Похожие рефераты | Скачать .docx |
Реферат: Станки с числовым программным управлением (ЧПУ)
Содержание
1. Общие сведения о станках с ЧПУ
2. Конструктивные особенности станков с ЧПУ
3. Многоцелевые станки с ЧПУ
4. Оснастка и инструмент для многоцелевых станков с ЧПУ
5. Серия Mynx NM (Doosan)
6. Организация работы оператора многоцелевых станков с ЧПУ
7. Технологии обработки деталей на многоцелевых станках с ЧПУ
Список литературы
1. Общие сведения о станках с ЧПУ
Под управлением станком принято понимать совокупность воздействий на его механизмы, обеспечивающие выполнение технологического цикла обработки, а под системой управления - устройство или совокупность, реализующих эти воздействия.
Числовое программное управление (ЧПУ) - это управление, при котором программу задают в виде записанного на каком-либо носителе массива информации. Управляющая информация для систем ЧПУ является дискретной и ее обработка в процессе управления осуществляется цифровыми методами. Управление технологическими циклами практически повсеместно осуществляется с помощью программируемых логических контроллеров, реализуемых на основе принципов цифровых электронных вычислительных устройств.
Системы ЧПУ практически вытесняют другие типы систем управления.
По технологическому назначению и функциональным возможностям системы ЧПУ подразделяют на четыре группы:
позиционные , в которых задают только координаты конечных точек положения исполнительных органов после выполнения ими определенных элементов рабочего цикла;
контурные, или непрерывные , управляющие движением исполнительного органа по заданной криволинейной траектории;
универсальные (комбинированные) , в которых осуществляется программирование как перемещений при позиционировании, так и движения исполнительных органов по траектории, а также смены инструментов и загрузки-выгрузки заготовок;
многоконтурные системы , обеспечивающие одновременное или последовательное управление функционированием ряда узлов и механизмов станка.
Примером применения систем ЧПУ первой группы являются сверлильные, расточные и координатно-расточные станки. Примером второй группы служат системы ЧПУ различных токарных, фрезерных и круглошлифовальных станков. К третьей группе относятся системы ЧПУ различных многоцелевых токарных и сверлильно-фрезерно-расточных станков.
К четвертой группе относятся бесцентровые круглошлифовальные станки, в которых от систем ЧПУ управляют различными механизмами: правки, подачи бабок и т.д. Существуют позиционные, контурные, комбинированные и многоконтурные (рис.ЧПУ.1, а) циклы управления.
|
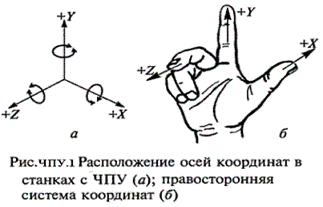
По способу подготовки и ввода управляющей программы различают так называемые оперативные системы ЧПУ (в этом случае управляющую программу готовят и редактируют непосредственно на станке, в процессе обработки первой детали из партии или имитации ее обработки) и системы, для которых управляющая программа готовится независимо от места обработки детали. Причем независимая подготовка управляющей программы может выполняться либо с помощью средств вычислительной техники, входящих в состав систем ЧПУ данного станка, либо вне ее (вручную или с помощью системы автоматизации программирования).
Программируемые контроллеры - это устройства управления электроавтоматикой станка. Большинство программируемых контролеров имеют модельную конструкцию, в состав которой входят источник питания, процессорный блок и программируемая память, а также различные модули входов/выходов. Для создания и отладки программ работы станка применяют программирующие аппараты. Принцип работы контроллера: опрашиваются необходимые входы/выходы и полученные данные анализируются в процессорном блоке. При этом решаются логические задачи и результат вычисления передается на соответствующий логический или физический выход для подачи в соответствующий механизм станка.
В программируемых контролерах используют различные типы памяти, в которой хранится программа электроавтоматики станка: электрическую перепрограммируемую энергонезависимую память; оперативную память со свободным доступом; стираемую ультрафиолетовым излучением и электрически перепрограммируемую.
Программируемый контролер имеет систему диагностики: входов/выходов, ошибки в работе процессора, памяти, батареи, связи и других элементов. Для упрощения поиска неисправностей современные интеллектуальные модули имеют самодиагностику. Программоноситель может содержать как геометрическую, так технологическую информацию. Технологическая информация обеспечивает определенный цикл работы станка, а геометрическая - характеризует форму, размеры элементов обрабатываемой заготовки и инструмента и их взаимное положение в пространстве.
Станки с программным управлением (ПУ) по виду управления подразделяют на станки и системами циклового программного управления (ЦПУ) и станки с системами числового программного управления (ЧПУ). Системы ЦПУ более просты, так как в них программируется только цикл работы станка, а величины рабочих перемещений, т.е. геометрическая информация, задаются упрощенно, например с помощью упоров. В станках с ЧПУ управление осуществляется от программоносителя, на который в числовом виде занесена и геометрическая, и технологическая информация.
В отдельную группу выделяют станки с цифровой индикацией и преднабором координат. В этих станках имеется электронное устройство для задания координат нужных точек (преднабором координат) и крестовый стол, снабженный датчиками положения, который дает команды на перемещение до необходимой позиции. При этом на экране высвечивается каждое текущее положение стола (цифровая индикация). В таких станках можно применять или преднабор координат или цифровую индикацию; исходную программу работы задает станочник.
В моделях станков с ПУ для обозначения степени автоматизации добавляется буква Ф с цифрой: Ф1-станки с цифровой индикацией и преднабором координат; Ф2-станки с позиционными и прямоугольными системами чпу; Ф3-станки с контурными системами ЧПУ и Ф4-станки с универсальной системой ЧПУ для позиционной и контурной обработки. Особую группу составляют станки, имеющие ЧПУ для многоконтурной обработки, например бесцентровые круглошлифовальные станки. Для станков с цикловыми системами ПУ в обозначении модели введен индекс Ц, с оперативными системами - индекс Т (например, 16К2Т1).
Системы числового программного управления (СЧПУ)-это совокупность специализированных устройств, методов и средств, необходимых для осуществления ЧПУ станками. Устройство ЧПУ (УЧПУ) станками - это часть СЧПУ, выполненная как единое целое с ней и осуществляющая выдачу управляющих воздействий по заданной программе.
В международной практике приняты следующие обозначения: NC-ЧПУ; HNC-разновидность ЧПУ с заданием программы оператором с пульта с помощью клавиш, переключателей и т.д.; SNS-устройство ЧПУ, имеющее память для хранения всей управляющей программы; CNC-управление автономным станком с ЧПУ, содержание мини-ЭВМ или процессор; DNS-управление группой станков от общей ЭВМ.
Для станков с ЧПУ стандартизованы направления перемещения и их символика. Стандартом ISO-R841 принято за положительное направление перемещения элемента станка считать то, при котором инструмент или заготовка отходят один от другого. Исходной осью (ось Z) является ось рабочего шпинделя. Если эта ось поворотная, то ее положение выбирают перпендикулярно плоскости крепления детали. Положительно направление оси Z-от устройства крепления детали к инструменту. Тогда оси X и Y расположены так, как это показано на рис.ЧПУ.1.
Использование конкретного вида оборудования с ЧПУ зависит от сложности изготовления детали и серийности производства. Чем меньше серийность производства, тем большую технологическую гибкость должен иметь станок.
При изготовлении деталей со сложными пространственными профилями в единичном и мелкосерийном производстве использование станков с ЧПУ является почти единственным технически оправданным решением. Это оборудование целесообразно применять в случае, если невозможно быстро изготовить оснастку. В серийном производстве также целесообразно использовать станки с ЧПУ. В последнее время широко используют автономные станки с ЧПУ или системы из таких станков в условиях переналаживаемого крупносерийного производства.
Принципиальная особенность станка с ЧПУ - это работа по управляющей программе (УП), на которой записаны цикл работы оборудования для обработки конкретной детали и технологические режимы. При изменении обрабатываемой на станке детали необходимо просто сменить программу, что сокращает на 80...90% трудоемкость переналадки по сравнению с трудоемкостью этой операции на станках с ручным управлением.
Основные преимущества станков с ЧПУ:
производительность станка повышается в 1,5...2,5 раза по сравнению с производительностью аналогичных станков с ручным управлением;
сочетается гибкость универсального оборудования с точностью и производительностью станка-автомата;
снижается потребность в квалифицированных рабочих станочниках, а подготовка производства переносится в сферу инженерного труда;
детали, изготовленные по одной программе, являются взаимозаменяемыми, что сокращает время пригоночных работ в процессе сборки;
сокращаются сроки подготовки и перехода на изготовление новых деталей благодаря предварительной подготовке программ, более простой и универсальной технологической оснастке;
снижается продолжительность цикла изготовления деталей и уменьшается запас незавершенного производства.
2. Конструктивные особенности станков с ЧПУ
Станки с ЧПУ имеют расширенные технологические возможности при сохранении высокой надежности работы. Конструкция станков с ЧПУ должна, как правило, обеспечивать совмещение различных видов обработки (точение-фрезерование, фрезерование-шлифование), удобство загрузки заготовок, выгрузки деталей (что особенно важно при использовании промышленных роботов), автоматическое или дистанционное управление сменой инструмента и т.д.
Повышение точности обработки достигается высокой точностью изготовления и жесткостью станка, превышающей жесткость обычного станка того же назначения, для чего производят сокращение длины его кинематических цепей: применяют автономные приводы, по возможности сокращают число механических передач. Приводы станков с ЧПУ должны также обеспечивать высокое быстродействие.
Повышению точности способствует и устранение зазоров в передаточных механизмах приводов подач, снижение потерь на трение в направляющих и других механизмах, повышение виброустойчивости, снижение тепловых деформаций, применение в станках датчиков обратной связи. Для уменьшения тепловых деформаций необходимо обеспечить равномерный температурный режим в механизмах станка, чему, например, способствует предварительный разогрев станка и его гидросистемы. Температурную погрешность станка можно также уменьшить, вводя коррекцию в привод подач от сигналов датчиков температур.
Базовые детали (станины, колонны, салазки). Столы, например, конструируют коробчатой формы с продольными и поперечными ребрами. Базовые детали изготавливают литыми или сварными. Наметилась тенденция выполнять такие детали из полимерного бетона или синтетического гранита, что в еще большей степени повышает жесткость и виброустойчивость станка.
Направляющие станков с ЧПУ имеют высокую износостойкость и малую силу трения, что позволяет снизить мощность следящего привода, увеличить точность перемещений, уменьшить рассогласование в следящей системе.
Направляющие скольжения станины и суппорта для уменьшения коэффициента трения создают в виде пары скольжения "сталь (или высококачественный чугун)-пластиковое покрытие (фторопласт и др.)"
Направляющие качения имеют высокую долговечность, характеризуются небольшим трением, причем коэффициент трения практически не зависит от скорости движения. В качестве тел качения используют ролики. Предварительный натяг повышает жесткость направляющих в 2...3 раза, для создания натяга используют регулирующие устройства.
Приводы и преобразователи для станков с ЧПУ. В связи с развитием микропроцессорной техники применяют преобразователи для приводов подачи и главного движения с полным микропроцессорным управлением - цифровые приводы представляют собой электродвигатели, работающие на постоянном или переменном токе. Конструктивно преобразователи частоты, сервоприводы и устройства главного пуска и реверса являются отдельными электронными блоками управления.
Привод подачи для станков с ЧПУ. В качестве привода используют двигатели, представляющие собой управляемые от цифровых преобразователей синхронные или асинхронные машины. Бесколлекторные синхронные (вентильные) двигатели для станков с ЧПУ изготавливают с постоянным магнитом на основе редкоземельных элементов и оснащают датчиками обратной связи и тормозами. Ассинхронные двигатели применяют реже, чем синхронные. Привод движения подач характеризуется минимально возможными зазорами, малым временем разгона и торможения, небольшими силами трения, уменьшенным нагревом элементов привода, большим диапазоном регулирования. Обеспечение этих характеристик возможно благодаря применению шариковых и гидростатических винтовых передач, направляющих качения и гидростатических направляющих, беззазорных редукторов с короткими кинематическими цепями и т.д.
Приводами главного движения для станков с ЧПУ обычно являются двигатели переменного тока - для больших мощностей и постоянного тока - для малых мощностей. В качестве приводов служат трехфазные четырехполосные асинхронные двигатели, воспринимающие большие перегрузки и работающие при наличии в воздухе металлической пыли, стружки, масла и т.д. Поэтому в их конструкции предусмотрен внешний вентилятор. В двигатель встраивают различные датчики, например датчик положения шпинделя, что необходимо для ориентации или обеспечения независимой координаты.
Преобразователи частоты для управления асинхронными двигателями имеют диапазон регулирования до 250. Преобразователи представляют собой электронные устройства , построенные на базе микропроцессорной техники. Программирование и параметрирование их работы осуществляются от встроенных программаторов с цифровым или графическим дисплеем. Оптимизация управления достигается автоматически после введения параметров электродвигателя. В математическом обеспечении заложена возможность настройки привода и пуск его в эксплуатацию.
Шпиндели станков с ЧПУ выполняет точными, жесткими, с повышенной износостойкостью шеек, посадочных и базирующих поверхностей. Конструкция шпинделя значительно усложняется из-за встроенных в него устройств автоматического режима и зажима инструмента, датчиков при адаптивном управлении и автоматической диагностике.
Опоры шпинделя должны обеспечить точность шпинделя в течение длительного времени в переменных условиях работы, повышенную жесткость, небольшие температурные деформации. Точность вращения шпинделя обеспечивается прежде всего высокой точностью изготовления подшипников.
Наиболее часто в опорах шпинделей применяют подшипники качения. Для уменьшения влияния зазоров и повышения жесткости опор обычно устанавливают подшипники с предварительным натягом или увеличивают число тел качения. Подшипники скольжения в оправках шпинделей применяют реже и только при наличии устройств с периодическим (ручным) или автоматическим регулированием зазора в осевом или радиальном направлении. В прецизионных станках применяют аэростатические подшипники, в которых между шейкой вала и поверхностью подшипника находится сжатый воздух, благодаря этому снижается износ и нагрев подшипника, повышается точность вращения и т.п.
Привод позиционирования (т.е. перемещение рабочего органа станка в требуемую позицию согласно программе) должен иметь высокую жесткость и обеспечивать плавность перемещения при малых скоростях, большую скорость вспомогательных перемещений рабочих органов (до 10 м/мин и более).
Вспомогательные механизмы станков с ЧПУ включают в себя устройства смены инструмента, уборки стружки, систему смазывания, зажимные приспособления, загрузочные устройства и т.д. Эта группа механизмов в станках с ЧПУ значительно отличается от аналогических механизмов, используемых в обычных универсальных станках. Например, в результате повышения производительности станков с ЧПУ произошло резкое увеличение количества сходящей стружки в единицу времени, а отсюда возникла необходимость создания специальных устройств для отвода стружки. Для сокращения потерь времени при загрузке применяют приспособления, позволяющие одновременно устанавливать заготовку и снимать деталь вовремя обработки другой заготовки.
Устройства автоматической смены инструмента (магазины, автооператоры, револьверные головки) должны обеспечивать минимальные затраты времени на смену инструмента, высокую надежность в работе, стабильность положения инструмента, т.е. постоянство размера вылета и положения оси при повторных сменах инструмента, имеют необходимую вместимость магазина или револьверные головки.
Револьверная головка -это наиболее простое устройство смены инструмента: установку и зажим инструмента осуществляют вручную. В рабочей позиции один из шпинделей приводится во вращение от главного привода станка. Револьверные головки устанавливают на токарные, сверлильные, фрезерные, многоцелевые станки с ЧПУ; в головке закрепляют от 4 до 12 инструментов.
3. Многоцелевые станки с ЧПУ
Благодаря оснащению многоцелевых станков (МС) устройствами ЧПУ и автоматической смены инструмента существенно сокращается вспомогательное время при обработке и повышается мобильность переналадки. Сокращение вспомогательного времени достигается благодаря автоматическим установке инструмента (заготовки) по координатам, выполнению всех элементов цикла, смене инструментов, кантованию и смене заготовки, изменению режимов резания, выполнению контрольных операций, а также большим скоростям вспомогательных перемещений.
|
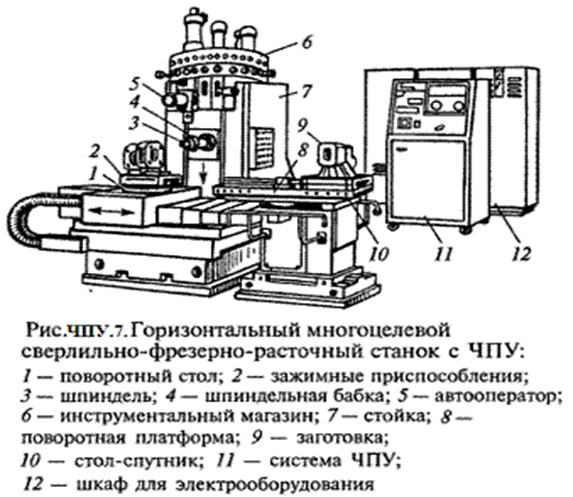
По назначению МС делятся на две группы: для обработки заготовок корпусных и плоских деталей и для обработки заготовок деталей типа тел вращения. В первом случае для обработки используют МС сверлильно-фрезерно-расточной группы, а во втором-токарной и шлифовальной групп. Рассмотрим МС первой группы, как наиболее часто используемые.
|
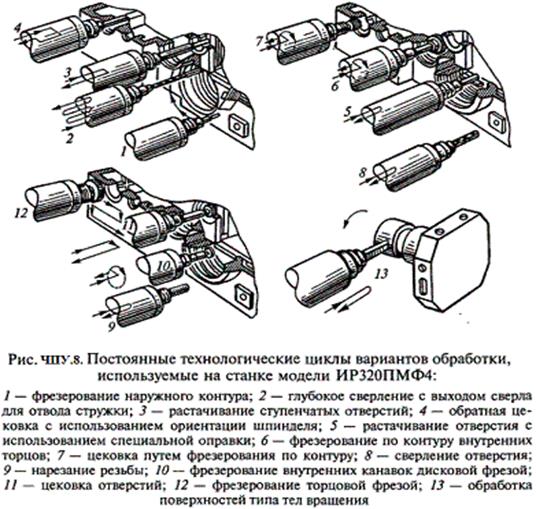
МС имеют следующие характерные особенности: наличие инструментального магазина, обеспечивающего оснащенность большим числом режущих инструментов для высокой концентрации операций (черновых, получистовых и чистовых), в том числе точения, растачивания. фрезерования, сверления, зенкерования, развертывания, нарезания резьбы, контроля качества обработки и др.; высокая точность выполнения чистовых операций (6...7-й квалитеты).
Для систем управления МС характерны сигнализация, цифровая индикация положения узлов станка, различные формы адаптивного управления. МС -это в основном одношпиндельные станки с револьверными и шпиндельными головками.
|
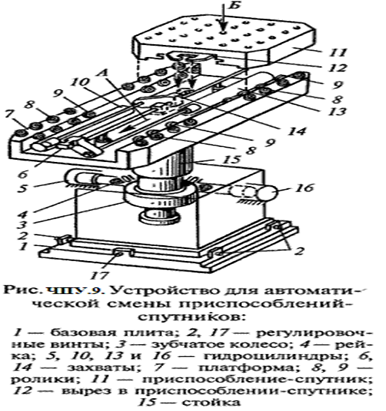
Многоцелевые станки (обрабатывающие центры) для обработки заготовок корпусных деталей. МС для обработки заготовок корпусных деталей подразделяют на горизонтальные (рис.2 ) и вертикальные(рис.58).
Обработка заготовок на МС по сравнению с их обработкой на фрезерных, сверлильных и других станках с ЧПУ имеет ряд особенностей. Установка и крепление заготовки должны обеспечивать ее обработку со всех сторон за одну установку (свободный доступ инструментов к обрабатываемым поверхностям), так как только в этом случае возможна многосторонняя обработка без переустановки.
Обработка на МС не требует, как правило, специальной оснастки, так как крепление заготовки осуществляется с помощью упоров и прихватов. МС снабжены магазином инструментов, помещенных на шпиндельной головке, рядом со станком или в другом месте. Для фрезерования плоскостей используют фрезы небольшого диаметра и обработку производят строчками. Консольный инструмент, применяемый для обработки неглубоких отверстий, имеет повышенную жесткость и, следовательно, обеспечивает заданную точность обработки. Отверстия, лежащие на одной оси, но расположенные в параллельных стенках заготовки, растачивают с двух сторон, поворачивая для этого стол с заготовкой.
Если заготовки корпусных деталей имеют группы одинаковых поверхностей и отверстий, то для упрощения составления технологического процесса и программы их изготовления, а также повышения производительности обработки (в результате сокращения вспомогательного времени) в память УЧПУ станка вводят постоянные циклы наиболее часто повторяющихся движений (при сверлении, фрезеровании). В этом случае программируется только цикл обработки первого отверстия (поверхности), а для остальных - задаются лишь координаты (X и Y) их расположения.
В качестве примера на рис.3 показаны некоторые постоянные технологические циклы, включенные в программное обеспечение и используемые при обработке на станке модели ИР320ПМФ4.
Устройство для автоматической смены приспособления-спутника (ПС) на станке модели ИР500МФ4 показано на рис.4. ПС 11 устанавливают на платформу 7 (вместимостью два ПС), на которой смонтированы гидроцилиндры 10 и 13. Штоки гидроцилиндров имеют Т-образные захваты 14 и 6. При установке на платформу (перемещение по стрелке Б) ПС вырезом 12 входит в зацепление с захватом 14 штока. На платформе ПС базируется на роликах 9 и центрируется (по боковым сторонам) роликам 8 (исходное положение ПС в позиции ожидания). Перемещение штока гидроцилиндра 10 обуславливает качение (по роликам) спутника. При движении штока гидроцилиндра 13 захват 6 перемещается (по направляющей штанге) и катит ПС по роликам 9 и 8 (в направлении стрелки А) на поворотный стол станка, где спутник автоматически опускается на фиксаторы. В результате захват 6 выходит из зацепления с ПС и стол станка (с закрепленным на нем спутником) на быстром ходу перемещается в зону обработки.
Заготовку закрепляют на спутнике во время обработки предыдущей заготовки (когда ПС находится в позиции ожидания) или заранее, вне станка. После того как заготовка будет обработана, стол станка автоматически (на быстром ходу) передвигается вправо к устройству для смены спутника и останавливается в таком положении, при котором фигурный паз ПС оказывается под захватом 6. Гидроцилиндр поворотного стола расфиксирует спутник, после чего ПС входит в зацепление с захватом 6, а масло поступает в штоковую полость гидроцилиндра 13, шток смещается в крайнее правое положение и перемещает спутник с заготовкой на платформу 7, где уже находится ПС с новой заготовкой. Чтобы поменять спутник местами, платформа поворачивается на 180° (на стойке 15) зубчатым колесом 3, сопряженным с рейкой 4, приводимой в движение гидроцилиндрами 5 и 16. Платформу 7 точно выверяют относительно поворотного стола станка с помощью регулировочных винтов 2 и 17, ввернутых в выступы базовой плиты 1, неподвижно закрепленной на фундаменте.
4.Оснастка и инструмент для многоцелевых станков с ЧПУ
РАСТОЧНЫЕ ГОЛОВКИ
Расточные головки японской компании NIKKEN применяются для растачивания отверстий в диапазоне диаметров от 3 мм до 595 мм. Уникальные технологии NIKKEN, используемые при изготовлении расточных головок обеспечивают их надежную работу. Низкое биение и высокая жесткость являются гарантией высокой точности обработки детали. Модульные расточные системы NIKKEN удобны при необходимости периодической смены инструмента.
Для получения идеальных результатов растачивания стали, нержавеющей стали и чугуна NIKKEN рекомендует использование расточных головок с оригинальными твердосплавными пластинками.
Расточные головки для ЧЕРНОВОГО растачивания RAC
Рис. 5. Расточные головки для ЧЕРНОВОГО растачивания
RAC
Диаметр обработки от 25 мм до 130 мм.
Гладкое растачивание с производительностью 250%.
Высокая жесткость.
Возможно изготовление расточных головок RAC со сквозным охлаждением.
Посадочная поверхность с точно обработанными зубцами.
Различные сменные насадки на расточную головку для обработки стали или нержавеющей стали, чугуна или алюминия и для сквозного растачивания.
Удобная шкала на головке для изменения диаметра растачивания.
Стандартные конусы BT-40, BT-50.
Возможно изготовление головок с конусом IT-40, IT-50.
Рис. 6. Пример 2-х шагового растачивания отверстия за один проход
Рис. 7. Полный контакт между сменной насадкой и расточной головкой
Расточные головки для ЧИСТОВОЙ расточки DJ
Рис. 8. Расточные головки для ЧИСТОВОЙ расточки DJ
Диаметр расточки от 3 мм до 50 мм.
Легкая установка микронной точности при помощи шкалы.
Возможно изготовление расточных головок DJ со сквозным охлаждением.
Сменные расточные резцы с твердосплавными пластинками для различных диаметров.
Возможно изготовление резцов повышенной жесткости из высокопрочной стали с карбидным стержнем.
Рекомендуемые режимы растачивания для различных материалов - в каталоге
Рис. 9. Удобная установка микронной точности на шкале
Рис. 10. Расточная головка со сквозным охлаждением
Расточные головки для ЧИСТОВОЙ расточки ZMAC
Рис. 11. Расточные головки для ЧИСТОВОЙ расточки ZMAC
Диаметр обработки от 16 мм до 180 мм.
Новая система двойного контакта обеспечивает высокую жесткость.
Поверхностное упрочнение кольца шкалы - специальная термообработка до HV800.
Возможно изготовление расточных головок ZMAC со сквозным охлаждением.
Легкая регулировка с точностью 3-5 мкм на диаметр обеспечивает высокоточную обработку и долговечность инструмента.
Высокоскоростное растачивание до 12000 об/мин специальными расточными головками из упрочненного сплава с системой балансировки для предотвращения вибрации.
Стандартные конусы BT-40, BT-50.
Возможно изготовление расточных головок с конусом IT-40, IT-50.
Рис. 12. Новейшая передовая система двойного контакта
Рис. 13. Удобная регулировка по шкале с микронной точностью
Расточные головки для растачивания БОЛЬШИХ ДИАМЕТРОВ
Рис. 14. Расточные головки для растачивания БОЛЬШИХ ДИАМЕТРОВ
Диаметр расточки от 130 мм до 595 мм.
Расточные головки для черновой и чистовой обработки больших диаметров.
Дополнительные аксессуары для расточных головок (фиксирующие винты, ключи, крепежная планка для сменных картриджей и т.п.)
Стандартные конусы BT-40, BT-50.
Возможно изготовление расточных головок с конусом IT-40, IT-50
Модульные расточные системы
Рис. 15. Модульные расточные системы
Модульные расточные системы представляют собой универсальный набор оправок, позволяющий собрать расточную головку практически для любого вида расточных работ - оправки для черновой и чистовой обработки, для глубокого растачивания и для обработки больших диаметров.
Благодаря системе двойного контакта достигается высокая жесткость оправки из-за отсутствия микровибрации. В результате увеличивается долговечность инструмента и достигается более высокая точность обработки. Повторяемость сборки модульной расточной системы с точностью до 3 мкм.
СВЕРЛИЛЬНЫЕ ЦАНГОВЫЕ ПАТРОНЫ
Сверлильные цанговые патроны японской компании NIKKEN компактны, обладают высокой точностью и высокой жесткостью. Жесткая и компактная конструкция сверлильных патронов NIKKEN устраняет проблемы ослабления посадки патрона на конусе, приводящие к повышенному биению или поломке инструмента.
Рис. 16. Сверлильные цанговые патроны BT-NPU
Сверлильные цанговые патроны BT-NPU
Биение не более 0,04 мм.
Сила закрепления инструмента в 3 раза выше при использовании специального ключа для затягивания патрона.
Возможно применение охлаждения через инструмент для сверл, диаметром свыше 6 мм.
Диаметр цанг 0,3 мм - 13 мм.
Стандартные конусы BT30, BT40, BT50.
Возможно изготовление оправок с конусом IT40, IT50
Дополнительные аксессуары и принадлежности для сверлильных патронов NIKKEN:
Рис. 17. Цанга
Рис. 18. Ключ для патрона
Адапторы для сверлильных цанговых патронов NIKKEN
Рис. 19. Адапторы для сверлильных цанговых патронов NIKKEN
Адапторы NIKKEN для сверлильных цанговых патронов представляют собой переходники с конусов BT30, BT40, BT50 на конусы по DIN (B6, B10, B12, B16, B18) или JACOBS (JT2, JT6). Возможно изготовление адапторов с конусом IT40 или IT50.
Адапторы для сверлильных патронов поставляются без патрона.
Площадь контакта конуса более 80% гарантирует надежное сверление, не сопровождаемое вибрацией или дребезжанием.
ФРЕЗЕРНЫЕ ПАТРОНЫ
Конструкция фрезерных патронов японской компании NIKKEN запатентована во многих странах мира. Благодаря очевидным достоинствам патроны NIKKEN используются на многих предприятиях по всему свету.
Фрезерный патрон NIKKEN
Рис.20. Фрезерный патрон NIKKEN
Патрон запатентован в Японии, Германии, США, Великобритании, Франции, Италии, Испании, Корее, Тайване.
Двойная жесткость увеличивает возможности при резании.
Биение инструмента в пределах 5 мкм на вылете 3 диаметров.
Стандартные конусы BT30, BT35, BT40, BT45, BT50.
Использование фрез от 2 до 32 мм.
Высокоскоростной фрезерный патрон NIKKEN
Рис. 21. Высокоскоростной фрезерный патрон NIKKEN
Максимальная скорость вращения до 40000 об/мин.
Возможна подача СОЖ под высоким давлением через патрон при использовании цанг CCK.
Стандартные конусы BT30, BT40, BT50.
Закрепление и ослабление гайки патрона производится специальным ключом GH.
Фрезерный патрон MINI-MINI CHUCK
Рис. 22. Фрезерный патрон MINI-MINI CHUCK
Патроны MINI-MINI CHUCK идеальны для использования концевых фрез малого диаметра.
Высокая скорость вращения до 30000 об/мин.
Высокая точность обработки: осевое биение на вылете 4-х диаметров не более 3 мкм.
Зажим инструмента у края патрона.
Стандартные конусы BT30, BT40, BT50.
Фрезерные патроны SLIM CHUCK
Рис. 23.Фрезерные патроны SLIM CHUCK
Фрезерные патроны SLIM CHUCK с подшипником скольжения TiN Bearing Nut. Корпус патрона небольшого диаметра обеспечивает обработку в труднодоступных местах.
Высокая скорость вращения: до 40000 об/мин.
Tin Bearing Nut обеспечивает жесткость при резании и возможность прецизионной чистовой обработки.
Высокая точность обработки: осевое биение на вылете 4-х диаметров не более 3 мкм.
Стандартные конусы BT30, BT40, BT50.
Возможно использование патронов SLIM CHUCK со сквозной подачей СОЖ.
РЕЗЬБОНАРЕЗНЫЕ ПАТРОНЫ
Резьбонарезные патроны японской компании NIKKEN используются для нарезания метрической, дюймовой и трубной резьбы диаметром от 2 до 100 мм. Кулачковый механизм с вращающимся подшипником обеспечивает точность, высокую чувствительность и долгий срок эксплуатации резьбонарезного патрона. Внешний диаметр патрона настолько мал, насколько это возможно. Только резьбонарезные патроны NIKKEN обеспечивают нарезание резьбы большого диаметра патроном с небольшим внешним диаметром.
Резьбонарезной патрон NIKKEN
Рис. 24.Резьбонарезной патрон NIKKEN
Широко примененяется для нарезания трубной резьбы, глухой резьбы и для нарезания резьбы в легких сплавах. Резьбонарезной патрон с возможностью выдвижения и втягивания метчика, расчитанной на компенсацию разности между подачей станка и шагом метчика.
Диаметр нарезаемой резьбы от М2 до М100 (метрическая), от 1/8 до 33/8 (дюймовая) и от 1/16 до 31/4 (трубная).
Стандартные конусы BT30, BT40, BT50.
Возможно изготовление патронов с конусом IT-40, IT-50.
Цанги для резьбонарезных патронов
Рис. 25. Цанга для резьбонарезного патрона
Рис. 26. Цанга с ограничителем момента для резьбонарезного патрона
Рис. 27. Удлиненная цанга для резьбонарезного патрона
Все цанги могуть быть использованы с любым типом самовыдвижного патрона для нарезания резьбы.
Кроме указанных выше, NIKKEN выпускает Синхронизированные резьбонарезные патроны, нарезающие один виток резьбы за один оборот шпинделя. К таким патронам поставляются цанги без механизма ограничения крутящего момента.
ИЗМЕРИТЕЛЬНАЯ ОСНАСТКА
Приборы, инструменты и оснастка для определения размеров - датчики положения, центроискатели, кромкоискатели, индикаторы, приборы для измерения инструмента.
Японская компания NIKKEN выпускает широкий спектр оснастки и приборов для определения геометрических размеров деталей и инструмента, а также центроискателей, датчиков положения и т.п. Измерительные приборы и оснастка NIKKEN отличается высокой точностью измерений, надежностью и простотой в эксплуатации.
3D Электронный измеритель размера (кромкоискатель, датчик касания). Universal Micro Touch.
Рис. 28. 3D Электронный измеритель размера (кромкоискатель, датчик касания). Universal Micro Touch
Прецизионный датчик касания. Повторяемость измерений ± 2 мкм.
Большой ход контактной головки без опасности повреждения: по оси X,Y= ± 7 мм, по оси Z= 3 мм.
Красная лампа и звуковой сигнал сигнализируют о касании. При касании немедленно загарается красная лампа, хорошо заметная с любой стороны датчика.
Контактная головка датчика подводится к кромке детали (для определения ее координат) либо подводится к двум поверхностям для измерения размера. Таким образом возможно измерение высоты, ширины паза, наружного и внутреннего диаметров, определение центра внутреннего диаметра и определение координат кромки детали.
Рис. 29. Схема работы 3D электронного измерителя размера. Universal Micro Touch.
Рис. 30. 3D Электронный измеритель размера (кромкоискатель, датчик касания). Universal Micro Touch
Мгновенная индикация красным светодиодом при очень легком контакте сенсорной головки с деталью.
Идеально подходит для определения центра (Центроискатель) на фрезерных, сверлильных, расточных станках и обрабатывающих центрах.
Повторяемость измерений в пределах 2 мкм.
Защитный механизм против ударов на высокой скорости. Шарик вытягивается на пружине (рисунок 30). Легкая проверка положения относительно поверхности заготовки.
Рис. 31. Схема работы электронного высокочувствительного датчика положения с функцией центроискателя. Touch Point (Electronic sensor)
Рис. 32. Универсальный стрелочный индикатор. Universal Micro Touch
Универсальный стрелочный индикатор модели UDS-1 на магнитном основании позволяет свободно перемещать стрелочный индикатор в пространстве, закрепляя его в нужном положении специальным механизмом. В горизонтальном положении максимальная длина рычага 300 мм. Возможность производить замеры на наружном и внутреннем диаметре, торца и заднего торца и т.д. Магнит в основании Индикатора может быт отключен для его безопасного перемещения.
Рис. 33 Универсальный стрелочный индикатор. Universal Micro Touch
Универсальный стрелочный индикатор модели UDS-2 на чугунном утяжеленном основании, изготовленном с высокой точностью. На основании имеется регулировочный винт для точной регулировки.
Основание с магнитом позволяет закреплять индикатор в различных положениях:
Рис. 34 Универсальный стрелочный индикатор. Universal Micro Touch
Рис. 35. Измеритель высоты. Hight Presette r
Нет необходимости в пробном резании!
Длина инструмента может быть измерена очень быстро и с высокой точностью без повреждения рабочей кромки сверла, фрезы или резца.
Надежное закрепление измерителя на магнитном основании (700Н) делает возможным измерение в ручном режиме на вертикальных и горизонтальных обрабатывающих центрах, а также на токарных станках.
Магнит в основании может быть отключен для безопасного перемещения Измерителя высоты.
Рис.36.Примеры использования Измерителя высоты.
Рис.37.Прибор для измерения инструмента. Tool Presetter.
Micro Tool Presetter , модели NMP-40N и NMP-50N.
Улучшение точности измерений благодаря использованию NIKKEN специальных подшипников.
Простое управление : быстрое измерение размера с точностью 0,001 мм, простой механизм.
Различные функции : выбор измерения диаметра/радиуса на дисплее, установка нуля, измерения в мм/дюймах, удержание в памяти, ввод значений для предустановки, дисплей для минимальных/максимальных значений измерения, проверка допуска и т.д.
Параметр | NMP-40N | NMP-50N | |
Диапазон измерений | Х (D) Z (L) |
D= 0 - 200 мм L= 0 - 300 мм |
D= 0 - 300 мм L= 0 - 400 мм |
Точность измерений | Ось X Ось Z |
0,01/0,001 мм избирательно (диаметр) 0,01/0,001 мм избирательно |
|
Шпиндель | ISO 40 | ISO 50 | |
Питание | Батарейка CR2032 (2 шт) | ||
Вес, кг (Размеры, мм) | 21 кг (760х480х300) | 35 кг (950х580х390) |
Рис.38.Жидкокристаллический дисплей.
Рис.39. Tool Presetter
Tool Presetter, модели NTP300, NTP400, NTP500.
Прибор для измерения инструмента с полным набором функций обеспечит увеличение производительности работы для высокопроизводительного дорогого обрабатывающего центра.
Быстрое перемещение обеспечивается двумя двигателями.
Пневматическое устройство закрепления инструмента гарантирует надежное измерение и высокую точность.
Высокоточная шкала по обеим осям.
Параметр | NTP300XZ-50(40) | NTP400XZ-50(40) | NTP500XZ-50(40) | |
Диапазон измерений | Х (D) Z (L) |
D= 0 - 300 мм L= 50 - 500 мм |
D= 0 - 400 мм L= 50 - 500 мм |
D= 0 - 500 мм L= 50 - 600 мм |
Точность измерений | Ось X Ось Z |
0,002 мм (диаметр) или 0,001 мм (радиус) 0,001 мм |
||
Шпиндель | BT30/40/50 или IT40/50 | |||
Питание | 100 В; 0,5 кВА | 220В; 1,2 кВА | ||
Вес, кг (Размеры, мм) | 300 кг (1220х950х1850) |
400 кг (800х1200х1900) |
700 кг (1800х1400х2400) |
Рис.40.Цифровой дисплей.
ОПРАВКИ С ПОДАЧЕЙ СОЖ
Японская компания NIKKEN выпускает два вида оправок с подачей СОЖ: со сквозной подачей через оправку и с подачей СОЖ через фланец.
Рис.41.оправка NIKKEN со сквозной подачей СОЖ
Рис.42.оправка NIKKEN с подачей СОЖ через фланец
Оправки NIKKEN могут использоваться при подаче СОЖ под высоким давлением (до 7 МПа). Они используются в стандартных сверлильных патронах, фрезерных патронах, а также в оригинальных патронах NIKKEN: SLIM CHUCK, MINI-MINI CHUCK, DREAM-CUT HOLDER.
Фрезерный патрон NIKKEN с подачей СОЖ
Рис.42.Фрезерный патрон NIKKEN с подачей СОЖ
• Максимальное давление СОЖ - 7 МПа.
Патрон SLIM CHUCK с подачей СОЖ
Рис .43.Патрон SLIM CHUCK с подачей СОЖ
• Максимальное давление СОЖ - 7 МПа.
• Простой дизайн, малый диаметр патрона.
• Высокая скорость вращения.
• Высокая точность.
Оправка DREAM-CUT HOLDER с подачей СОЖ
Рис.44. Оправка DREAM-CUT HOLDER с подачей СОЖ
• Максимальное давление СОЖ - 7 МПа.
• Эффект гашения вибрации.
• Высокая скорость.
Патрон MINI-MINI CHUCK с подачей СОЖ
Рис.45.Патрон MINI-MINI CHUCK с подачей СОЖ
• Максимальное давление СОЖ 7 МПа.
• Скорость вращения до 30000 об/мин, балансировка G2.5
• Биение в пределах 3 мкм.
Сверлильный патрон NIKKEN с подачей СОЖ
Рис.46.Сверлильный патрон NIKKEN с подачей СОЖ
• Максимальное давление СОЖ 1 МПа.
Опрпавка с боковым зажимом (для сверления)
Рис.47.Опрпавка с боковым зажимом (для сверления)
Максимальное давление СОЖ - 7 МПа.
ПОВОРОТНЫЕ СТОЛЫ CNC
Японская компания NIKKEN , без преувеличения является мировым лидером по производству станочных поворотных столов . Исключительная надежность, безупречное качество и длительный срок эксплуатации - вот те качества, благодаря которым столы NIKKEN заслужили признание во всем мире.
Поворотные и поворотно-наклонные столы позволяют добавить одну или две контролируемые оси к существующему станку. CNC столы NIKKEN для станков и обрабатывающих центров благодаря своему высокому качеству допускают работу под нагрузкой в течении 24 часов в сутки.
Червяк из высококачественной углеродистой стали прекрасно работает при высоких скоростях вращения.
Червячное колесо поворотных столов NIKKEN изготовлено из специальной стали, а зубья подвергнуты ионному азотированию. Твердость поверхности зубьев червячного колеса - HV-930 (на глубину 0,1 мм), твердость сердцевины зуба - HRC36. Такая обработка обеспечивает восприятие поворотным столом высоких нагрузок на протяжении длительного времени без ухудшения качества и точности обработки детали.
По сравнению с поворотными столами, в которых установлены червячные колеса из традиционных материалов (фосфористая бронза, алюминевая бронза), столы NIKKEN обладают более высокой стойкостью к нагрузкам и гораздо большей долговечностью. Степень износа червячной передачи NIKKEN во много раз ниже аналогичной других производителей, изготовленной, например, из фосфористой бронзы (см рисунок).
Рис.48.Степень износа червячной передачи NIKKEN
Опыт компании NIKKEN в разработке зубчатых зацеплений и глубокое изучение работы колесно-червячной пары позволили создать высокоскоростные поворотные столы со скоростью вращения планшайбы до 44,4 об/мин. Вращение червячного винта создает масляную пленку, препятствующую контакту металл-металл, удаляющую продукты износа, позволяющую получить высокую жесткость системы и добиться высокой износоустойчивости.
Компания NIKKEN использует в создании поворотно-наклонных столов технологии, запатентованные в Японии, США и Европе. Благодаря этим новейшим разработкам, 5-и осевые столы NIKKEN отличаются от аналогов отсутствием вибрации при любом угле наклона и прекрасно подходят для одновременной многоповерхностной обработки деталей, включая силовое сверление и торцевое фрезерование.
Условно поворотные и поворотно-наклонные столы NIKKEN можно разделить на несколько типов. Вот некоторые из них:
Рис.49.Горизонтальный поворотный стол NIKKEN
Рис.50.Поворотный стол NIKKEN
Рис.51.Поворотный стол с возможносью наклона вручную от 0° до 90°.
Рис.52.Поворотный стол с задним расположением двигателя.
Рис.53.Поворотно-наклонный стол NIKKEN (5-и осевой поворотный стол).
Рис.54.Поворотный стол высокой жесткости и точности.
Рис.55.Многошпиндельный поворотный стол NIKKEN.
Рис.56.Поворотный стол с верхним расположением двигателя.
Рис.57.Многошпиндельный поворотно-наклонный стол NIKKEN (многошпиндельный 5-и осевой поворотный стол).
NIKKEN выпускает круглые столы различных размеров и с разными характеристиками. Начиная от компактных поворотных столов с диаметром планшайбы от 105 мм (вес стола всего 30 кг), заканчивая горизонтальными поворотными столами с диаметром планшайбы до 1200 мм, весом 1300 кг.
Максимальная скорость вращения для некоторых моделей столов - 44,4 об/мин. Высокоскоростные поворотные столы серии Z подходят для высокоскоростного фрезерования поверхности лопаток турбин.
Внешние присоединительные размеры столов могут быть различными в зависимости от типа привода.
5.Серия Mynx NM (Doosan)
Рис.58. серия Mynx NM (Doosan )
Новый стандарт конструкции вертикальных обрабатывающих центров, обеспечивающий повышенную производительность, высокую точность и непревзойденные рабочие характеристики.
Техническая информация
Модели: | NM410HS | NM510HS |
Размеры станка | ||
Вес станка (Килограммы) | 5000 | 7000 |
Высота станка (Миллиметры) | 2930 | 3130 |
Габариты станка (Миллиметры) | 2390x2140 | 2600x3200 |
Источник питания | ||
Подача сжатого воздуха (Мега Паскаль) | 0.54 | |
Элекропитание (номинальная мощность) (Киловольт-ампер) | 39.5 | 52 |
Подача | ||
Диапазон рабочих подач (Миллиметры в минуту) | 24000 | 22500 |
Ускоренное перемещение по оси X, Y, Z. (Метры в минуту) | 48/48/48 | 48/48/45 |
Перемещение по осям | ||
по оси X (Миллиметры) | 762 | 1020 |
по оси Y (Миллиметры) | 410 | 510 |
по оси Z (вперед/назад), ползун (Миллиметры) | 510 | 625 |
Расстояние от оси шпинделя до колонны (Миллиметры) | 457 | 557 |
Расстояние от торца шпинделя до поверхности стола (Миллиметры) | 150-660 | 150-775 |
Рабочий стол | ||
Грузоподъёмность стола. (Килограммы) | 600 | 800 |
Рабочая поверхность (-) | 4-125x18H8 | |
Размеры (Миллиметры) | 920x430 | 1200x500 |
Автомат смены инструмента (АСИ) | ||
Вес инструмента макс. (Килограммы) | 8 | |
Время смены инструмента (стружка-стружка) (Секунды) | 3.6 | 3.9 |
Время смены (инструмент-инструмент) (Секунды) | 1.5 | |
Ёмкость инструментального магазина (-) | CAM30 | |
Максимальная длина инструмента (Миллиметры) | 300 | |
Максимальный диаметр инструмента (Миллиметры) | 90 | 87 |
Максимальный диаметр инструмента без соседних (Миллиметры) | 150 | |
Метод выбора инструмента (-) | memory random | |
Тип хвостовика инструмента (-) | MAS403 BT40 | |
Шпиндель | ||
Конус шпинделя (-) | SO #40 7/24Taper | |
Крутящий момент шпинделя (Оборотов в минуту) | 60 | 166.6 |
Скорость шпинделя (Оборотов в минуту) | 20000 | 15000 |
Емкость бака | ||
Подача СОЖ (Литры) | 250 | 300 |
Смазка (Литры) | 1.8 | |
Двигатели | ||
Двигатель подачи (X/Y/Z) (КилоВатты) | 3.0/3.0/4.0 | 4.0/4.0/7.0 |
Мощность привода шпинделя (КилоВатты) | 18.5 | 22 |
Рис.59.Техническая информация
6.Организация работы оператора многоцелевых станков с ЧПУ
Функции обслуживающего персонала на станках с ЧПУ сводятся к установке, закреплению и выверке приспособлений и инструмента, вводу программ или к установке программоносителей и заготовок, замене режущего инструмента, снятии обработанных деталей и наблюдению за работой станка. На МС с ЧПУ смена режущего инструмента автоматизирована.
Как правило, станки с ЧПУ обслуживают оператор и наладчик, между которыми возможны два варианта распределения обязанностей. По первому варианту наладку, переналадку и одналадку выполняет наладчик, а оперативную работу и контроль за работой станка - оператор. По второму варианту наладку и переналадку осуществляет наладчик, а подналадку, оперативную работу и контроль за работой - оператор.
Функции наладчика более сложны и обширны, чем оператора. В них входят приемка и осмотр оборудования, подготовка инструмента и приспособлений к наладке, ввод управляющей программы, наладка, подналадка и контроль исправности оборудования, инструктаж рабочего-оператора.
Оператор для обеспечения безопасности труда обязан соблюдать правила, характерные для конкретных видов работ.
Перед началом работы оператор должен:
проверить работоспособность станка, а для этого с помощью тест - программ проконтролировать работу устройства ЧПУ и самого станка, убедиться в подаче смазки, в наличии масла в гидросистеме, проверить работу ограничивающих упоров;
проверить надежность закрепления приспособлений и инструментов, соответствие заготовки требованиям технологического процесса, отклонение от точности настройки нуля станка (не должно превышать норму); отклонение по каждой из координат, а также биение инструмента в шпинделе станка;
перед началом работы по программе включить автомат "Сеть", установить заготовку и закрепить ее, ввести в УЧПУ управляющую программу, заправить магнитную ленту или перфоленту в считывающее устройство, нажать кнопку "Пуск" и обработать первую заготовку по программе. Проверить качество обработки первой заготовки на соответствие чертежу.
Не допускается устанавливать и обрабатывать на станке заготовки, масса которых превышает допустимую массу, указанную в паспорте станка.
Габаритные размеры и планировка помещений должны обеспечивать свободный доступ ко всем уздам и устройствам станков с ЧПУ во время их работы.
Одним из непременных условий, обеспечивающих безопасность труда оператора станков с ЧПУ , является освещенность помещения (200 лк при люминесцентных лампах и 150 лк при лампах накаливания). Уровень освещенности для станков с ЧПУ классов точности В и А должен быть еще выше.
7.Технологии обработки деталей на многоцелевых станках с ЧПУ
1. Назначение технологического процесса . При обработке деталей на станках с ручным управлением операционный процесс предназначен для рабочего, обслуживающего станок.
Полнота разработки этого процесса технологами зависит от типа производства. При массовом производстве техпроцесс разрабатывается наиболее полно, при серийном производстве степень детализации уменьшается, а при единичном производстве операционный технологический процесс представляется технологами исполнителям схематически или не представляется вовсе.
Имеется в виду, что универсальный станок обслуживает рабочий высокой квалификации, который самостоятельно способен выбрать инструмент, приспособления, режимы резания и порядок обработки заготовки и обеспечить требуемое качество детали.
Во всех случаях действия технолога корректирует рабочий, обслуживающий станок. Если изменились условия обработки (вид заготовки, припуск на обработку, вид оборудования или инструментальной оснастки и др.), рабочий самостоятельно так изменяет параметры технологического процесса, чтобы обеспечить выполнение конечной цели — получение годной детали.
Положение изменяется, если рассматривать станок с ЧПУ.
Техпроцесс предназначен в этом случае для программиста, который составляет управляющую программу. Отсюда вне зависимости от величины серии требуется весьма тщательная проработка всех элементов техпроцесса, включающая траекторию инструмента. Вся работа выполняется до обработки на стадии программирования.
Это требует развитую нормативную базу для обоснованного выбора всех элементов технологического процесса :
станка с ЧПУ;
режущего инструмента (материала, типа, размера, конструкции и геометрии);
вспомогательного инструмента;
приспособлений;
структуры техпроцесса;
режимов резания;
норм времени;
квалификации рабочего и др.
2. Роль рабочего. Качество изделия и производительность обработки при обслуживании станков с ручным управлением определяются квалификацией рабочего, обслуживающего станок.
При использовании станков с ЧПУ качество обработки зависит от качества управляющей программы. Отсюда снижаются требования к квалификации рабочего, облегчается его подготовка, сокращается срок обучения. Это важное преимущество станков с ЧПУ при остром дефиците рабочих - станочннков.
Но одновременно повышаются требования к качеству программ. Эффективное использование станков с ЧПУ предъявляет высокие требования к службе подготовки управляющих программ.
3. Полуавтоматический цикл обработки. При обслуживании станков с ручным управлением (рис. 60) оперативное время (время цикла)
=
+
где — машинное время,
— вспомогательное время.
Автоматы имеют длительность цикла =
+
где — время рабочих ходов,
— время холостых ходов.
Обозначим =
*
;
=
*
;
Где и
— доля вспомогательных и холостых ходов во времени цикла.
Пусть =
. Тогда повышение производительности при обработке на автомате только за счет сокращения холостых ходов составит
=
Рис.60. Цикл обработки при различной степени ее автоматизации
Пусть ≠0,6—0,7 ;
=0,1.
Повышение производительности — в 2,57 раза.
Станок с ЧПУ работает по полуавтоматическому циклу. У него различают время рабочих и холостых ходов и вспомогательное время (), необходимое для загрузки станка. Программное время
=
-
Суммарное время холостых и вспомогательных движений =
+
При =
повышение производительности по сравнению с универсальными станками равно
=
,
где и
— вспомогательное время на станках с ручным управлением и станках с ЧПУ.
Пусть =0,6—0,7;
=0,1;
= 0,15. Повышение производительности—в 2,15 раза.
Полуавтоматический цикл означает, что рабочий должен быть освобожден от непосредственного участия в процессе обработки.
Для этого требуется:
· высокая надежность системы СПИД;
· стабильность процесса обработки.
4. Высокая надежность системы СПИД . Станок С, приспособление П, инструмент И и деталь Д в процессе обработки находятся в диалектическом единстве, образуют единую систему. Надежность любой системы выражается периодом безотказной работы — наработкой на отказ. Отказ выражается в том, что параметры системы выходят за допустимые пределы. Возникновение отказа требует вмешательства рабочего.
При обслуживании станка с ручным управлением рабочий постоянно контролирует ход технологического процесса, при появлении отказов рабочий немедленно вмешивается и восстанавливает требуемый ход процесса.
При наличии автоматического цикла рабочий не принимает непосредственного участия в ходе технологического процесса. Отсюда резко повышаются требования к надежности функционирования системы СПИД.
Станки с ЧПУ имеют более высокие нормы точности, им необходим более высокий уровень жесткости и надежности всех узлов и элементов.
5. Стабильность процесса обработки. Стабильность определяется размахом колебаний параметров системы СПИД.
К параметрам относятся прочность, жесткость, износ и другие свойства элементов системы СПИД, режимы резания, геометрия инструмента и т. д. В процессе обработки одной детали или партии указанные параметры не остаются постоянными. Чем меньше пределы изменения параметров, тем более стабильной является система СПИД.
При обработке деталей на станке с ЧПУ необходимо стабилизировать:
параметры заготовки (припуски, свойства материала, состояние поверхностного слоя и др.);
параметры инструмента (свойства материала, твердосплавной пластины, геометрию);
параметры станка (точность, жесткость, виброустойчивость и др.);
дробление стружки;
эффективную размерную настройку инструмента (вне станка на специальных приборах размерной настройки или на станке);
режимы резания и т. д.
6. Концентрация обработки. Принцип концентрации обработки заключается в том, чтобы весь объем обработки выполнить на одной или ограниченном числе операций.
При этом уменьшается число операций техпроцесса и, соответственно, затраты времени на транспортирование, складирование, установку и закрепление заготовок.
Наличие многопозиционных револьверных головок и инструментальных магазинов и возможность автоматической смены инструмента позволяют создавать такие инструментальные наладки, чтобы максимально концентрировать обработку на одной двух операциях.
На рис. 61 показаны:
а — заготовка;
б — заготовка после обработки с одной стороны;
в — готовая деталь;
г — инструментальная наладка для обработки детали.
Рис.61. Концентрация обработки
Список литературы
1. В.И. Комиссаров, Ю.А. Фильченок, В.В. Юшкевич. Размерная наладка станков с ЧПУ на роботизированных участках, Владивосток, ДВПИ, 1985.
2. Гжиров Р.И., Серебреницкий П.П. Программирование обработки на станках с ЧПУ. Справочник, Л., Машиностроение, 1990,-592с.
3. Общемашиностроительные нормативы времени и режимов резания для нормирования работ, выполняемых на универсальных и многоцелевых станках с ЧПУ. Часть II, М., Экономика, 1990г., -474с.
4. Интернет-сайт технической литературы www.bibt.ru
5. Интернет-сайт по многоцелевым станкам с ЧПУ www.cftech.ru
Похожие рефераты:
Разработка автоматизированного участка изготовления детали "Фланец"
Расчет и проектирование дискового долбяка и участка инструментального цеха
Автоматизированное проектирование станочной оснастки
Технология выполнения токарных работ
Обработка деталей на токарных одношпиндельных автоматах: инновационный аспект
Обработка деталей РЭС резаньем
Технологический процесс изготовления детали
Разработка технологического процесса изготовления детали с применением ГАП и ГПС