержание тонких фракций размером менее 10 мкм. Сочетание же этих добавок, применяемое на наших цементных .заводах, положительно влияет не только на повышение производительности мельниц. Оно способствует формированию наиболее благоприятного зернового состава получаемого цемента.
Как тонко следует измельчать цемент особобыстротвердеющий и высоких марок. Исследования В. Б. Ратинова, С. М. Рояка, А. Е. Шейкина свидетельствуют о том, что при сверхтонком измельчении возможно последующее падение прочности цемента вследствие перекристаллизации гидратных новообразований. Наблюдается также понижение сульфатостойкости и морозостойкости цемента, увеличение его водопотребности, усиление усадочных явлений и др. Опыт показывает, что нецелесообразно измельчать портландцемент до удельной поверхности более 6000 см2/г. Помимо этого, получить такую степень дисперсности в современных помольных агрегатах при работе даже в замкнутом цикле весьма затруднительно, поскольку их производительность существенно снижается.
Рациональная дисперсность портландцементов высоких марок и быстротвердеющих должна устанавливаться применительно к химико-минералогическому составу исходного клинкера в зависимости от марки цемента и требуемой прочности в начальный период твердения при замкнутом цикле помола. Стремясь к получению и особобыстротвердеющих, и высокомарочных цементов необходимой прочности, следует учитывать, что существует прямая связь между фазовым составом клинкера и необходимой дисперсностью цемента. При пониженном содержании в клинкере суммы активных минералов (C3S + С3А) требуется более тонкое измельчение портландцемента, чем при повышенном. Можно считать, что содержание фракций цемента размером меньше 30 мкм должно составлять не менее 65—75%, в зависимости от марки портландцемента оно может достигать и 80%. Исследования, проведенные НИИЦементом в лабораторных условиях и на некоторых заводах, позволили установить фазовый состав клинкера для получения высокопрочного и особобыстротвердеющего портландцемента марки 600 при условии, что в односуточном возрасте он должен иметь предел прочности при сжатии 20— 25 МПа и в трехсуточном — 40 МПа при удельной поверхности около 4500 см2/г. Он должен характеризоваться расчетным содержанием трехкальциевого силиката примерно 65—68% и трехкальциевого алюмината не более 8%. При весьма тонком измельчении содержание гипса в этих цементах желательно довести до 4% (в расчете на БОз). Добавка 5—8% трепела способствует равномерному росту прочности к 28-суточному возрасту, хотя при этом наблюдается тенденция к повышению нормальной густоты цементного теста, а возможно и к некоторому снижению односуточной прочности.
Особый интерес, например, приобретает портландцемент Белгородского завода, отличающийся высоким содержанием белита в тончайших фракциях менее 5 мкм и сосредоточением алита в средних фракциях. Это позволяет получать вяжущее марок 500 и выше при удельной поверхности 3000—3200 см2/г. Примечательно, что этот портландцемент отличается характерными для белита положительными свойствами — высокой пропариваемо-стыо и пониженной усадкой. Высокая дисперсность быстротвердеющих цементов и значительное содержание в них суммы активных минералов (C3S + C3A) значительно ускоряет формирование коагуляционной структуры и заметно сокращает индукционный период гидратации. Наблюдается тенденция к некоторому ускорению сроков схватывания при недостаточном содержании в цементе гипса; при этом следят за тем, чтобы не повышалась температура цемента в процессе его помола, так как может произойти так называемое «ложное схватывание» цемента.
Однако, несмотря па значительные научно-исследовательские работы и накопленный опыт, пока еще нет оснований рекомендовать единую, пригодную для всех цементных заводов, физико-химическую характеристику цемента марки 600. Особенности сырья и оборудования требуют уточнения исходных параметров для получения особобыстротвердеюших и высокопрочных цементов; могут встретиться некоторые затруднения при обжиге клинкера на твердом многозольном топливе, что должно учитываться при разработке технологии.
Из-за повышенного содержания тончайших фракций эти цементы отличаются сравнительно большей чувствительностью к перевозкам навалом и длительному хранению, чем обычный портландцемент. Их нужно повторно испытывать при храпении более 25 сут. На основе ОБТЦ можно получить бетонную смесь такой же подвижности как и на обычном портландцементе при несколько меньшем значении В/Ц, что объясняется высоким содержанием зерен цемента менее 5 мкм, быстро образующих заметное количество геля гидросиликатов кальция, играющего роль пластификатора. Эта способность цемента проявляется особенно заметно при повышенной жесткости бетонной смеси.
Результаты опытных работ и внедрений в строительство быстротвердеющих н высокопрочных портландце-ментов позволяют сделать следующие обобщения, характеризующие эффективность этих видов портландцемента. При обычной технологии приготовления на основе этих цементов получают бетон повышенных марок. В результате появляется возможность уменьшить размер строительных элементов и снизить массу конструкций при сокращении их стоимости; необходимое условие изготовления такого бетона — применение высококачественных заполнителей.
При сохранении высокой марки бетона достигается снижение удельного расхода цемента; так, например, при изготовлении бетонов марок 500—550 на ОБТЦ взамен применявшихся рацее рядовых портландцементов расход цемента снижается примерно на 15%. Это приводит к уменьшению усадочных явлений в конструкциях и относительному снижению тепловыделения.
Быстрое твердение при сокращенном режиме пропаривания позволяет снизить потери предварительного напряжения арматуры, которые весьма ощутимы при длительной тепловлажностной обработке; поскольку бетон имеет высокую начальную прочность, можно раньше передать на него усилия от натяжения арматуры, что повышает производительность. Особенно эффективно применение высокопрочных цементов и ОБТЦ в жестких бетонных смесях при значениях Ц/В = 2—3,5 для изготовления предварительно напряженных двухскатных и подкрановых балок, ферм и ряда других железобетонных конструкций. Опытное применение ОБТЦ позволило значительно увеличить оборачиваемость форм в производстве железобетонных шпал при сокращении расхода цемента до 20%.
Использование высокопрочных и особобыстротвердеющих портландцементов способствует дальнейшему повышению технического уровня заводов сборного железобетона и строительства в целом. Необходимо лишь рационально использовать свойства этих цементов.
Во фторсодержащих клинкерах полное усвоение извести при обжиге достигается при 1373—1673 К. В клинкере сохраняется около 50—70% фтора или 20—30% хлора от первоначально введенных количеств (15—25%). Клинкер содержит C3S, C2S, CnA7-CaF2, стекло и возможно С3А и СА. Полезна добавка 5—10% трепела. Цемент отличается быстрым схватыванием и через 6 ч твердения набирает прочность 14—20 МПа, через 28 сут до 40 МПа. С помощью специальных добавок, вводимых для замедления сроков схватывания, удается получить марку 600, но несколько снизив при этом прочность в первые часы твердения. Высокопрочные цементы получают при добавке кристаллизационных компонентов (крентов) для увеличения закономерных сростков в цементном камне, являющихся затравками для синтеза гидратных фаз. Эти добавки близки по составу к добавке САПС; они способствуют быстрому наступлению начала схватывания.
На основе опытной партии портландцемента с низкой водопотребностью были изготовлены бетоны марок 600—800 с В/Ц=0,27—0,29. Расход цемента составил 500—600 кг/м3. Бетонные смеси с таким В/Ц имеют хорошую удобоукладываемость: осадка конуса составляет 6—20 см, жесткость — 2—10 с. Подвижность бетонной смеси сохраняется в течение 1,0—1,5 ч. Пропаренные бетоны на этом цементе характеризуются стабильным ростом прочности при длительном твердении, низкой пористостью, высокой морозо- и сульфатостойкостью.
Химический состав портландцементного клинкера
Портландцементный клинкер является продуктом спекания при обжиге сырьевой шихты надлежащего состава, обеспечивающего преобладание в нем высоко-основных силикатов кальция. Физико-химической основой технологии производства являются термохимические реакции, при которых происходит химическое взаимодействие между известью и глинистыми минералами. В результате образуется клинкер, содержащий кальциевые соединения — трех- и двухкальциевые силикаты, алюминаты и алюмоферриты кальция. После охлаждения он тонко измельчается с небольшой добавкой гипса. При помоле специальных портландцементов в состав цементной шихты вводят дополнительные компоненты определенного состава.
B клинкере обычно содержатся примеси в виде щёлочей, оксидов титана, фосфора и др. Химический состав портландцементного клинкера характеризуется коэффициентом насыщения кремнезема известью (КН) и модулями, силикатным (п) и глиноземным (р), численное значение которых позволяет производственнику ориентироваться в особенностях технологии производства клинкера. Они определяют свойства, необходимые для получения специального портландцемента на его основе.Силикатный модуль обычно находится в пределах 1,7—3,5, а глиноземный — 1—3.
Результаты исследований, проводившихся в последние годы с помощью новейших физико-химических методов, позволили более ясно представить себе фазовый состав клинкера и создать базу для проектирования заданного состава клинкера при производстве специальных портландцементов.
Фазовый состав портландцементного клинкера
При рассмотрении фазового состава клинкера следует учитывать условия его формирования. При обжиге сырьевой шихты содержащиеся в ней примеси и зола топлива распределяются неравномерно, что обусловливает переменный состав образующихся клинкерных фаз. Для них характерно образование твердых растворов, способных размещать в своих кристаллических решетках вовлеченные примесные атомы при условиях компенсации их зарядов. Компонентами твердых растворов являются щелочи, оксиды магния, хрома, титана, фосфора и др. В процессе обжига происходит стабилизация моноклинного алита. Наибольшей способностью к вовлечению примесных атомов в решетках обладают алюминаты и алюмоферриты кальция; белиты (6%) и алиты (около 4,8%).
Признано называть клинкерные фазы по названию исходных минералов — фаза алита, фаза белита. Алит — фаза трехкальциевого силиката C3S. Одним из наиболее важных в химии цемента соединений извести с кремнеземом является трехкальциевый силикат C3S. Он устойчив в интервале температур от 1523 до 2343 К, при которых расплавляется с разложением (инконгруентно), на СаО и расплав; он может образовываться путем первичной кристаллизации из трех- или четырехкомпонентного расплава, содержащего алюминий и железо. В этом случае не удается получить чистые кристаллы C3S, ибо в их твердом растворе содержится небольшое количество алюминатов и ферритов кальция. С. М. Рояк и О. К. Алешина наблюдали образование C3S при 1273—1473 К в зоне твердофазовых реакций в виде слоя толщиной около 1 мкм вокруг зерен СаО и в количестве менее 1% массы материала. Этот слой служит затравкой для основной массы алита, кристаллизующейся в жидкой фазе при 1723 К. Известен способ получения C3S из извести и кремнекислоты в расплаве хлористого кальция; после охлаждения расплав обрабатывается спиртом и водяным паром при 873 К. C3S может образовываться путем твердофазовой реакции между кремнекислотой и известью при температурах 1723 — 1873 К; при 2073 К — реакция протекает с большей скоростью. Однако для осуществления этой реакции необходим многократный обжиг тонко измельченного промежуточного продукта. Только при этих условиях можно получить C3S, не содержащий свободной извести.
Структура алита сложена из тетраэдров (Si04) и отдельных ионов кислорода и кальция. Последние координированы между собой шестью кислородными ионами. Для этой структуры характерна нерегулярная координация ионов кальция и «пустот» между ними. Полагают, что такой координацией можно объяснить высокую энергию решетки трехкальциевого силиката. Алит в портландцементном клинкере рассматривали как трехкальциевый силикат, в котором два атома кремния замещены двумя атомами алюминия, а для компенсации заряда в промежутках располагается атом магния. Такое замещение происходит в каждых 18 молекулах C3S, что позволило предложить следующую формулу алита — C54Si6 AM. Предлагают также рассматривать формулу алита в виде C51Si6 AM. Однако получить синтетический алит этого состава не удалось, продукт обжига содержал обычно некоторое количество свободного оксида кальция. Это дало основание считать, что растворимость глинозема значительно меньше, чем полагали ранее.
Белит
— фаза двухкальциевого силиката (C2S) существует в четырех модификациях. При исследовании путем травления некоторыми реактивами полированных шлифов портландцементного клинкера в отраженном свете заметно как светлое, так и темное призматическое промежуточное вещество. Обе эти составляющие различаются по отражательной способности. Светлое промежуточное вещество, обладающее наибольшей отражательной способностью, представлено алюмоферритами кальция с высокими показателями преломления, а также сильно обогащенным железом стеклом. Темное призматическое промежуточное вещество с меньшей отражательной способностью представляет собой трехкальциевый алюминат и клинкерное стекло, которое из-за быстрого охлаждения не успело закристаллизоваться. Промежуточное вещество отчетливо проступает при протравливании поверхности полированного шлифа в течение 1 с при 20°С специальным раствором серной кислоты в этиловом спирте. При помощи других реактивов можно различить в нем железосодержащие фазы, включая обогащенное железом стекло, трехкальциевый алюминат и др.
Алюмоферриты кальция
. Кристаллы алюмоферритов кальция характеризуются призматической, либо округлой формой, они от желтовато-бурого до темно-бурого или даже черного цвета. Раньше считали, что химический состав алюмоферритпой фазы клинкера, названной по имени исследователя браунмиллеритом, C4AF.
Трехкальциевый алюминат
— темное промежуточное вещество, появляющееся в присутствии щелочей в призматической форме, а если их нет — в прямоугольной. Несмотря на наличие травителей определение содержания трехкальциевого алюмината в клинкере связано с трудностями. О. М. Астреева и Л. Я. Лопатникова разработали количественный иммерсионный метод определения С3А в клинкере с помощью прокрашивания. Особо тонко измельченный порошок клинкера прокрашивается специальным спиртовым раствором органического красителя «кислотного ярко-голубого». В результате интенсивно окрашиваются только кристаллы С3А, что дает возможность определить их содержание.
Трехкальциевый алюминат неустойчив. Он образует Ci2A7 в условиях обжига цементного клинкера при содержании в составе сырьевой смеси минерализатора — фтористого кальция, либо кремнефтористого натрия, кальция или магния, а также в присутствии минерализатора— сернокислого кальция. Кристаллическая структура С3А еще точно не определена. Предполагают, что в С3А ионы Аl+3 в центрах боковых сторон элементарного куба окружены в правильном порядке шестью ионами кислорода. Другие ионы Аl3+ в центрах граней охватывают плоское кольцо из четырех ионов кислорода. В структуре имеются два вида ионов Са2+: одни, расположенные в углах куба, правильно координированы шестью атомами кислорода, а другие, сгруппированные в небольшой куб внутри структуры, неправильно координированы девятью атомами кислорода. Для структуры в целом характерно наличие примесей в пустотах кристаллических решеток, имеющих размер около 1,7А. В промышленных клинкерах MgO содержится до 2,5% по массе, С3А растворяет до 9% Na2O; наблюдается также способность к растворению незначительных количеств Si02. Для С3А характерно отсутствие полиморфизма.
Пятикальциевый трехалюминат
. Это соединение в портландцементном клинкере в виде отдельной фазы не кристаллизуется. Оно растворяется в стекловидной фазе либо входит в состав алюмоферритов кальция. Установлено существование метастабильной фазы, которая присутствует в клинкере, полученном при исключительно быстром обжиге.
Стекловидная фаза
. При резком мгновенном охлаждении (замораживании) жидкой фазы клинкера теоретически возможное содержание стекла может достичь примерно 25%; практически же стекловидной фазы в клинкере значительно меньше, потому что в реальных условиях она охлаждается со средней скоростью. Стекловидная фаза образуется в результате неравновесных условий кристаллизации клинкерного расплава при охлаждении.
Присутствие стекловидной фазы можно установить, сопоставив теплоту растворения исследуемого клинкера с аналогичной характеристикой полностью закристаллизованного (отожженного) клинкера, а также под микроскопом при исследовании в иммерсионных жидкостях. Обломки стекла в одном и том же образце клинкера могут иметь различное светопреломление. Это объясняется микроскопической гетерогенностью структуры и неспособностью жидкой фазы достигнуть во время охлаждения равновесия с крупными кристаллами затвердевших фаз.
В полированных шлифах отражательная способность также меняется в зависимости от значения глиноземного модуля. Для того, чтобы отличить стекло от кристаллического темного промежуточного вещества, рекомендуется протравливать поверхность шлифа клинкера раствором едкого калия. Резкое охлаждение клинкера, способствующее образованию стекловидной фазы, создает вместе с тем в ней внутренние напряжения, что является причиной рассыпания клинкера в процессе последующего хранения, однако оно благоприятствует сохранению прочности цемента при его вылеживании. Прочие составляющие клинкера. Свободный (несвязанный) оксид кальция практически всегда содержится в клинкерах в количестве, обычно не превышающем 0,75—1%. Это свидетельствует о неполноте реакций образования силикатов кальция. Свободный оксид кальция в клинкере представлен в виде скоплений или отдельных округлых зерен, часто примерно одинакового с белитом размера; его трудно обнаружить в прозрачном шлифе клинкера, но он хорошо виден в полированном шлифе, так как благодаря округлой форме заметно выделяется на поверхности шлифа. Содержание свободного оксида кальция может быть определено глицератным методом; он очень легко обнаруживается при образовании хорошо видимых фенолятов кальция. Количество оксида магния частично в виде периклаза в клинкере составляет 1—4% в зависимости от его содержания в исходных сырьевых материалах, главным образом в известняковом компоненте. Теоретическая температура диссоциации углекислого магния при давлении 0,1 МПа составляет 913 К. Оксид магния в зависимости от температуры его получения имеет различную плотность. При обжиге при 1673 К и выше получается неактивная MgO, называемая периклазом, ее плотность 3,58 г/см3; низкотемпературный оксид магния (каустический) имеет плотность 3,3 г/см3. Количество кристаллического оксида магния в клинкере всегда меньше расчетного его содержания, так как MgO распределена в цементном клинкере в виде твердого раствора и входит в состав алюмоферритов кальция\ алита, белита, стекловидной фазы, а также нередко и V трехкальциевый алюминат. Остающийся несвязанным оксид магния является периклазом, содержание которого зависит от количества и состава жидкой фазы, режима обжига и скорости охлаждения клинкера. Размер кристаллов периклаза в быстро охлажденных клинкерах со значительным содержанием стекловидной фазы меньше, чем в тех же клинкерах, но медленно охлажденных, т. е. близких к равновесной кристаллизации. Объясняется это тем, что растворимость оксида магния в стекле больше, чем в кристаллических алюмоферритах. В полированных шлифах клинкера обычно применяемые травители на периклаз не действуют, он отчетливо наблюдается в виде светлых угловатых зерен, возвышающихся над поверхностью. Обычно зерна имеют вид прямоугольников или треугольников.
Щелочи
. Содержание щелочей в Клинкере составляет обычно 0,3—1 % и в отдельных случаях достигает 1,5%; количество щелочей зависит от их содержания в исходных сырьевых материалах, а также от условий возгонки в процессе обжига. Подача в печь уловленной электрофильтрами пыли приводит к повышению содержания щелочей в клинкере. Обычно в пыли преобладает оксид калия, оксида натрия содержится, как правило, меньше.
Систематические исследования клинкерных систем, содержащих наряду с основными компонентами щелочные оксиды, показали, что эти оксиды прежде всего связывают серный ангидрид. При этом образуются щелочные сульфаты; возможно появление щелочно-сульфатной фазы, содержащей оба щелочные оксида.
Весьма существенно влияют щелочи на образование трехкальциевого силиката. Обычно при заметном количестве калия наблюдается избыток свободного оксида кальция.
Оксиды марганца
присутствуют в клинкере, если в качестве сырьевого компонента используют доменный шлак, содержащий обычно соединения марганца. Содержание Мп203 может достигнуть 3%; в этом случае цемент будет коричневым. Установлено, что Мп203 может замещать в клинкере Fe203. Исследования В. В. Тимашева показали благоприятное действие Мп на спекание клинкера. Клинкер из сырьевой смеси, в составе которой есть соединения марганца, нужно обжигать в окислительной среде.
Диоксид титана
переходит в клинкер обычно из глинистого компонента; содержание его составляет около 1%.
Пентаксид фосфора (фосфорный ангидрид)
содержится в клинкере, полученном из обычного цементного сырья в весьма незначительных количествах (порядка 0,2—0,3%), которые ускоряют процесс твердения портландцемента. Опыт работы некоторых цементных заводов показал, что при попадании в состав сырьевой смеси оксидов фосфора резко понижалась прочность цемента. Часто было трудно установить причину существенного снижения гидравлической активности, так как при обычном химическом анализе оксид фосфора осаждается с полуторными оксидами и тем самым меняет химическую характеристику состава клинкера. Однако при более детальном анализе удавалось обнаружить заметное (около 2%) количество Р205 в клинкере.
Было выявлено, что алит, вторично обожженный в присутствии фосфата кальция, разлагается на двухкальциевый силикат, в твердом растворе которого содержится фосфат кальция и свободный оксид кальция.
Сернистые соединения
обычно содержатся в глинистом компоненте цементной сырьевой шихты и, особенно, в том случае, если сырьевым компонентом является доменный шлак. Количество серы в пересчете на серный ангидрид (S03) не превышает обычно 0,75— 1%. В исходном сырье сера встречается как пирит, реже в виде сульфатов или органических соединений. Она может поступать в обжигаемую шихту с твердым топливом, либо сернистым мазутом. В процессе обжига, который, как правило, всегда является окислительным, сульфиды окисляются и вступают в реакцию со щелочами, образуя сульфаты щелочей и некоторое количество сульфата кальция. При высоких температурах Сульфат кальция может разлагаться, однако появляющийся серный ангидрид взаимодействует с обжигаемой высокоизвестковой шихтой и вновь образует сульфаты. Поэтому в отходящих газах вращающихся печей количество серного ангидрида обычно незначительно; в улавливаемой из отходящих газов пыли содержатся, как правило, сернокислые соединения. Таким образом, в цементном клинкере имеется алит, основой которого является C3S; двухкальциевый силикат — основа белита; трехкальциевый алюминат и четырехкальциевый алюмоферрит, образующие промежуточное вещество и в том числе стекловидную фазу. Присутствуют диоксид титана в виде твердого раствора в трехкальциевом силикате; оксид магния в виде периклаза, а также в составе твердого раствора в алите, белите, алюмоферрите и трехкальциевом алюминате (кроме того, он входит в состав стекловидной фазы), серный ангидрид в виде сульфатов щелочных металлов, а также сернокислого кальция; щелочи в виде новообразований, являющихся продуктами взаимонесвязанный — не вступавший в реакцию, так называемый свободный оксид кальция; примеси фосфорного ангидрида в составе белита и, возможно, алита; оксиды марганца преимущественно в составе алюмоферритов; оксиды хрома в составе силикатов кальция; нерастворимый (в кислоте) остаток, содержащий преимущественно не вступавший в реакцию кремнезем; возможны примеси фтора и хлора.
Минералогический состав клинкеров для производства специальных портландцементов устанавливается в зависимости от профилирующих свойств, которыми должен обладать данный цемент. Для сравнительной оценки минералогического (фазового)состава клинкера были предложены эмпирические модули — силикатный и глиноземный. Одним из таких показателей является также коэффициент насыщения кремнезема известью. Для расчета сырьевой шихты на цементных заводах задаются значением КН, а также одного из модулей — силикатного либо глиноземного. КН определяют в зависимости от совокупности ряда факторов — физико-химических свойств сырья, условий его переработки и обжига клинкера и, главным образом, в зависимости от специального назначения портландцемента, который будет изготовлен ИЗ этого клинкера.
С повышением КН увеличивается при соответствующем обжиге содержание алита в клинкере. При высоком численном значении КН, в равной степени как и при высоком значении силикатного модуля, затруднен процесс обжига; чтобы обеспечить полноту реакции образования алита, необходима повышенная температура обжига. Практически удается этого достигнуть не всегда, в клинкере остается повышенное (>1%) содержание свободной извести, соответственно увеличивается количество белита. При высоком значении глиноземного модуля, при прочих одинаковых характеристиках сырьевой шихты, также затруднен процесс обжига клинкера из-за повышенной вязкости жидкой фазы, что замедляет формирование трехкальциевого силиката. Понижение силикатного, а также глиноземного модуля делает обжигаемый клинкер относительно легкоспекаемым и легкоплавким, что может затруднить обжиг. Могут образоваться свары, комья обжигаемого клинкера и настыли на футеровке в зоне спекания.
При расчете сырьевой шихты для производства специальных портландцементов обычно учитывают весь комплекс изложенных обстоятельств и пользуются следующей несколько упрощенной формулой КН, поскольку не всегда можно точно предусмотреть количество свободной извести, которое окажется в клинкере, а также содержание серного ангидрида (S03), так как частично он может улетучиваться с отходящими из печи газами.
Свойства цементов
Нормальная густота
. В отличие от других строительных материаловцемент испытывают в гидратиро-ванном состоянии в виде теста либо песчаного раствора. Поэтому на результаты испытаний влияют не только физико-химическая характеристика вяжущего, но также содержание и особенности всех применяемых при испытании материалов: воды, песка, специальных добавок. Кроме того, большое значение имеют способы приготовления цементного теста либо раствора и условия, в которых протекают процессы твердения. Большое внимание необходимо уделять подбору количества воды для затворения цемента.
При испытании по ГОСТ определяют нормальную густоту цемента, измеряя глубину погружения стандартного пестика. Нормальная густота цементного теста характеризует количество воды затворения в % массы цемента и составляет для портландцемента примерно 22—28%. Она зависит от химико-минералогического состава клинкера, удельной поверхности цемента, содержания в нем допускаемой ГОСТ добавки трепела либо доменного шлака до 20% и некоторых других факторов. Сроки схватывания и равномерность изменения объема определяют в цементном тесте нормальной густоты.
Скорость схватывания
. Портландцемент, затворенный количеством воды, установленным при определении его нормальной густоты, образует подвижное пластичное тесто, которое в зависимости от химико-минералогической характеристики клинкера, удельной поверхности и вещественного состава цемента постепенно в течение нескольких часов теряет подвижность, превращаясь в плотное тело.
Во время перемешивания теста контакты, возникшие между гидрат-ными новообразованиями коллоидных фракций цемента, нарушаются, и тесто сохраняет подвижность несмотря на постепенное нарастание связности. Чем дольше длится гидратация, тем больше становится гидратных новообразований и выше плотность структуры.
Время, в течение которого образуется непрерывно уплотняющаяся и коагуляционная структура, является периодом схватывания, т. е. формирования структуры. Таким образом, схватывание цемента следует рассматривать как первоначальную стадию общего процесса твердения. По ГОСТ начало схватывания должно наступать не ранее 45 мни н заканчиваться не позднее 12 ч с момента затворения. Нормальные сроки схватывания портландцемента достигаются при совместном помоле клинкера с добавкой подобранного количествагипса, при котором содержание S03 в цементе должно быть не меньше 1,5%и не выше 3,5%. При большей добавке гипса возможно ускорение схватывания.
Замедление схватывания цемента наступает вследствие того, что на поверхности цементных зерен откладываются тончайшие пленки геля гидросульфоалюмината кальция, быстро образующегося в результате взаимодействия сульфата кальция с трехкальциевым алюминатом. Эти гелевые пленки сдерживают диффузию воды к цементному зерну, что снижает скорость гидратации Вследствие исключительно высокой дисперсности образующегося геля гидросульфоалюмината кальция его трудно обнаружить под микроскопом. Замедлителями могут быть также полуводный гипс и безводный сульфат кальция (ангидрит); эффективность их действия связана с разной степенью растворимости. При использовании природного ангидрита образование в уже полностью затвердевшем цементе гидросульфоалюмината кальция вследствие запоздалой (медленной) растворимости ангидрита может привести к возникновению весьма опасных напряжений в цементном камне, так как увеличивается объем кристаллизующегося гидросульфоалюмината кальция. При избыточном содержании гипса также возможно появление опасных напряжений в хорошо затвердевшем цементе вследствие продолжающейся реакции образования гидросульфоалюмината кальция.
Большое значение при выборе добавки гипса имеет удельная поверхность и зерновой состав цемента, причем в цементы с повышенным содержанием щелочей следует вводить относительно больше добавки. У средне- и высокоалюминатных цементов несколько большая добавка гипса вызывает повышение прочности в первые дни твердения и уменьшение усадки и расширения. Характерно, что добавка гипса может даже ускорить схватывание низкоалюминатных, богатых алюмоферритами кальция цементов, причем в этом случае не наблюдается тенденция к повышению первоначальной прочности и к уменьшению объемных изменений. Оптимальная добавка гипса для каждого цемента может быть установлена только на основе данных экспериментальных помолов цементов в заводских помольных агрегатах с характерной для них системой аспирации, температурами измалываемого цемента, его гранулометрическим составом и др.
Ложное схватывание. Иногда происходит так называемое ложное схватывание цемента, характеризующееся тем, что цементное тесто схватывается преждевременно с большим выделением тепла. Однако при дальнейшем перемешивании тесто разжижается и схватывается уже нормально. Такое явление объясняют тем, что при помоле горячего клинкера, особенно в мельницах открытого цикла, температура цемента повышается иногда до 150°С и выше. Это вызывает дегидратацию гипса с образованием не только полугидрата, но и полностью обезвоженного сульфата кальция — ангидрита в растворимой форме. Быстрая гидратация ангидрита и полуводного гипса сопровождается преждевременным загустеванием цементного теста, которое при дальнейшем перемешивании разжижается.
Ложное схватывание цемента может вызвать быструю потерю пластичности бетонной смеси во время перемешивания либо перевозки к месту потребления. Его можно предупредить глубоким охлаждением клинкера, помолом его, преимущественно в сепараторных мельницах, либо охлаждением корпуса мельниц открытого цикла, сильной аспирацией, а также подачей распыленной водновоздушной смеси в последнюю камеру мельницы.
Испытание цемента на ложное схватывание заключается в видоизменении стандартного определения нормальной густоты цементного теста с повторением испытания через короткие интервалы — 3—5 мин с промежуточным перемешиванием. На скорость ложного схватывания бетонной смеси влияют температура, условия и время перемешивания, вид заполнителя и др. Возможна локализация явлений ложного схватывания цемента путем введения небольшой добавки СДБ, гипса либо минерального масла. Однако не у всех цементов даже при высокой температуре их измельчения наступает ложное схватывание. Полагают, что оно может быть вызвано наличием большого количества свободной извести либо недожога в измалываемой шихте клинкера. При затвореиии цемента с высокой удельной поверхностью часто образуются уплотненные комочки, которые при дальнейшем перемешивании распадаются. Замечено, что быстрое их схватывание вызывается переходом щелочей в карбонаты в результате взаимодействия с углекислотой при длительном хранении цемента на воздухе. В некоторых случаях оно носит характер ложного схватывания. Имеются данные о других (кроме гипса) видах замедлителей схватывания, их действие в большинстве случаев зависит от дозировки. Можно считать, что карбонаты, хлориды и нитраты являются ускорителями схватывания; сульфаты и фосфаты — замедлителями, за исключением сульфата глинозема, который действует как ускоритель. О влиянии добавок цветных металлов сведения разные. Их считали замедлителями схватывания, однако последние работы показали положительное влияние добавок небольших количеств цинка на твердение портландцемента. Б. Э. Юдович и Н. Т. Власова отмечают, что высокомарочные алитовыс цементы, не содержащие добавок, кроме гипса, могут характеризоваться аэрациопным ложным схватыванием. Оно вызвано образованием эттрингита в тонких слоях конденсата на дислокационной сетке поверхности частиц цемента.
Водоудерживающая способность
. При затворении цемента водой как в лабораторных, так и промышленных условиях можно видеть, как некоторые цементы полностью удерживают воду в период схватывания, другие же отделяют небольшой слой разной толщины. Поскольку водоцементное отношение при приготовлении бетонной смеси обычно всегда превышает значение, установленное при определении нормальной густоты цементного теста, то водоотделение становится особо заметным. От него во многом зависит однородность бетона и прочность сцепления в нем цементного раствора с крупным заполнителем и стальной арматурой.
При послойной укладке бетона отделяющаяся из него вода скапливается на поверхности укладываемых слоев. В результате образуется контактная прослойка бетона с большим содержанием воды, что вызывает расслаивание бетона, нарушающее его монолитность, а это особенно нежелательно при укладке массивного бетона. Расслоение может идти и внутри бетона; образующаяся в результате водоотделения пленка воды может заметно понизить сцепление цементного раствора с крупным заполнителем и арматурой.
Испарение этой воды вызывает образование дополнительного количества пор, содействующих диффузии агрессивной воды в глубину бетона. Повышение водо-удерживающей способности достигается введением в исходный цемент активной минеральной добавки (в виде трепела, опоки), а также применением некоторых поверхностно-активных веществ. Дозировка и вид добавки должны быть предварительно определены экспериментальным путем. Водоотделение может оказаться полезным, например, при вакуумировании или применении водопоглощающей опалубки, при однослойном бетонировании небольших по сечению конструкций, при изготовлении железобетонных труб способом центрифугирования и в других случаях, когда необходимо снижение В/Ц и повышение плотности и прочности бетона.
Равномерность изменения объема — важное свойство цемента, которое определяется в соответствии с требованиями стандарта. Цементный камень при определенной влажности дает усадку либо несколько расширяется. Однако изменения объема камня весьма малы и заметно на равномерность изменения объема при стандартном испытании не влияют.
Расширение цементного камня, вызывающее искривление исследуемых образцов либо появление на них волосных трещин,-— результат запоздалой, но весьма сильной по своему действию гидратации химически не связанного свободного оксида кальция в клинкере. Такое расширение называют кажущимся, поскольку объем гашеной извести меньше суммы объемов исходных оксида кальция и воды, вступивших в реакцию.
Считают, что частицы образовавшейся гашеной извести растут преимущественно в одном направлении; при этом создаются напряжения, вызывающие расширение массы, которое теоретически составляет 95,5% объема исходного оксида кальция. Такое явление происходит при гидратации крупнозернистых кристаллов оксида кальция, требующей длительного взаимодействия с водой. Цементный камень расширяется также при избыточном содержании крупнокристаллических зерен пери-клаза (оксида магния), а также при большом количестве добавки гипса.
На заводах получают клинкер с минимально допустимым количеством свободного оксида кальция в цементе, содержание периклаза и гипса в котором обеспечивает равномерность изменения объема. Достигается это при помощи тонкого помола сырьевой шихты равномерного состава, качественного обжига и быстрого охлаждения клинкера.
Поскольку расширение цементного камня может проявиться в опасных размерах спустя много лет после за-творения цемента, стандартом предусмотрен ускоренный метод испытания цемента. По ГОСТ стандартно изготовленные лепешки цементного теста подвергаются через сутки после затворения кипячению в воде; после охлаждения они не должны иметь искривлений и даже волосных трещин. В ряде стран испытание ведут по методу Ле Шателье путем кипячения через сутки после затворения цилиндрика цементного теста, разрезанного по длине и снабженного двумя иглами, концы которых расходятся под действием напряжений, возникающих в результате расширения цементного камня. Допустимое расширение составляет 3—10 мм, причем максимальный его размер предусмотрен в большинстве стандартов. В ряде стран регламентирован автоклавный метод испытания образцов призм в течение 3 ч при давлении 2,1 МПа. В США допускается расширение портландцемента, равное 0,8%, в других странах — 0,5, 1 и даже 1,3%.
Тепловыделение.
Гидратация цемента сопровождается выделением тепла, что может быть установлено по изменению температуры цементного теста, помещенного немедленно после его затворения в термос. В тонкостенных бетонных конструкциях это тепло сравнительно быстро рассеивается и заметно не влияет на структуру цементного камня.
Проблема тепловыделения привлекла внимание исследователей в связи с тем, что в массивном бетоне гидротехнических и других видов сооружений заметно повышается температура до значения, часто превышающего, примерно на 323К, температуру бетона при его укладке. Рост температуры вызывает напряжения, которые являются результатом неравномерного нагрева и охлаждения бетона; при малой его теплопроводности внутренние слои массива охлаждаются медленнее поверхностных. При возникновении больших термических напряжений в бетоне могут появиться трещины. Для устранения этих явлений применяют по возможности тощие бетонные смеси или укладывают в толщу массива трубы, по которым поступает вода для охлаждения бетона.
Клинкерные минералы при полной гидратации различаются по термохимическому эффекту, который для C2S состоит из тепла, выделяющегося как при химической реакции, так и при адсорбции воды гелем и составляет 504 кДж/кг. Тепловыделение при гидратации C3S равно 260 кДж/кг. Теплота гидратации для C4AF 420 кДж/кг й для С3А — 869 кДж/кг. Теплота образования гидросульфоалюминатов кальция составляет 558 кДж/кг безводного С3А. Теплота гидратации для СаО определена в 1170 кДж/кг и для MgO — 852 кДж/кг.
Изучение тепловыделения при гидратации портландцемента различного минералогического состава подтвердило, что наиболее термичнымн минералами в цементе являются C3S и С3А, причем C4AF замедляет тепловыделение других минералов. Основное количество тепла выделяется в первые 3—7 сут твердения. Примерное тепловыделение чистого, не содержащего добавок портландцемента для разной продолжительности твердения можно определить по разработанным в нашей стране коэффициентам, характеризующим долю участия клинкерных минералов в этом процессе.
Введение в портландцемент малых количеств активных минеральных добавок заметно не влияет на установленную зависимость.
Стандартную термохимическую характеристику цемента находят по ГОСТ при помощи термосного метода. Испытанию подвергают цементный раствор, в котором соотношение между цементом и песком устанавливается в зависимости от вида и марки цемента так, чтобы максимальное повышение температуры было бы близко к 288К. Расход цемента в единице объема раствора возрастает, если вместо портландцемента применяют пуццо-лановый и шлакопортландцемент.
С увеличением расхода цемента в 1 м3 бетона тепловыделение возрастает практически линейно. Повышение В/Ц приводит к заметному возрастанию теплового эффекта в случае применения алитового и алюминатного цементов. Зависимость тепловыделения от В/Ц у бетонов на белитовом цементе меньше. У бетонов с одинаковым расходом цемента и подвижностью изотермическое тепловыделение не зависит от свойств заполнителей, удельной теплоемкости и средней плотности материала зерен. Пластифицирующие и воздухововлекающие добавки по-разному влияют на тепловыделение. Введение ускорителей твердения приводит к увеличению тепловыделения. Набухание и усадка цемента. Набухание и усадка обусловлены способностью цементного камня и бетона изменять объем в зависимости от химических процессов, протекающих при твердении, и от влажности среды, в которой они находятся. Набухание сопровождается поглощением воды и увеличением массы цементного камня, достигающей 3—5% при продолжительности твердения 100 сут. Бетоны, находящиеся в воде, набухают меньше, чем цементный камень; через 6—12 мес. происходит стабилизация объемных изменений, хотя масса при этом продолжает увеличиваться. Набухание не вызывает снижения прочности, как это бывает при «запоздалой» гидратации СаОсвоб, периклаза, либо при взаимодействии щелочей цемента с реакционноспособным заполнителем бетона. Набухание цементного камня следует рассматривать как результат взаимодействия с водой, при котором образующийся цементный гель адсорбирует на своей чрезвычайно развитой поверхности воду, раздвигающую гидратиые новообразования. Поэтому при набухании внутренняя структура цементного камня уплотняется. Несомненно, что набухание вызывается также расклинивающим действием тонких пленок воды и осмотическими силами, возникающими в связи с разностью концентраций на поверхностях гидратированных частиц, и полу-проницаемостью, присущей цементному камню. Цементный камень и затвердевший бетон в воздушно-сухой среде дают усадку, сопровождающуюся потерей воды. Скорость усадки возрастает с уменьшением относительной влажности среды, а абсолютная величина усадки (мм/м) в несколько раз превышает набухание. Усадка наблюдается также при взаимодействии гидроксида кальция в цементном камне с углекислотой воздуха. Эта реакция протекает наиболее полно при определенной относительной влажности воздуха. Усадка бетона может привести к возникновению значительных напряжений, образованию микротрещин и макротрещин, нарушению монолитности конструкций и создать тем самым условия для активного действия других внешних агрессивных факторов. Нежелательна также усадка в предварительно напряженных конструкциях.
При вычислении потерь предварительного напряжения, а также в расчетах статически неопределимых систем нормативные значения деформаций усадки принимаются пока еще только в зависимости от марки бетона на сжатие без учета вида применяемого портландцемента, а также от жесткости или подвижности бетонной смеси.
Прочность цемента — одна из наиболее важных его физико-механических характеристик, от которой в основном и зависит прочность бетона в различных условиях твердения. Прочностные показатели цемента определяют, испытывая затвердевшие образцы из песчаного раствора в установленные сроки твердения. При этих испытаниях мы уже имеем дело с продуктом химического взаимодействия с водой, протекающего при гидратации цемента, поэтому на получаемые прочностные показатели цементного раствора, его физические характеристики оказывают влияние условия, при которых происходят эти химические процессы.
В стандартах на методы испытаний цемента строго регламентируются водоцементное отношение, условия приготовления, уплотнения и твердения испытуемых образцов, сроки их испытания, состав раствора, вид применяемого песка, размеры образцов. Стандартные методики каждой страны имеют свои отличительные особенности, поэтому невозможно точно сопоставить прочностные показатели цементов, получаемые в разных странах. Такое сопоставление возможно лишь в том случае, когда по разным стандартным методикам испытывается один и тот же образец цемента.
Для алита и алитовых портландцементов характерна близость коэффициентов нарастания прочности (в период от 1 мес до 2 лет). При сопоставлении же интенсивности твердения и цементов с преобладанием указанных минералов наблюдается некоторое различие, особенно заметное для белита и белитового портландцемента в период твердения от одного месяца до шести. Объясняется это тем обстоятельством, что заметный рост прочности белита в этот период не может проявиться при твердении цемента, так как решающее значение для формирования прочности цементного камня имеют процессы, связанные с участием в твердении C3S.
В специальных портландцементах, шлаковых, пуццолановых, пластифицированных, гидрофобных и др., влияние минералогического состава исходного цементного клинкера на прочность цемента сохраняется, однако при меньших относительных значениях получаемых показателей прочности. Вместе с тем необходимо учитывать возможность изменения этих коэффициентов в зависимости от состава бетона, содержания в составе цемента активных минеральных добавок, условий его изготовления и температурно-влажностных условий твердения.
Скорость взаимодействия цементных зерен с водой зависит от суммарной поверхности зерен или их удельной поверхности (см2/г). С увеличением тонкости помола (удельной поверхности) возрастает скорость процессов твердения и повышается прочность цементного камня. Чтобы получить заданную прочность, необходимо подобрать не только минералогический состав исходного клинкера и вещественный состав цемента, но и оптимальную гранулометрию цементного порошка при определенной его удельной поверхности.
При увеличении удельной поверхности независимо от его минералогического состава гидратируется больше цемента. Для предупреждения значительного развития усадки и других нежелательных явлений следует правильно подбирать дозировку гипса. От цемента зависит не только прочность, но и другие свойства бетона, в первую очередь, такие, как морозостойкость, трещиностойкость и др. Требования к удельной поверхности цемента должны выдвигаться с учетом и этих свойств. При рациональном гранулометрическом составе цемента создаются условия для длительного протекания процессов твердения цемента, обеспечивающих его «самозалечивание» при различных напряженных состояниях.
Значительно ускорить твердение цемента и повысить его прочность в возрасте до 28 сут можно, вводя специальные добавки — ускорители твердения, являющиеся преимущественно солями одновалентных, двухвалентных и трехвалентных металлов. Наибольшее практическое применение получил хлористый кальции, а также добавки сульфатов и карбонатов натрия и калия. Оптимальную дозировку добавок устанавливают обычно опытным путем.
Ползучесть цементного камня и его способность к релаксации напряжений при его высыхании повышаются. Наблюдения Девиса за ползучестью бетона, продолжавшиеся в течение 30 лет, показали, что деформация ползучести через 1 год, принятая за единицу, возрастает через два года до 1,14, через 5 лет — до 1,2, через 10 лет — до 1,26, через 20 лет — до 1,33 и через 30 лет — до 1,36.
Несмотря на большое число исследований единого уравнения для описания закономерностей деформаций ползучести бетона во времени нет. Выявлены линейные и нелинейные деформации ползучести. До некоторой границы нагрузки при сжатии деформации ползучести линейно зависят от значения напряжения в бетоне.
Переход линейной ползучести в нелинейную происходит в материале в условиях сжатия при напряжении выше RT, когда обнаруживаются микротрещины. Анализ физических явлений в бетоне показывает, что длительное действие нагрузки с напряжениями, превышающими RT, вызывает разрушение структуры, улавливаемое по изменению скорости ультразвука.
Мера ползучести имеет различное значение для бетона на обычном портландцементе и на высокопрочном. Для расчетов принимается, что ползучесть на высокопрочном портландцементе меньше. Исходят из того, что уменьшение меры ползучести с увеличением возраста бетона одинаково для обычного и высокопрочного портланднементов.
Морозостойкость
— это способность бетона сопротивляться попеременному замораживанию и оттаиванию при насыщении его пресной или морской водой.
Наиболее быстро в насыщенном водой бетоне замерзает «свободная» вода, находящаяся в пустотах и макропорах цементного камня; это происходит при температуре несколько ниже нуля, поскольку в воде содержатся такие растворимые гидратные новообразования, как щелочи и др. Температура замерзания воды в капилляpax зависит от размера капилляров; в особо мелких образуется при минус 233—223К. С дальнейшим понижением температуры возрастает количество воды, превращающейся в лед, но даже при 195К некоторая часть воды в наиболее мелких порах внутри геля остается.
Как известно, превращение воды в лед сопровождается увеличением объема на 9%. Г. И. Горчаков полагает, что главными факторами, определяющими напряжения в стенках капилляров цементного камня при замерзании воды, являются: степень заполнения капилляров водой, проницаемость стенок по отношению к воде, скорость кристаллизации воды и параметры, характеризующие внутренний размер капилляров и толщину их стенок. Снижение прочности и разрушение бетона под действием попеременного замораживания и оттаивания объясняется, главным образом, напряжениями, возникающими в структуре цементного камня и бетона.
Считают также, что разрушение стенок пор в цементном камне при замораживании и оттаивании — следствие возникновения гидравлического давления воды перед фронтом промерзания.
Чтобы получить бетон повышенной морозостойкости очень важно правильно выбрать цемент с учетом его химико-минералогического состава, дисперсности, наличия активных минеральных добавок, а также воздухо-вовлекающих, газообразующих, пластифицирующих и гидрофобных веществ. Важны также расход цемента на 1 м3 бетона, вид и качество применяемых заполнителей.
Наиболее морозостойки бетоны па алитовых высокопрочных, а также на сульфатостойких портландцементах. Наименее морозостойки при температурах замерзания до минус 223К бетоны на пуццолановых и шлакопортландцементах в связи с повышенным количеством воды, адсорбционно удерживаемой содержащимися в этих цементах активными минеральными добавками. Следует отметить, что пропаривание снижает морозостойкость цементных бетонов.
Цементы
К группе цементов, применяемых для приготовления цементных бетонов и растворов, относятся все виды портландцементов, шлакопортландцементов, пуццолановых портландцементов, песчанистый портландцемент, глиноземистые цементы, расширяющиеся и безусадочные цементы и сульфато-шлаковый цемент.
Портландцемент — гидравлическое вяжущее, твердеющее в воде и на воздухе, получаемое путем совместного тонкого измельчения клинкера и необходимого количества гипса. Клинкер получается в результате обжига до спекания сырьевой смеси надлежащего состава с преобладанием силикатов кальция (70—80%).
Изготовляются следующие разновидности портландцемента: пластифицированный; гидрофобный; сульфатостойкий; с умеренной экзотермией; быстротвердеющий; -белый; цветной; тампонажный; для бетонных покрытий автомобильных дорог; для производства асбестоцементных изделий; магнезиальный.
Пластифицированный портландцемент изготовляется путем введения в обычный портландцемент при его помоле пластифицирующей поверхностно-активной добавки, придающей бетонам и растворам на этом цементе повышенную подвижность, удобо-укладываемость и морозостойкость.
Гидрофобный портландцемент изготовляется путем введения в обычный портландцемент гидрофобно-пластифицирующей добавки, понижающей гигроскопичность цемента при его хранении и повышающей подвижность, удобоукладываемость и морозостойкость бетонов и растворов на этом цементе. Гидрофобный портландцемент не комкуется и практически не теряет прочности при длительных перевозках и хранении.
Сульфатостойкий портландцемент изготовляется из клинкера нормированного химического и минералогического составов. Он обладает повышенной сульфатостой-костью и пониженной экзотермией, необходимыми для изготовления бетонных и железобетонных конструкций наружных зон гидротехнических и других сооружений, работающих в условиях сульфатной агрессии при одновременном систематическом попеременном замораживании и оттаивании, увлажнении и высыхании.
Портландцемент с умеренной экзотермией изготовляется из клинкера нормированного минералогического состава, обеспечивающего при несколько повышенной сульфатостойкости умеренную экзотермию, необходимую при изготовлении бетонных и железобетонных конструкций, работающих в пресной или слабо минерализованной воде и в условиях систематического многократного замораживания и оттаивания, увлажнения и высыхания.
Быстротвердеющий портландцемент обладает более интенсивным, чем обычный портландцемент, нарастанием прочности в начальный период твердения.
Белый портландцемент — гидравлическое вяжущее белого цвета, изготовляемое путем совместного тонкого измельчения маложелезистого клинкера, получаемого спеканием при обжиге сырьевой смеси соответствующего состава, активной минеральной добавки и гипса. Активная минеральная добавка и гипс в тонкоизмельченном состоянии должны иметь белизну не ниже установленной для цемента данного сорта. Для повышения белизны и устранения зеленоватых оттенков клинкер подвергается отбеливанию.
На основе белого портландцемента (или клинкера) путем тщательного смешивания или совместного помола с красящими пигментами могут быть получены цементы различных цветов.
Страниц: 1 2 3 4 5 6 7
Рубрики: Строительные материалы и Инструменты
Метки: Строительный раствор, Тампонажный цемент, Цветной цемент
Цветной портландцемент — гидравлическое вяжущее, получаемое путем совместного помола портландцементного клинкера с пигментным сырьем, минеральными или органическими пигментами, а также помола цветных клинкеров с активной минеральной добавкой в количестве до 6% и необходимым количеством гипса. Для производства цветных цементов используется клинкер белого портландцемента, цветной клинкер, а также отбеленные клинкеры с пониженным содержанием красящих окислов железа и марганца.
Цветные портландцемента подразделяются на следующие разновидности: желтые, розовые, красные, коричневые, зеленые, голубые и черные.
Тампонажный цемент, являющийся разновидностью портландцемента, обладает высокой прочностью в начальные сроки твердения, необходимой при тампонировании нефтяных и газовых скважин.
Тампонажный цемент выпускается двух видов: «для холодных» скважин и для «горячих» скважин. Он применяется в виде цементного теста состава 1:0с повышенным содержанием воды (40—50%).
Портландцемент (в том числе пластифицированный и гидрофобный), предназначенный для бетонных покрытий автомобильных дорог, должен удовлетворять следующим специальным требованиям:
1. введение инертных добавок в состав портландцемента не допускается;
2. допускается введение в состав портландцемента при его помоле активных минеральных добавок только в виде гранулированного доменного шлака в количестве не более 15%;
3. расчетное содержание трехкальциевого алюмината в клинкере допускается не более 10% .
Портландцемент для производства асбестоцементных изделий — гидравлическое вяжущее, получаемое путем совместного тонкого измельчения портландцементного клинкера нормированного химического и минералогического состава и гипса; цемент не должен содержать никаких активных или инертных минеральных добавок.
Магнезиальный портландцемент — гидравлическое вяжущее, продукт тонкого измельчения клинкера, получаемого путем обжига до спекания обогащенной окисью Железа искусственной смеси известково-магнезиальных и глинистых пород, состав которой обеспечивает преобладание в полученном клинкере силикатов кальция.
Шлакопортландцемент — гидравлическое вяжущее, твердеющее в воде и на воздухе, получаемое путем совместного тонкого измельчения клинкера, необходимого количества гипса и доменного гранулированного шлака или путем тщательного смешивания тех же материалов, измельченных раздельно. Весовое содержание шлака в шлакопортландцементе должно находиться в пределах 30—70% .
К разновидностям шлакопортландцемента относятся быстротвердеющий шлакопортландцемент и шлаковый магнезиальный портландцемент.
Шлакопортландцемент обладает примерно такой же воздухостойкостью, как и обычный портландцемент, но бетоны и растворы на основе шлакопортландцемента в отношении морозостойкости уступают бетонам и растворам на обычном портландцементе.
Шлакопортландцемент не оказывает корродирующего действия на заложенную в бетон стальную арматуру и достаточно прочно сцепляется с ней. Поэтому его применяют в железобетонных конструкциях наравне с портландцементом. Схватывание и твердение шлакопортландцемента происходит медленнее, чем портландцемента, особенно при низких положительных температурах.
При твердении шлакопортландцемента выделяется меньше тепла, чем при твердении портландцемента. Это позволяет эффективно применять шлакопортландцемент в массивных сооружениях.
Быстротвердеющий шлакопортландцемент обладает более интенсивным, чем обычный шлакопортландцемент, нарастанием прочности в начальный период твердения. Количество доменного гранулированного шлака в быстротвердеющем шлакопортландцементе должно составлять не менее 30 и не более 50% от веса цемента.
Шлаковый магнезиальный портландцемент — гидравлическое вяжущее, получаемое совместным тонким измельчением магнезиального портландцементного клинкера, гранулированного доменного шлака и необходимого количества гипса или тщательным смешиванием тех же материалов, измельченных раздельно. Весовое содержание гранулированного доменного шлака должно составлять не менее 30 и не более 70% от веса готового продукта.
Пуццолановый портландцемент — гидравлическое вяжущее, твердеющее в во-Де и во влажных условиях, получаемое путем совместного тонкого измельчения клинкера, необходимого количества гипса и активной минеральной добавки или путем тщательного смешивания тех же материалов, измельченных раздельно.
Бетоны, изготовленные из пуццоланового портландцемента, отличаются повышенной водостойкостью и водонепроницаемостью. Пуццолановый портландцемент эффективно твердеет в воде и во влажных условиях. При твердении на воздухе он дает несколько большую усадку, чем портландцемент.
Морозостойкость и воздухостойкость бетонов на пуццолановом портландцементе ниже, чем бетонов на портландцементе.
Пуццолановый портландцемент при твердении выделяет меньше тепла, чем портландцемент, поэтому его не следует применять для бетонных работ при пониженных температурах, целесообразно его использование для бетонирования массивных сооружений.
Сульфатостойкий пуццолановый портландцемент изготовляется из клинкера нор. мированного химического и минералогического состава, обеспечивающего повышенную по сравнению с обычным пуццолановым портландцементом сульфатостойкость, необходимую для изготовления бетонных и железобетонных конструкций, работающих в подводных или подземных частях сооружений в условиях сульфатной агрессии .
Песчанистый портландцемент представляет собой вяжущее, наиболее эффективно твердеющее при автоклавной обработке и состоящее из смеси тонкоизмельченно-го портландцементного клинкера и кварцевого песка при необходимой добавке гипса. Его получают путем совместного помола составляющих компонентов или тщательного смешивания тех же компонентов, измельченных раздельно.
Глиноземистый цемент — быстротвердеющее гидравлическое вяжущее, получаемое путем тонкого измельчения клинкера, изготовляемого расплавлением или обжигом до спекания сырьевой смеси надлежащего состава, обеспечивающего преобладание в готовом продукте низкоосновных алюминатов кальция.
К разновидностям глиноземистого цемента относится высокоглиноземистый цемент.
Обязательным условием для нормального твердения глиноземистого цемента и длительного сохранения им прочности является пониженная положительная температура твердения (ниже 25° С) в начальные и последующие сроки твердения, ввиду чего эти цементы не допускается применять в условиях жаркого климата.
Запрещается смешивать глиноземистый цемент с портландцементом и другими видами цементов.
Высокоглиноземистый цемент отличается от обычного глиноземистого цемента более высоким содержанием глинозема, обладает высокой огнеупорностью и применяется для изготовления высокоогнеупорных бетонов и растворов.
Водонепроницаемый расширяющийся цемент (ВРЦ) является быстро схватывающимся и быстротвердеющим гидравлическим вяжущим, получаемым путем тщательного смешивания глиноземистого цемента, высокопрочного или строительного гипса и молотого высокоосновного гидроалюмината кальция примерно в следующих соотношениях: глиноземистого цемента — 70, гипса — 20, четырех кальциевого гидроалюмината — 10%.
Водонепроницаемый безусадочный цемент (ВБЦ) является быстросхватывающим-ся и быстротвердеющим гидравлическим вяжущим, получаемым путем тщательного смешивания тех же компонентов, что и при производстве расширяющегося цемента ВРЦ, но в других соотношениях.
Гипсоглиноземистый расширяющийся цемент является быстротвердеющим гид-дравлическим вяжущим, получаемым совместным тонким измельчением высокоглиноземистых шлаков (70%) и природного двуводного гипса (30%).
Сульфатно-шлаковый цемент — гидравлическое вяжущее, получаемое путем совместного тонкого измельчения высушенных гранулированных доменных шлаков я гипса или природного либо высокообожженного сульфата кальция, размолотых с небольшой добавкой портландцемента, извести или обожженного доломита.
Важнейшим свойством сульфатно-шлаковых цементов является повышенная стойкость в сульфатных водах. При твердении сульфатно-шлаковый цемент выделяет меньше тепла, чем портландцемент. Сульфатно-шлаковый цемент не оказывает корродирующего действия на заложенную в бетон стальную арматуру.
Категорически запрещается смешивание сульфатно-шлакового цемента с известью, портландцементом и его разновидностями и другими цементами.
Известь. Строительная известь получается путем обжига ниже температуры спекания кальциево-магниевых карбонатных горных пород — известняков, мела, поломитизированных известняков, доломитов и мергелистых известняков и выпускается в комовом или тонкоизмельченном виде.
Тонкоизмельченная строительная известь получается путем гашения или размола комовой извести, в процессе которого допускается введение минеральных тонко-молотых добавок.
По условиям твердения известь строительная разделяется на воздушную и гидравлическую.
Известь строительная воздушная — продукт, получаемый путем обжига до возможно полного выделения углекислоты из чистых или доломитизированных из-ветняков. Она обеспечивает твердение и сохранение прочности строительных раствори в воздушно-сухих условиях.
Известь строительная воздушная изготовляется следующих видов: негашеная комовая — продукт обжига карбонатного сырья с содержанием глинистых примесей не более 6%;
негашеная молотая— продукт помола комовой извести, а также совместного помола извести с различными минеральными добавками;
гидратная (пушонка) — продукт гидратации негашеной извести, влажность извести-пушонки не должна превышать 5%, считая на влажное вещество;
молотая карбонатная — продукт совместного помола негашеной извести и карбонатных пород.
Известь строительная воздушная комовая негашеная, молотая и известь гидратная выпускаются двух сортов: первого и второго.
Известь строительная гидравлическая выпускается в порошкообразном виде и представляет собой тонкомолотую обожженную мергелистую карбонатную горную породу с содержанием глинистых примесей от 6 до 20%.
Растворы и бетоны на гидравлической извести после затвердения на воздухе продолжают твердеть и сохранять свою прочность и под водой.
По скорости гашения известь подразделяется на быстрогасящуюся (менее 20 мин) и медленногасящуюся (более 20 мин). Содержание непогасившихся зерен в комовой извести после ее гашения должно быть не более 10% в 1-м сорте и не более 20% — во 2-м.
Известково-шлаковые, известково-пуццолановые, известково-кремнеземистые, известково-нефелино-вые вяжущие и романцемент. Известково-шлаковые (гидравлические) вяжущие получают путем совместного измельчения высушенных гранулированных Доменных шлаков и извести (гидравлической или воздушной) или тщательного смешивания в сухом виде тех же материалов, измельченных раздельно в тонкий порошок. Содержание извести должно находиться в пределах 10—30%.
Для регулирования сроков схватывания и улучшения процессов твердения добавляется при помоле этого вяжущего около 5% гипса; возможна также добавка 10—20% Портландцемента.
Известково-шлаковое вяжущее медленно схватывается и медленно твердеет, но при длительном нормальном твердении во влажных условиях или в воде приобретает значительную прочность.
Морозостойкость бетона и раствора на известково-шлаковых вяжущих низка 1 значительно повышается при наличии в их составе около 20% портландцемента.
Известково-пуццолановые вяжущие подразделяются на следующие:
1. Известково-пуццолановые, получаемые путем совместного измельчения активной минеральной добавки с известью и при необходимости с добавкой портландцемента;
2. Известково-зольные (в том числе сланцезольные), получаемые путем совместного помола топливных зол и шлаков, содержащих окись кальция в количестве не менее 15% с кремнеземистой активной минеральной добавкой и при необходимости с добавкой портландцемента.
Для регулирования сроков схватывания и улучшения процессов твердения при помоле этих вяжущих добавляется около 5% гипса.
Известково-пуццолановые вяжущие твердеют медленно при пониженных положительных температурах и быстрее при тепловлажностной обработке, особенно в автоклаве.
Известково-кремнеземистые и известково-нефелийовые вяжущие представляют собой тонкоизмельченные смеси материалов надлежащего состава. Бетоны на этих вяжущих в результате кратковременного твердения в автоклавах образуют прочный камень.
Известково-кремнеземистые вяжущие состоят из смеси тонкоизмельченных кремнеземистых материалов (кварцевый песок, маршалит, песчаники, активные минеральные добавки и др.) и необходимого количества извести.
Известково-нефелиновые вяжущие состоят из смеси тонкоизмельченного высушенного нефелинового шлама, характеризующегося высоким содержанием двухкальциевого силиката, и необходимого количества извести.
Романцемент — гидравлическое вяжущее, получаемое путем измельчения в тонкий порошок обожженных известковых или магнезиальных мергелей или же искусственных смесей известняков и глин при температурах, при которых обжигаемый материал не доводится до спекания. Сроки схватывания романцемента от начала затвердения должны быть: начало не ранее 15 мин, конец — не позднее 24 ч.
Гипсовые вяжущие. Это воздушные вяжущие, получаемые путем тепловой обработки гипсового сырья и помола до или после этой обработки. Производятся следующие виды гипсовых вяжущих материалов: гипс строительный; гипс формовочный; гипс технический (высокопрочный); ангидритовое вяжущее; высокообжиговый гипс;
гипсовые вяжущие из гипсосодержащих пород.
При производстве гипса строительного для регулирования сроков схватывания и улучшения его физико-механических свойств допускается введение добавок. В зависимости от качества гипс строительный подразделяется на первый и второй сорт.
Гипс формовочный— продукт тепловой обработки гипсового природного камня, отличающийся от гипса строительного более тонким помолом и большей прочностью. Величина относительного объемного расширения формовочного гипса не должна превышать 0,15%.
Гипс технический (высокопрочный) — продукт, получаемый тепловлажностной обработкой гипсового камня под давлением с последующим его размолом. Гипс технический отличается сравнительно малой водопотребностью и повышенной прочностью.
Ангидритовое вяжущее — продукт обжига при температуре 600—800° С гипсового камня или природного ангидрита (без обжига), измельченного в тонкий порошок совместно с различными добавками (катализаторами).
В качестве добавок при изготовлении ангидритового вяжущего применяют бисульфат или сульфат натрия в смеси с железным или медным купоросом, известь, доломит, обожженный при температуре около 900° С, основной доменный шлак, золы горючих сланцев и др.
Высокообжиговый гипс — продукт обжига при температуре 800—1000° С сырья, состоящего из двуводного гипса или ангидрита, измельченный в тонкий порошок. Гипсовые вяжущие из гипсосодержащих пород — продукты тепловой обработки гипессодержащих пород (сажи, глиногипса) и отходов промышленности.
Не допускается их применение для изготовления изделий и конструкций, эксплуатируемых в условиях с относительной влажностью воздуха более 60%.
Магнезиальные вяжущие представляют собой тонкомолотые порошки, содержащие окись магния и твердеющие при затворении водными растворами некоторых солей,, главным образом хлористого или сернокислого магния.
Магнезиальные вяжущие изготовляются следующих видов:
магнезит каустический получается путем обжига при температуре диссоциации и ниже температуры спекания природного магнезита и подразделяется в зависимости от химического состава на первый, второй и третий классы;
доломит каустический (заменитель каустического магнезита для менее ответствен ных изделий), получаемый обжигом природного доломита до полного выделения углекислоты из углекислого магния с последующим помолом.
В качестве затворителей для магнезиальных вяжущих применяется водный раствор хлористого или сернокислого магния. Как заменители при специальном обосновании для затворения могут быть применены растворы следующих солей: хлористого или сернокислого железа, хлористого цинка, отходящей рапы (отходы при извлечении бромг из морских озер), карналита искусственного, растворы соляной или серной кислот.
Магнезиальные вяжущие могут применяться только при условии твердения их на воздухе с относительной влажностью менее 60% .
Стекло жидкое. Стекло жидкое подразделяется на натриевое и калийное.
Натриевое стекло жидкое применяется в качестве вяжущего в виде водного раствора совместно с кремнефтористым натрием или другими специальными добавками и молотыми наполнителями. В строительстве применяется натриевое стекло жидкое с модулем от 2,5 до 3. Кремнефтористый натрий технический применяется 1-го и 2-го сортов.
Калийное стекло жидкое применяется в виде водного раствора в качестве связующего в силикатных красках, мастиках и замазках. Модуль калийного жидкого* стекла должен быть в пределах от 3 до 4; удельный вес — от 1,4 до 1,42.
Натриевое стекло жидкое применяется для:
уплотнения (силикатизации) грунтов, бетонной и каменной кладки;
приготовления жароупорных и огнеупорных бетонов с предельной температурой эксплуатации не более 1400° С;
приготовления кислотостойких бетонов и растворов;
приготовления огнезащитных обмазок.
Калийное стекло жидкое применяется для приготовления:
1. силикатных красок, предназначаемых для окраски фасадов и внутренних поверхностей производственных зданий;
2. кислотостойких бетонов и растворов.
Кислотоупорный кварцевый кремнефтористый цемент представляет собой порошкообразный материал, изготовляемый путем совместного помола или тщательного смешивания раздельно измельченных кварцевого песка и кремнефтористого натрия затворяемый на водном растворе силиката натрия (стекло жидкое), после чего он превращается на воздухе в прочное камневидное тело, способное противостоять действию большинства минеральных и органических кислот.